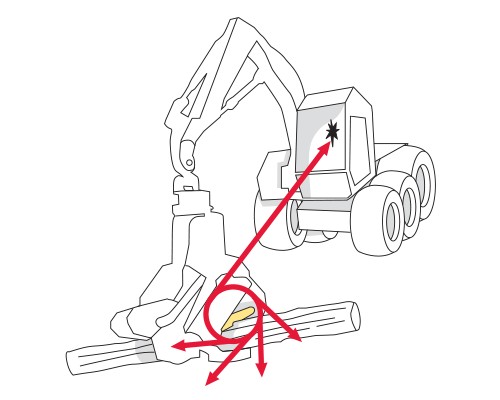
What is chain shot, how does it happen, and how do we ensue operator and bystander safety?
Oregon educates on harvester chain shot. Chain shot is the high velocity separation and ejection of a piece or pieces of cutting chain from the end of a broken chain in saw chain based mechanized harvesting systems. Chain shot potentially exposes both machine operators and bystanders to a risk of serious injury or death. Chain shot typically occurs near the drive end of the cutting system but can also come from the bar tip area.
First, the saw chain breaks. Second, after a saw chain break, the “free” end of the saw chain begins to whip away from the break. Third, if the saw chain is not contained by the saw box or a chain shot guard, the broken saw chain’s free end can speed up rapidly, carrying immense dynamic energy. Finally, at the peak of the whip, saw chain pieces may break loose and be ejected at high speed.
Although the "Shot Cone Zone" reflects the most likely chain shot path, deflections can occur, substantially expanding where chain pieces may travel. To minimize risk, operators should keep out of the Shot Cone Zone. Ground personnel and bystanders should be at least 230 feet away from cutting operations and out of the Shot Cone Zone.
The following best practices will increase your safety and the life of your cutting system. Do not use saw chain that:
- Has broken twice or is severely damaged.
- Has excessive saw chain stretch or has broken or cracked components.
- Has loose rivet joints—if you can rotate the rivets with your fingers, they are too loose.
Important operational recommendations are as follows:
- Never engage in a cut with yourself, ground personnel, or bystanders in the Shot Cone Zone.
- Always cut as close to the ground as possible to reduce the distance that any potential ejected pieces could travel.
- Your cutting systems operates in challenging environments and depend on sufficient lubrication to minimize wear and extend the life of operation.
In the next issue of Logging-on we will look at techniques to minimise the risk of a chain shot event. Source
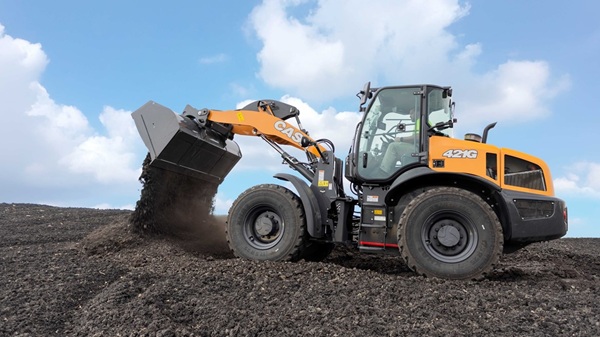
These include two new compact wheel loaders, motor graders with enhanced controls and a telescopic small articulated loader.
The new Case 421G compact wheel loader features a hydrostatic drive that enables attachments unavailable to larger machines. The hydraulic system with flow sharing and load sensing capabilities gives operators adjustable hydraulic flow and improves efficiency and overall fuel consumption. A high-flow hydraulic option is also available for crews who want to run special attachments like stump grinders or cold planers. And the hydrostatic transmission features shift-on-fly and auto-shift capabilities for seamless gear transitions and a smoother ride. Operators can continue working safely and more comfortably with the new cab structure of the 421G, which features more glass and seat-mounted controls for better all-around visibility. The cab also includes modern essentials like a customizable colour display with encoder, an in-display rear-view camera and a USB port and phone holder.
To help crews take on jobs with complex site plans more efficiently, Case is upgrading all M Series dozer models with a range of advanced control technologies to enable more precise cuts, fills and grades. Case also enhanced the hydraulic and electrical systems for simplified servicing, uptime and ease of use.
