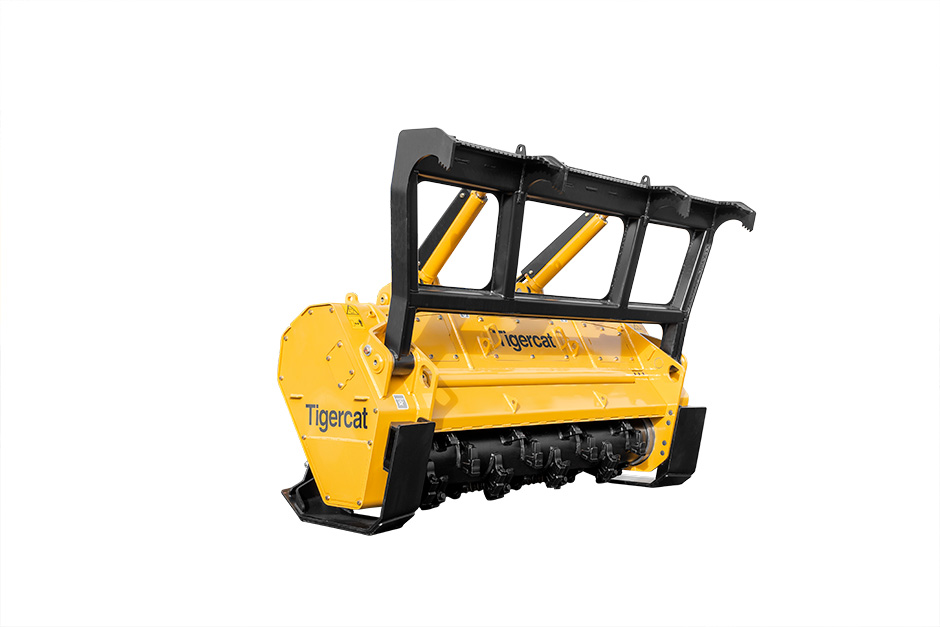
Tigercat releases a smaller class mulching head suited to applications like fire mitigation and remediation.
Designed for the Tigercat 470 mulcher, the 4054-20 provides a complete end-to-end Tigercat mulching solution for narrow swath applications and lower horsepower carriers. The 4054-20 head has a smaller diameter drum, a two metre (79 in) mulching swath and a lighter weight, more compact design. Key applications include fire mitigation and remediation, as well as right-of-way and site preparation projects requiring a smaller, more agile machine.
The smaller size and lighter weight of the 4054-20 means it can work on carriers with less attachment power, while retaining similar recovery performance to larger heads equipped on larger carriers. Various carbide tools and hardened steel knife tools are available to suit a range of applications. The Tigercat designed bolt-on tool system is available for both the open face rotor and the feed control rotor.
Manufactured to Tigercat’s high standards for robustness and quality, the 4054-20 mulching head offers excellent durability and reliability. Carbide welding on the skis provides extra protection from wear. The robust housing with reinforced side covers adds to the heavy duty build quality and structural integrity.
The drive system efficiently transfers power with no belt slip and reduced belt tension maintenance. Large, heavy duty bearings and shafts ensure long life and high uptime. Numerous removable access covers allow easy maintenance of wear items and service points. The wear liner can be serviced in the field and does not require welding or rotor removal. Source
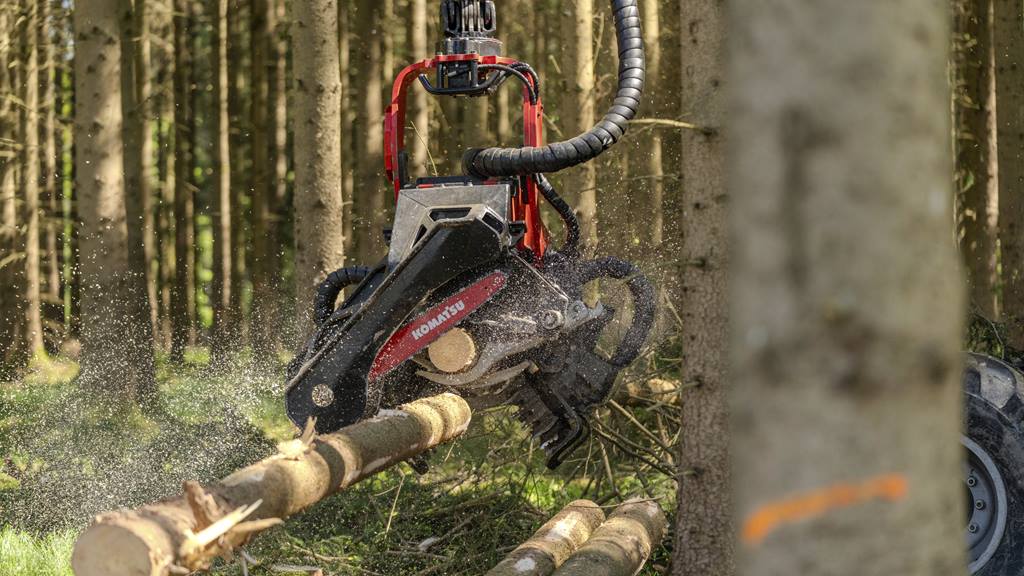
Key improvements include a redesigned valve block and enhanced hydraulics for the feeding system
The Komatsu C124 has received significant upgrades for the 2025 model year, aimed at boosting productivity and user experience. The most notable upgrade is the introduction of a new valve bank, which offers improved durability, reduced wear, and lower energy losses—resulting in fuel savings. Additionally, the pressure control for the front and rear knives has been refined for greater precision, with adjustments now fully managed via software. This allows operators to easily control settings like the knives’ opening pressure from inside the cab. The hydraulics for the tilt functions have also been improved, resulting in smoother operation and potentially higher measurement accuracy during processing.
