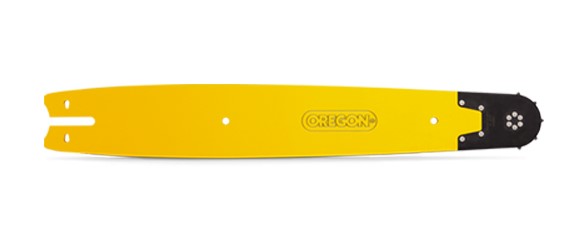
EnduraMax™ bars are versatile and fit a wide range of harvesting equipment.
The improved bar nose has longer wear life and is more durable in nose pinch situations. The optional Jet-Fit bar-mount system minimizes downtime and maximizes productivity. Jet-fit’s slotted motor-mount design fits harvester equipment outfitted with automatic chain tensioners and easily slides in and out of the bar clamp, saving up to 20 minutes when the operator needs to change the bar.
There is minimised rail wear, chipping, and spreading with Oregon’s specialized 3/8" thick high-grade alloy steel. This material allows the bars to hold their original form and resist bending even during heavy use. With slower wear these 60% longer lasting bars reduce the cost of operation. The new EnduraMax bars can be used on the same saw systems as the existing ¾” legacy bars.
All Oregon harvester guide bars are designed and built with the following features and benefits.
- High-Grade Steel: Featured on the 3/4" Pitch Solid Harvester RSN guide bar and double-ended guide bars for minimized rail wear, chipping, and spreading with Oregon’s specialized 3/8" thick high-grade alloy steel. New Enduramax Harvester bars are equipped with high-grade AR500 steel.
- LubriTec: This increases the life of the harvester guide bar and saw chain. The dam allows the chain drive links and oil to have closer contact, significantly reducing oil waste.
- Induction Hardening: On the traditional 3/4" bars - Increase the longevity of the guide bar with precision heat-treated rails. The induction hardening process offers good resistance to wear and chipping.
- Precision Groove: Maintain chain cutting stability and minimize wear. The straight and square-milled grooves are designed for consistency.
In additional, these extra harvester guide bar enhancements are available:
- Harvester Replaceable Sprocket Noses (RSN): Harvester Replaceable Sprocket Noses (RSN) extend the life of the guide bar body. The RSN’s strong and rigid design helps accelerate the return on the investment by increasing workload efficiency with quick and easy nose replacement in the field. New EnduraMax bars are equipped with a redesigned nose, not backwards compatible with ¾” legacy bars.
- Jet-Fit: The patented Jet-Fit bar-mount system maximizes productivity. The slotted motor-mount design fits harvester equipment outfitted with automatic chain tensioners and easily slides in and out of the bar clamp. The Jet-Fit is available in .080" gauge.
- Stump Spray: The patented Stump Spray guide bars help prevent the spread of butt and root-rotting fungi by delivering a precise cut and control agent application. With the custom channel along the bar’s leading edge, simply open the dimpled exit holes with the special punch-out to fit your need. Select models incorporate the Jet-Fit mounting tail slots. Source
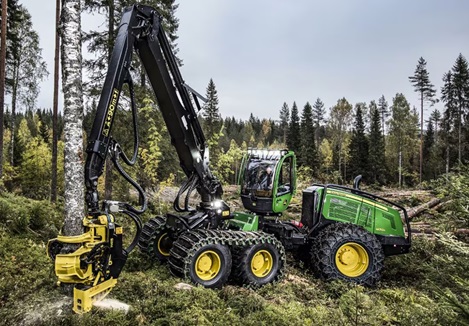
Simulator training helps provide safe and cost-effective training for operators of modern forestry machines.
The logging machines require high motor skills, constant concentration, and proper planning. Researchers aimed to analyse the learning curves of the trainees in order to determine the period during which most development takes place. In this study, 11 trainees were trained on a John Deere harvester simulator for approximately 15 hours each. In each case, a clear learning curve could be identified, despite high inter- and intra-person variability. Effective time showed a steady decrease during training, with a group minimum at the end of training. Crane tip distance per tree dropped rapidly in the first 3 to 4 hours, followed by a more gradual decrease. Crane control showed a significant increase by the 9th hour of training. Several crane functions used simultaneously increased more rapidly to almost a maximum value already in the 5th hour.
The individual curves for each trainee were highly variable, showing a wide range of values and shapes. In conclusion, most personal development occurs during the first phase of simulator training, which typically takes approximately 9 to 10 h. It is important to consider significant inter-personal variability and tailor the duration of simulator training to individual needs.