A brand-new Case D Series motor graders is being released. Engineered to make precision road building easier and featuring intuitive electro-hydraulic controls with 3-axis joysticks and an informative 8-inch touchscreen display, these new machines offer a whole new dimension of control for operators who need to meet precise specifications.
In terms of build and performance, the D Series motor graders leverage the same platform and drive system as their C Series counterparts to deliver the same outstanding performance. But a new in-cab layout with a range of improvements like a new keypad control and electronic handle throttle transforms the operator experience, while a new CASE SiteConnect™ modem enables advanced telematics to reduce downtime and service costs. Form more information on the other new and upgraded machines, visit the Case website Source
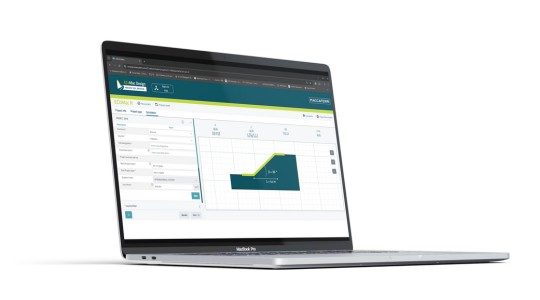
EcoMac is a suite of specialized tools designed to support engineers and professionals in developing advanced erosion control solutions.
Created to enhance precision and efficiency, EcoMac helps users design effective, sustainable systems for protecting slopes and channel banks from soil erosion while ensuring environmental compliance and structural reliability. The EcoMac suite includes three powerful tools:
- EcoMac R: Estimates soil loss using the Revised Universal Soil Loss Equation (R.U.S.L.E), evaluating erosion risks on unprotected slopes and recommending optimal solutions with reinforced geomats.
- EcoMac S: Defines the required tensile strength of geomats and anchorage spacing for slope stabilization.
- EcoMac B: Provides tailored anchorage solutions for protecting channel banks from erosion.
Integrated with eDesign, Maccaferri’s online project design platform, EcoMac offers a seamless, efficient experience. The eDesign platform includes a range of free, user-friendly software tools tailored for civil, geotechnical, and hydraulic engineering. With EcoMac embedded in eDesign, users can perform detailed analyses, select appropriate products, and optimize designs to meet their project requirements. Source
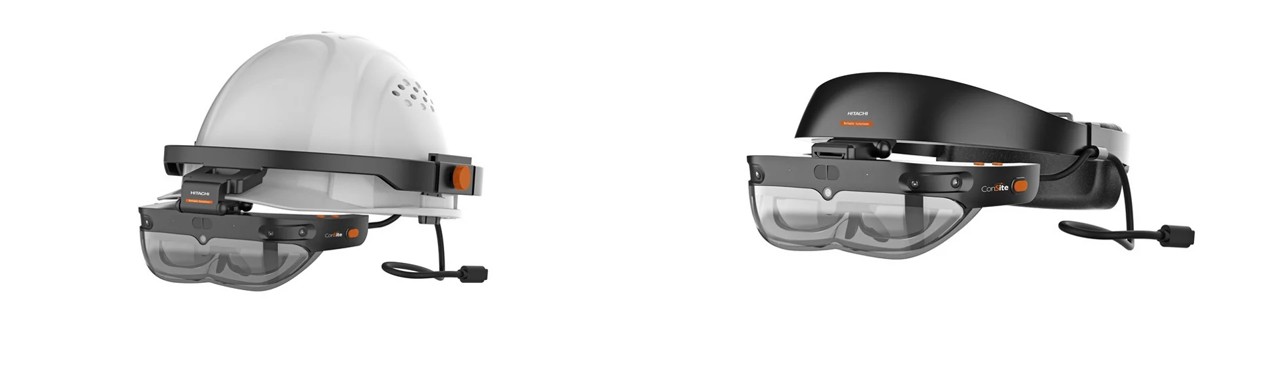
This allows technicians to receive remote support from their service desk with a visual aid.
Hitachi and Holo-Light have developed new-look XR smart glasses that are highly durable – watertight and dustproof – allowing technicians to receive remote support from their service desk with a visual aid, using XR technology that enables the combination of real and virtual spaces; and deliver fast and high-quality onsite service.
