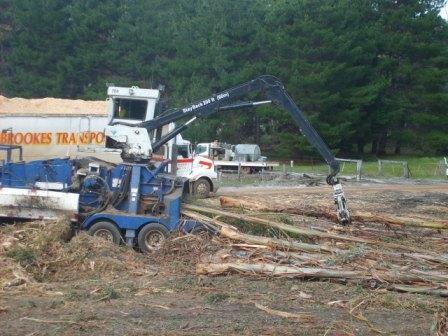
Hydraulic circuits refer the path taken by hydraulic fluid in a system. Open and closed circuit HST configurations refer to how the hydraulic lines in the system are connected:
- Open circuit – The fluid is brought into the pump via a reservoir and is then routed to the motor. It must then re-enter the reservoir after the motor. The pump supplies a continuous, constant flow of fluid. The fluid is not pumped to a high pressure, but the pressure of the fluid will rise when it encounters resistance. If this pressure rises too high, it will be returned to the reservoir via a pressure relief valve. These hydraulics normally cost less as they can use fixed displacement pumps.
- Closed circuit – The flow is uninterrupted as the fluid passes straight from the pump to the motor and back to the pump. This circuit supplies full pressure to the system at all times (creating a very responsive system). The pump will vary its flow rate in order to supply the constant pressure; therefore no path through the reservoir is required.
- Open loop – There is no feedback for speed, pressure, flow or torque regulation. If variable control settings are required, the operator must manually carry these out.
- Closed loop – This has feedback devices that allows communication between the pump and motor. This enables the HST to automatically adjust to different operating conditions of the load, engine or both.