To ensure high and consistent measurement quality, Advanced length measuring is now standard on the C124. This update includes a stronger cylinder and a modified mechanical stop to reduce wear.
The saw unit has been redesigned with additional clearance between the saw bar and frame to prevent collisions. A reinforced, curved base plate enhances durability while reducing the unit's ground footprint. The updated design also provides more space around the saw motor, making daily maintenance easier and more accessible.
The new feed system features high-flow motors that enhance performance and reduce energy losses. The upgraded system also includes improved hose routing for easier servicing and extended service life. An optional reinforced hose protection layer is now available to further increase hose longevity.
The 2025 model introduces the “Find End” option, which automatically resets length measurements without requiring a new cut, reducing waste. The option has been updated with a protected lens and debris-resistant design for longer service life. Other enhancements include improved centering for small stems, stronger bushings with better sealing for front delimbing knives, and new feed rollers with spikes for better grip and measuring accuracy in challenging conditions. Source
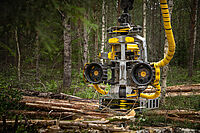
Kesla continues to develop its fleet of products.
The Kesla 19RH-III twinAX is an efficient solution for energy wood harvesting. Thanks to the modular structure of the RH-III harvester head series, the Kesla 19/21RH-III is easy to equip for various applications. The Kesla twinAX cutting system is a cutting knife unit intended to replace the saw module of Kesla 19/21RH-III heads. With a cutting capacity of up to 30 cm (11.8 in) (depending on the wood type), the Kesla twinAX is perfect for heavier energy wood harvesting sites. A regular saw module can easily be replaced with the twinAX module and vice versa, reducing the risks related to head investments, even in rapidly changing work situations. The Kesla twinAX cutting system ensures stump treatment in line with the Forest Act, including on energy wood sites. Equipped with the revamped Kesla MTH-grip multi-stem processing grapple, Kesla proTILT tilt control and multi-stem feed rollers, the harvester head is an incredibly efficient tool for multi-stem processing.
Kesla has made many upgrades to the Kesla RH-III harvester head range that improve the products’ operating characteristics and durability. The extensive updates to Kesla’s manufacturing technology have enabled, for example, the development of robotic welding and automation as well as the introduction of new structural solutions, which is reflected in the higher durability of the upgraded frame structures and the improved power-to-weight ratio of the heads.
An important addition to Kesla’s accessory range is the SuperCUT 150 saw module, which is now available for the sturdier Kesla RH-III models from the 26H-III onwards.
For a long time, Kesla has been heavily investing in the development of harvesters for excavators, and cooperating with multiple excavator manufacturers. Kesla’s product selection includes productised installation kits and accessories that make installing a head to most excavator models’ hydraulics easy, providing an efficient and effective solution that is also approved by base machine manufacturers. Source
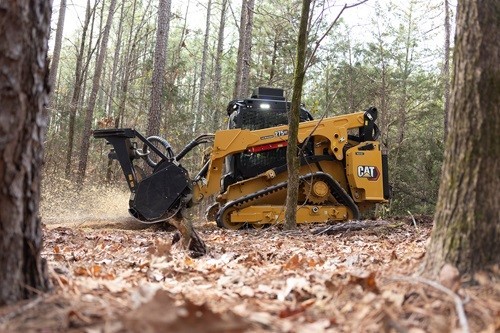
They have more power, performance and comfort.
Caterpillar introduces eight new next generation Cat® Skid Steer Loader (SSL) and Compact Track Loader (CTL) models. Four new Cat SSLs – the Cat 250, 260, 270, and 270 XE – mark the introduction of the next generation design to the SSL line. Meanwhile, the new Cat 275, 275 XE, 285 and 285 XE mark the expansion of the next generation design for the CTL line, joining the 255 and 265 announced in late 2023. The largest CTLs ever produced by Caterpillar, the new Cat 285 and 285 XE compete in a new class size with greater lift height and lift and tilt breakout forces. High performance is the standard for these next generation machines, elevating Caterpillar’s loader reputation through upgrades in engine power and torque, lift and tilt breakout forces, stability, operator comfort, and technology.
