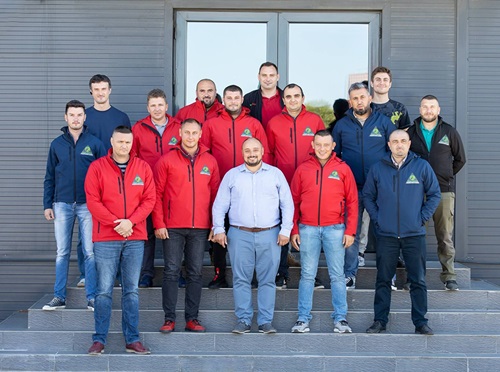
The additional support spans across three different continents.
Responsive after-sale support and technical expertise on the ground are critical factors to ensure successful high volume harvesting operations. To that end, Tigercat Industries is pleased to announce that Marcelo Antonio Pinto Goth has joined the Tigercat product support team in Chile. Assuming the role of factory support representative, Marcelo will be based in Concepción.
Marcelo is the third member of the Tigercat technical team in Chile, recruited in response to the fast-growing field population of Tigercat machines throughout the Chilean forestry regions. He will work closely with Tigercat dealer, Latin Equipment, focused on providing after-sale technical and operational support to Tigercat’s growing customer base.
Marcelo comes with a wealth of forest industry knowledge as well as the required technical expertise. He has eighteen years of direct experience with forestry equipment and a further sixteen years as a heavy equipment technician in the construction machinery sector.
Nick Whitman has been appointed to the position of product support representative. Based in Oxford, Arkansas, Nick will provide after-sale technical support in the southern US, including Alabama, Mississippi, Louisiana, Texas, Oklahoma and Arkansas.
Nick has a strong technical background with over nine years of experience working on heavy equipment as a technician and supervisor. He will be working closely with regional service manager John Withrow, product support representative Nicholas Edwards, and Tigercat district managers James Farquhar and Johnny Boyd.
Alser Power SRL based in Brașov is now representing the TCi equipment brand at the national level in Romania. Founder and director general, Albert Serban spent many years investigating and consulting on forest practices in Europe and Asia. Recognizing the strong potential of the Romanian forest industry, he founded Alser Power SRL in 2008. The company has grown into one of the largest forest equipment dealers in Romania, focused on strong customer support. Source
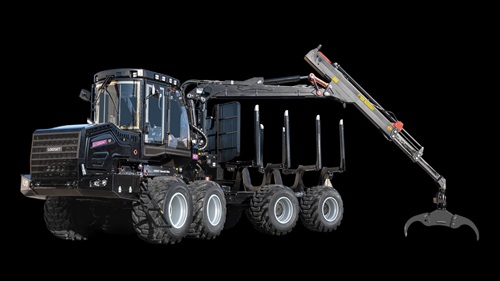
The project is co-funded by the EU and is run in collaboration with strategic partners.
Logset is expanding its portfolio of digital solutions to be able to offer both improved efficiency as well as a reduced footprint in forestry. The result is a unique map software which takes further advantage of the machine’s information flow and provides the operator with a quick overview of tree species, timber quantities as well as locations. Darkness, shift work and snow are no longer of concern, as the driver can easily see the areas that already have been forwarded and plan and optimize the routes. As a result, the forest environment can be cared for in a more responsible way.
Logset’s current digital portfolio which includes machine positioning, production follow-up and machine monitoring, gets a powerful complement through the new map software and streamlines and supports the everyday life for their customers. The product is in line with StanForD 2010 and the launch will happen during 2024. Source
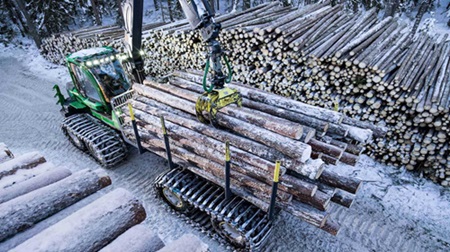
This will enable customers to remotely download secure software updates directly to their equipment
Through its Equipment Mobile app, it will enable customers to remotely download secure software updates directly to embedded controllers on compatible 4G-connected John Deere equipment. This update follows the March 2022 announcement that expanded the availability to purchase Customer Service ADVISOR directly from John Deere.
Using their John Deere Operations Center™ account, John Deere customers operating compatible 4G-connected machines can use this enhanced solution to complete secure software updates directly to an embedded controller through a user-friendly interface using the Equipment Mobile app. This is in addition to other valuable customer maintenance and repair information added to Operations Center™ and Property Center™ this year including Operator’s Manuals, Warranties, and Product Improvement Programs specific to their equipment.
With this announcement, John Deere is taking the next step toward digitizing and enhancing the self-repair experience for customers. This feature will give John Deere customers the ability to keep controllers on their compatible 4G-connected equipment up to date with the latest software releases. These updates can include enhancements and general improvements to generate a better equipment experience.