The current shortage of trained personnel to conduct service and maintenance work on construction and mining machinery is one of the main challenges facing the industry, and therefore the streamlining of inspection, repair and other related work is a priority. Technicians usually use multiple data sources – such as status reports, service manuals and parts catalogues – on smartphones and tablets. However, they face difficulties in operating mobile devices with their hands full, viewing multiple data sources and communicating with expert technicians through online calls.
The XR smart glasses are the solution to meet these challenges, despite previously being used mainly indoors, and with other issues concerning onsite durability and operational stability. The latest innovation has been developed in collaboration by Hitachi Construction Machinery and Hololight to provide the technology for streaming large amounts of data in a stable manner for long periods of time. The companies will continue to work together to enhance remote support functions and other solutions, as well as strengthen partnerships to supply the market.
The smart glasses have been awarded an IP65 rating – meaning that they are watertight and dustproof – and created with a robust design that can be used with confidence by technicians at construction sites and mines in all weathers. In addition, they can be attached to a safety helmet and utilise the XR streaming technology to overlay multiple screens on to the surrounding area – making it possible to operate with physical buttons and finger movements. The footage from the camera on the glasses also enhances the speed and quality of online support available from the service desk in the form of advice, documents and data. Source
A study is examining how different levels of delay impact performance in remotely controlled crane operation via VR
Remote control of forestry machines can improve the work environment for the operator. A well-functioning teleoperation system is also a step towards increased autonomy. Full autonomy, that could handle all possible situations the machine might encounter, requires extensive development. Teleoperation allows a gradual transition to autonomous functions. However, system delay is a critical factor in tasks that involve high speeds, such as crane operation. This study has therefore examined how remote control affects operator performance in a crane operation task. Operators performed the task using both teleoperation via a VR headset and conventional operation from the machine cabin. In the teleoperation setup, the task was performed both with the system's minimal inherent delay and with two levels of additional, artificial delay. The crane operation was a standardized task, where two logs were moved between two designated points on the ground and two positions in the machine's load area. The task is complex enough to include many critical handling operations while being controlled enough to allow repeated measurements for statistical analysis.
The operators achieved surprisingly comparable performance regardless of delay or whether they were operating remotely or from the cabin. However, at the higher delays of 150 ms and 200 ms, operators reported that the crane sometimes felt as if it got "stuck" during rapid adjustments. At delays between 200 ms and 600 ms, the experience shifted to where the crane became impossible to control normally. For comparison, latency in a 4G connection is usually under 50 ms.
The VR experience was generally positive, with the lack of vibrations and noise being especially appreciated. However, the stereoscopic vision was not entirely perfect, and in some situations, the crane's position occasionally appeared to shift suddenly by 1 to 2 meters (3 to 6 ft).
The results suggest that a forwarder crane operated remotely with VR can achieve performance comparable to that from the machine cabin. Performance remains unaffected even with delays that exceed those expected on a 4G connection, up to levels involving an additional 100 ms delay in the connection. Although the chosen camera positions and VR technology provide stereoscopic vision that facilitates crane operation, depth perception is not as accurate as with traditional in-cabin control.
Further research is needed to address all aspects of forwarding work under remote control, as well as to assess machine safety and working environment conditions. Source
Read MorePonsse release their Interim Report for 1 January - 31 March 2025
Ponsse indicated that the forest machine market picked up slightly during the first quarter of the year. Order intake totalled EUR 184.5 million. The order books turned to a slight increase at the end of the quarter, driven by the European market. Net sales increased positively by about nine per cent. The company’s euro-denominated operating profit is estimated to be slightly higher in 2025 than in 2024. Economic uncertainty is expected to continue and affect demand for forest machinery. Source
Stihl expands in Africa
Stihl has expanded its presence in Africa: With marketing companies in Morocco and Cameroon, the leading manufacturer of chainsaws and motorized garden tools wants to exploit the growth potential in the promising regions of North and Central Africa. Source
Read MoreTo see the full list of international logging, roading and trucking conferences and expo’s, please click the “Events” tab at the top of the page.
Read More