The new SSL and CTL models carry on Caterpillar’s new machine nomenclature with the elimination of the series letter designation. All next generation Cat SSLs are now identified by an ending model number of 0, while all CTLs have a model number ending in 5. Simplifying nomenclature, the middle number represents machine size with a larger number designating a larger machine.
All next generation Cat SSL and CTL models feature a redesigned engine compartment that places the engine and cooling package lower into the frame for improved stability, giving the operator confidence in handling heavy loads throughout all aspects of the work cycles. Meeting U.S. EPA Tier 4 Final/EU Stage V emissions standards, the four new CTL models are powered by the Cat C3.6TA engine, while the 250 and 260 SSLs are powered by the Cat C2.8T and the 270 and 270 XE by the Cat 3.6TA. These new engines maintain horsepower across a wider RPM range compared to the previous engines powering the D3 series and boast significant torque increases – 13% for the 250 and 260, 35% for the 270, and 50% for the 275 and 285 – for improved working performance.
With a vertical lift design, these new next generation machines feature significant increases in lift height, breakout forces and ROC to elevate loader flexibility and performance.
Their new closed-center auxiliary hydraulic system allows these machines to operate all Cat Smart Attachments with the standard hydraulics provided. Standard hydraulic system pressure increases 5% to 3,500 psi (24130 kPa) in the next generation models. Cat 250, 260, 270 and 275 machines equipped with standard hydraulic flow are shipped from the factory outfitted as “High Flow ready.” High Flow functionality is activated simply via a new software enabled attachment (SEA), permitting on-machine or remote activation of increased hydraulic flow to 30 gal/min (113 l/min) for the 250, 260, and 270 models and 34 gal/min (129 l/min) for the 275 at standard hydraulic system pressure.
The four next generation CTL models feature a new E-bar (equalizer bar) undercarriage that provides increased stability for grading and handling heavier loads. The E-bar undercarriage harnesses Caterpillar’s heritage and leadership with track type tractors to provide a hybrid undercarriage solution. It delivers the benefits of a rigid-style undercarriage design when lifting heavy loads or using heavy attachments like mulchers and dozer and grader blades, while simultaneously providing the benefits of an oscillating undercarriage when encountering uneven terrain or obstacles.
All next generation Cat SSLs and CTLs feature a larger cab design with 22% more overall volume and 26% additional foot space. With a 2.75-in (70-mm) increase in interior width, the new cab expands footwell-to-ceiling height by 1.8 in (46 mm) and allows for an additional 1.5 in (40 mm) of hip room and 1.1 in (28 mm) more width between the joysticks to improve operator comfort.
Next generation loaders are equipped with either a 5-in (127-mm) standard LCD monitor or an 8-in (203-mm) advanced touchscreen monitor, depending on the selected technology package. Like the advanced display on the D3 series, the standard monitor features Bluetooth connectivity and supports functionality for rearview camera feed, creep, job clock, maintenance reminders and 32 languages. The advanced touchscreen monitor provides a higher level of control over standard monitor functionality, offers advanced radio control, and supports side cameras and 32 language choices. The new advanced joysticks enable integrated control of the advanced touchscreen monitor, so all machine function control and adjustments can be made without the operator removing their hands from the controls.
A range of new mechanical and air-ride suspension seat options are available for these next generation machines, including a high-comfort seat that is both ventilated and heated. New auto temperature control plus vent outlet positioning above the operator help the new HVAC system to quickly cool the cab’s interior.
Entering and exiting next generation loaders is much easier thanks to their low entry points. The operator can now open the cab door without the lift arms being fully lowered to the frame stops. A simplified two-step door removal process allows operators to quickly remove it without tools. The machines’ lower engine mounting, 59% larger rear window and bigger top window providing 15% increased viewable area combine to improve operator visibility.
These new SSLs and CTLs offer the next level of integrating machine and technology. Both standard and advanced monitors provide the ability to run Cat Smart Attachments, such as the dozer and grader blades and backhoe. Attachment operation is integrated into the joysticks, and the machine automatically recognizes the type of attachment and the required joystick pattern for controlling it. Source
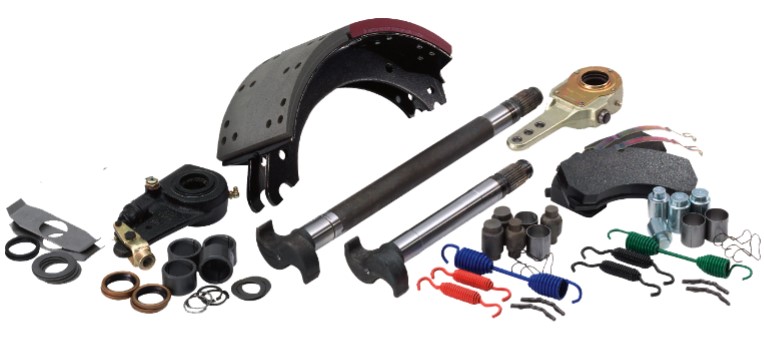
Cummins explains why it's important to inspect the entire foundation braking system during service.