John Deere remains committed to continuing the development of solutions that support and enhance customers’ ability to safely and securely repair their own equipment, including reprogramming capabilities for compatible equipment and solutions for non-connected machines. To learn more about John Deere’s commitment to customer uptime and repairability, visit Deere.com/repair.
Available on both iOS and Android at no cost, the Equipment Mobile app helps John Deere customers to manage, maintain, and keep their equipment running. With this app, users can prepare equipment for work, access key information from the Operator’s Manual, and find the parts they need. The app also connects with John Deere Operations Center™, providing an easy, reliable connection between John Deere customers and their equipment.
John Deere Operations Center™ is an online farm and worksite management system, available to customers at no cost, that enables access to work progress anywhere, anytime through web, tablet, or phone. Operations Center™ enables customers to manage your operation more efficiently, reduce costs, and improve profitability.
John Deere Property Center™ helps residential customers manage their mower or compact utility tractor and connects them with their John Deere dealer. It provides customers with the online tools and information needed to conveniently manage your equipment, plan maintenance, buy parts, and do work around the yard.
Customer Service ADVISOR™ helps customers diagnose, troubleshoot, and perform most equipment repairs. The tool is available through John Deere dealerships and directly from John Deere on shop.deere.com. Equipment owners and independent repair shops have access to Customer Service ADVISOR™ in addition to replacement parts through John Deere dealers. Source
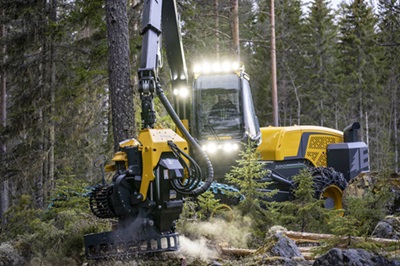
This allows for lower capital cost mulching for specialised operations.
The development behind the cabin is one of Eco Log´s longest projects so far and the road has been lined with quite a few challenges. Also, it has been a learning process to many parts of the company. The new harvesters in the G series are now waiting for production to start in 2024.
Behind the decision to develop a new harvester cabin are several factors. Future regulations, new design possibilities and, not the least, the demands and requests from the customers was finally decisive and a first pilot study was started in summer 2017.
To develop an entirely new cabin is, to say the least, an extensive task and the factors to consider are many. In a pilot study, all input from the market is gathered with a variety of different parameters, such as manufacturing costs, legal requirements, technical limitations, choice of suppliers and the conditions to manufacture and produce the product in an efficient way. Of course, the operator comes first regarding visibility, ergonomics, comfort and functionality.
When the development work really starts there are a variety of thorough tests and simulations that must be conducted to ensure that everything from climate, materials and electronics to visibility and, above all, safety is well functioning and meets various requirements and standards. A slightly different customer request was the turnable seat where the main reason was to create a space for having lunch without sitting with the food in your lap. This solution has then resulted in several advantages. As an example, there is plenty of space behind the seat to store your cooler bag or lunch bag and one can also spin the seat to get out of the cabin more easily. Another advantage is an easier service. Now, one can turn the seat around and easily access fuses, relays, diagnostic sockets and many other things that are placed under the panels behind the operator.
Storage possibilities is a recurring request from the customers and Eco Log´s development department has put a lot of effort to find smart storage solutions – a task that comes with a lot of challenges. The cabin must also accommodate large amounts of electronics, a ventilation system suited both for summer and winter, noise isolation and now, the rotating seat.
A special carriage was manufactured to be able to move the cabin between different tests. Eco Log performed many calculations on solidity and the possibilities to get out of the cabin in case of an accident. To verify all the calculations a number of cabins were tested. We simulate that a machine turns over (ROPS), they release a large steel ball onto the cabin to simulate a falling tree (FOPS); and ensure that the front windshield is resistant to chain shots. Also, OPS tests are carried out to make sure that the operator can´t be injured by example logs or other objects.
The cabin has a new HVAC system. The preparations of the climate tests are made in a simulation program, both regarding air flow and capacity for heating and cooling. The optimized result could then be 3D printed and tested in the first prototype cabin. There are also requirements deciding how a cabin should be cooled without causing air drafts around ones neck. This also applies to heating and the possibility to have windows free from condensation. The requirements today states that it can only differ a maximum of five degrees between head and foot for the operator. The cabin climate also includes floor heating, a newly developed system that has been thoroughly tested for an optimal temperature. Electric heating coils under the rubber mat makes snow and water dry quickly and gives a comfortable temperature to your feet or to your dog accompanying you in the machine. The challenge with floor heating is to create a system that provides a heated area that is as large as possible and in the same time safe to walk on and install without risk of causing damages to the system when handling the chair.