The research was published in Forests 2024, 15(8). The authors are Krzysztof Polowy and Dariusz Rutkowski. Source
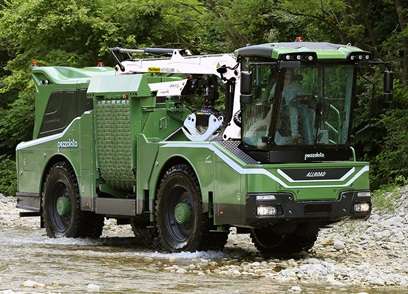
The chipper has maximum mobility due to a number of features.
The All Road has four driving wheels (Nokian 650-65 R38), and all steering, allowing three steering modes: both axles together, each axle individually or the front axle only. Two engines are available:
- Volvo Penta TWD 1683 engine (6 cylinders, 16 litres, 585 kW, 796 hp, 3650 Nm), and
- Caterpillar C18 engine (6 cylinders, 18 litres, 563kW, 755 hp, 3504 Nm) which does not require AdBlue.
The crane consists of a Palfinger Epsilon S110F104, with a reach of 10,1 m (33 ft) with a FG31R grapple and electric controls by means of joysticks. The crane is positioned at the very centre of the machine for better distribution of weight for both during transport and the working phase, avoiding abnormal twisting on the vehicle frame.
It has 4 stabilising feet, two with side exit, in order to optimize the machine stability and thus increase the operator’s comfort. It has a wide loading hopper especially designed for the processing of voluminous material, equipped with a feeding chain, 1400 mm (55 in) wide and positioned at 1050 mm (41 in) from the ground for faster loading operations, either with little piles or large stacks of wood.
Pezzolato’s closed drum, well known for its reliability and guaranteed to last the machine’s lifetime; designed to guarantee quality chips both small and big size. The drum weight is approximately 4500 kg (9,920 lb) and is staggered on the drum in order to better distribute the machine stress, decreasing vibrations, noise and fuel consumption.
The comfortable cabin can be adjusted in height and in all directions to improve the visibility of the loading area and of the unloading conveyor during the use of the crane. Wholly glassed and air-conditioned, it has all controls for total management of the machine during the machine movement and chipping phase.
It has optimized software that assures that the operator can displace the vehicle in the middle of the yard without stopping the chipping. It can also move automatically from the configuration on the road to the working one in less than 60 seconds.
The fan for the expulsion of the chips is hydraulically driven with a stepless change of speed so that the rpm can be adjusted according to the real needs, reducing consumption and the production of excessive fine chips. The speed, adjusted by the operator, is kept constant by the system, even if the r.p.m. of the main engine changes. The fan’s and unloading conveyor’s wearing parts are composed by wear proof plates including a standard steel base and some carbide units (CDP – Castodur Diamond Plates). Source
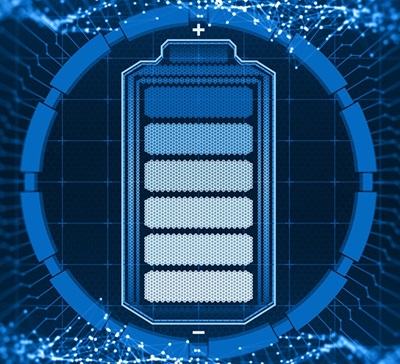
Cummins lets us dive into how cell voltage monitoring (CVM) works.
Fuel Cell Electric Vehicles (FCEVs) and Battery Electric Vehicles (BEVs) are at the forefront of advancing towards a more sustainable transportation industry. That is why, many manufacturers around the world are investing in both FCEVs and BEVs to develop technologies for lower emissions for commercial transportation. From fuel cells for long-range heavy-duty applications to battery electric drivetrains, companies are aiming to deliver integrated power solutions that optimize performance and efficiency. This article breaks down the concept of fuel cell stacks and batteries, focusing on the key facet of CVM that is vital for efficient fleet operation, reducing downtime and better maintenance of fuel cells and batteries.
CVM is a technology that monitors the voltage of each cell within a stack to ensure the system operates correctly. It is a monitoring system that measures and adjusts voltage based on how the cell is performing. It is like adjusting the vehicle's power output by pressing down on the pedal to accelerate a car to a desired speed.
Over time, however, cells in both batteries and fuel cells degrade, meaning they produce less voltage and, consequently, less power. This degradation requires systems to draw more electrical current to maintain the same level of power output. To mitigate this, advanced technologies like silicon carbide are used for semiconductors and control algorithms are tuned throughout the fuel cell’s life. CVM helps by measuring the voltage and allowing for adjustments to be made to maintain optimal performance. This monitoring is critical for predicting the lifespan of cells and ensuring the system's overall health.
Fuel cells and batteries are built from many smaller, individual cells that are combined to increase their power output. This approach is similar across various applications, whether it is the fuel cell stack in FCEVs, the batteries in BEVs, or the cells in electrolyzers, which are used to create hydrogen by splitting water using an electric current to separate its molecules into hydrogen and oxygen.