Brake system issues are a leading cause of out-of-service violations. When performing brake maintenance, it is important to inspect and maintain the entire braking system to prevent these violations. The goal is not to have more brake jobs, but rather for brake jobs to be more complete, resulting in more uptime. Automatic slack adjusters, brake shoe lining, brake drum, camshaft and the brake chamber bracket are the top five braking components responsible for the most out-of-service citations.
Proper brake maintenance can prevent costly roadside repairs, reduce downtime, and decrease the number of fines and enforcement penalties. Here’s a complete look at what goes into proper brake maintenance.
To maintain proper brake adjustment and provide balanced braking, automatic slack adjusters (ASA) must be inspected to confirm an identical ASA is used on both sides of an axle and the adjuster mechanism is functioning properly. Measure and confirm “free-stroke” is correct. If found to be incorrect, determine the root cause and correct it; do not just adjust the brake.
Check lining thickness and look for cracked linings as well as ones covered with oil, grease or fluid from a failed camshaft seal/bushing or wheel seal. Rust jacking occurs when harsh chemicals, such as ones used for deicing, get between the table of the shoe and the lining. The shoe coating fails, then rust forms and the lining cracks and is lifted off the table resulting in premature failure of the lined shoe.
Start the brake drum inspection by measuring drum wear. The diameter of the drum should not be beyond the manufacturer’s limits. As the brake surface wears the drum mass is reduced, resulting in the brake’s inability to dissipate heat. The retained heat reduces friction material life and braking performance.
Also, check to see that no part of the drum is missing. Look for scored or heat-checked drums. Upon visual inspection, a heat-checked (cracked) brake drum will appear closed at room temperature. Heat checks open and close with each brake application. Be aware that heat checks may not necessarily be at the edge of the drum. In addition, if you find hot spotting or scoring, replace the brake drum.
When inspecting the camshaft look for missing or broken components such as cam rollers, springs, anchor pins and mounting bolts. Check cam bushings, cam tubes, and retaining rings. Be on the lookout for excessive wear of the camshaft head and rollers, as these can cause brake stroke fluctuations and result in exceeding the maximum range of the camshaft. Also check to see that the camshaft and camshaft tubes are properly lubricated.
Check camshaft radial movement by moving the camshaft head in all directions, and use a dial indicator to measure movement. Next, move the camshaft axially.
The service chambers and spring brakes on each end of an axle must be the same size. Inspect to make sure push rod stroke is not greater than the industry limits. There should be no damage to the service chamber, spring brake or push rods/clevis. Service chamber or spring brakes should be fastened securely.
There are long stroke and standard stroke chambers, and it is important to know which you are working with. The Society of Automotive Engineers recommends using two of three options for identification. Long stroke chambers have a trapezoidal shaped tag, square port boss and permanent identification on the brake chamber.
To test the return spring, force the pushrod back when the brake is released. Release the air from the service chamber. Release the spring brake and pull the pushrod out. When you let go, the pushrod should return to a full released position on its own. Symptoms of a bad return spring include an under-adjusted ASA, uneven release, rod not returning to full release position, and dragging brakes. Source
Tigercat provides additional product support in Australia
Tigercat announces an additional Australian factory representative team member, Jake Peters, based in Garfield, Victoria. Jake, along with Glen Marley based in Gundagai, NSW, Steve Green based in Launceston, Tasmania, and Damien Ambrose based in Tumut, NSW, will form the Australian product support quartet. A team who has been supporting Onetrak and our customer base in Australia for the past 24 years. Source
JCB’s engine business marks its 20th birthday
Since 2004, JCB Power Systems in Foston, Derbyshire, has gone from producing three engines a day to making almost 300. It has become a world leader in the design, development and manufacture of diesel engines and is now leading the way with the pioneering development of hydrogen engines. The business initially employed 20 people but has expanded its workforce to more than 400. To mark today’s anniversary, employees were presented with gifts and letters thanking them for their service. In addition, 10 employees with a combined 200 years’ service, planted an oak tree in the grounds of the plant to mark the occasion. Source
Read MoreTo see the full list of international logging, roading and trucking conferences and expo’s, please click the “Events” tab at the top of the page.
Read More