The choice of different materials has also been tested, amongst others to see how the sun´s rays affect. Tests were performed in an UV chamber for more than 1000 hours, which according to standard is equal to approximately ten years of exposure of the sun. The UV-affected material was also brushed with hydraulic oil to see if that could have an impact on the lifespan of the material. Through these tests, some materials could be excluded, and others selected for use in a forest machine.
Many tests have also been carried out on the key-less system, both regarding the placement of antennas in the cabin, but also regarding functionality and reliability. The sensor for locking and unlocking have been tested to ensure that it works even if you are wearing gloves, if it rains or is cold outside. The key has been tested regarding reach, but has also been put down in mud to ensure that you can drop it in your tracks and still get into the cabin. Source
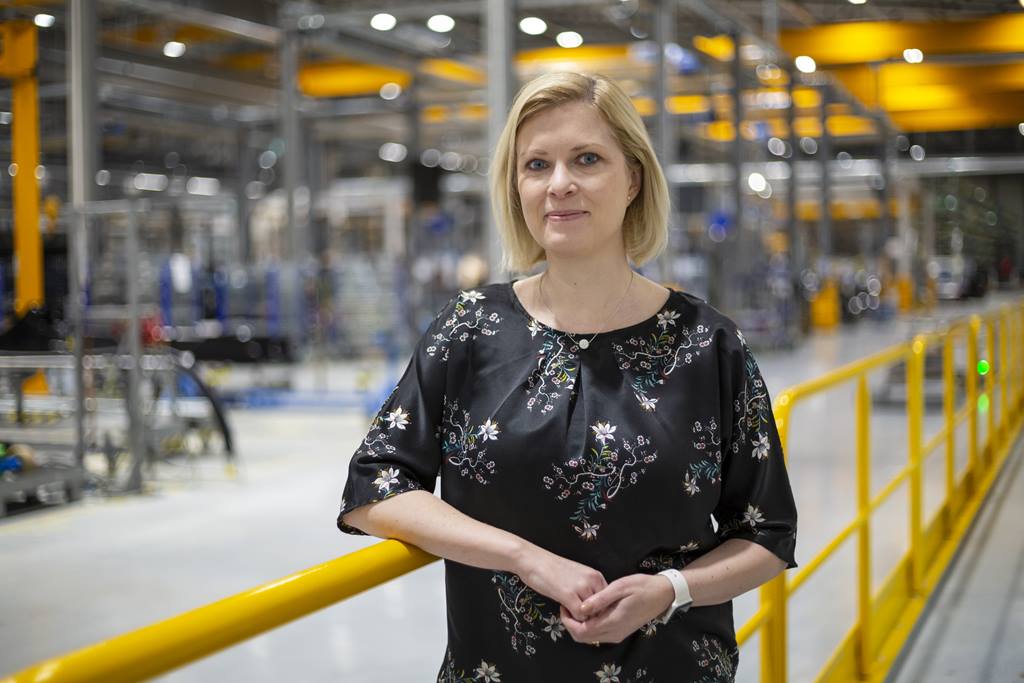
They have created a brand-new development department for electrification
Stina Drotz stepped into the role of General Manager of the department, whose main mission is to solve the challenges of electrification of Komatsu forest machines together with industry stakeholders. Stina is a civil engineer and has a background in both the automotive and forestry industries. Although she has experience from similar projects, it is new to now participate in building a completely new department.
The key to success, Stina believes, is about developing people, both at individual and team level. People with different backgrounds and experiences will need to collaborate and lift each other up. The team will work in a newly built, modern facility in a development environment that is at the forefront of digital solutions. People will also have a unique opportunity to participate from idea to finished product.
In particular, Stina sees three challenges with her new mission. In addition to the technical challenges that electrification entails, society’s infrastructure for electricity distribution also needs to be developed. In addition, it is important to find the right employees with the right skills. The large industrial investments made in Norrland create great competition for new employees – a challenge that the company partly takes on by establishing a local office in Stockholm.
The new department is emerging, and recruitment is underway. Above all, the company seeks electric vehicle developers and engineers who are specialists in software, hardware, mechanics, hydraulics and energy. Komatsu Forest is looking for skilled engineers who want to break new ground. Komatsu Forest aims to reduce CO2- emissions from their machines by 50% by 2030. Source
Ponsse manufactures its 20,000th forest machine
The 20,000th Ponsse forest machine has been completed at Ponsse’s factory in Vieremä, Finland. After the celebration on 11 December, the Ponsse Bear harvester with Ponsse H8 harvester head will go to a Norwegian customer, Lågen Skogsdrift AS. Source
Read MoreTo see the full list of international logging, roading and trucking conferences and expo’s, please click the “Events” tab at the top of the page.
Read More