What is cell voltage? Think of a battery's voltage as its stored potential energy, like how water stored behind a dam holds it. Charging a battery is like filling the dam, while using a battery is akin to releasing water to generate electricity. For fuel cells and electrolyzers, applying current or introducing hydrogen fuel across a cell stack generates voltage, which then can be converted into power. This power can then be used to make a vehicle move. FCEVs, however, tend to operate at lower voltages compared to BEVs. A component called a boost DC-DC converter is therefore necessary to match the lower fuel cell output voltage to the battery's higher voltage.
However, FCEVs are hybrids and include fuel cells as well as a battery pack. This is because fuel cells have a response time lag, so they operate with a battery pack, in addition to the fuel cell stack. This compensates for the response time lag by providing instantaneous power. However, a smaller battery is used in FCEVs because the fuel cell continuously recharges it and supplies power, reducing the dependency on the battery for range. The batteries in FCEVs and pure BEVs could have similar technology and voltage, but those in FCEVs would have less total power.
CVM is crucial for several reasons. First, it can enable predictive maintenance, which helps in scheduling maintenance tasks before unexpected downtimes occur, reducing downtime and saving costs. Second, it enhances safety by ensuring that the system operates within its designed parameters, which prevents accidents and ensures systems do not malfunction.
Modern CVM systems can include embedded algorithms that analyze and sample data independently, making the overall voltage management system more intelligent. This capability helps in ensuring better control, safety, and a longer lifespan of the energy system, fuel cell or batteries. Source
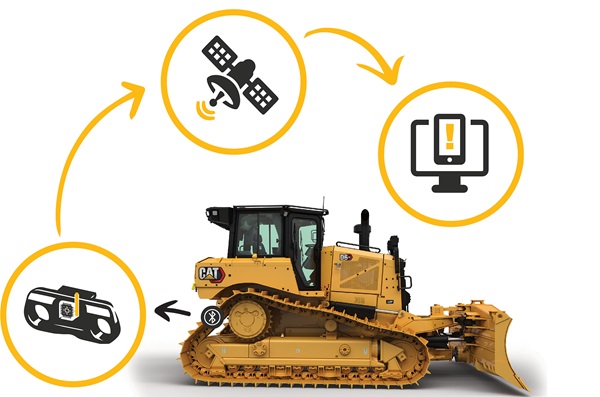
It also provides alerts at key wear percentages.
With 120 years of undercarriage experience, Caterpillar continues to innovate, so customers get the most from their investment. Exclusive to Cat® machines and undercarriages, the proprietary Cat Track Wear Sensor (CTWS) remotely monitors undercarriage wear to better predict wear out, plan maintenance and increase machine uptime.
Monitored within the Cat Wear Management System, the new CTWS wirelessly communicates critical track link wear information from the machine to the dealer for monitoring. Timed alert intervals – a 40% wear alert for possible bushing turns, 70% to signal for measuring and replacement part ordering, and 100% for required replacement – improve inspection scheduling and streamline ordering of replacement parts. The real-time track wear status enables no-touch track link measurements, increases fleet coverage by automating inspections, provides visibility to track wear when operating in remote locations and allows for prioritized timing of service visits by helping optimize manual inspections.
Field tested for proven reliability throughout the expected track life, more than 2,000 Cat machines have been shipped with the innovative sensor technology. The small electronic sensor installs in a customized pocket in the track link for protection. Each link assembly includes a smart link, resulting in two sensors on a machine, one on each side. The CTWS survives high frequency shock loads and meets sensor functional and environmental tests. Subject to operating conditions, sensor battery life has been shown to last up to seven (7) years.
The wear sensor is standard on new Cat D5, D6 and D8 dozers, and 953 and 963 track loader models in select regions with planned expansion to models in the dozer line in the future. It can be retrofitted on eligible dozer undercarriages. Source
Megawatt charging Milestone for Electric Trucks with up to 3000 kW
MAN Truck & Bus, the Technical University of Munich and other partners have presented the results of the Nefton charging infrastructure research project. The first public charging demonstration with over 1000 kW took place. The focus is already on charging capacities up to 3000 kW and bidirectional charging. The current capacity allows a 40 ton truck to travel 400km (250 mi) with a 30 min charge. But the public charging infrastructure expansion is urgently needed. Source
Doppstadt present their new SM 620.3 screening machine
Due to a variety of options and drums, the screening machine can be equipped for use in commercial waste, as well as for compost, bark, wood chips, building rubble, or excavated earth. With the new DualPower Smart Hybrid drive technology, switching between sites with power infrastructure and field locations is no problem. Low diesel consumption and high throughput capacity further enhance the list of benefits of this universal machine, along with a large feed hopper with a low loading edge and a stone grid that can fold over 90 degrees. Source
Read MoreTo see the full list of international logging, roading and trucking conferences and expo’s, please click the “Events” tab at the top of the page.
Read More