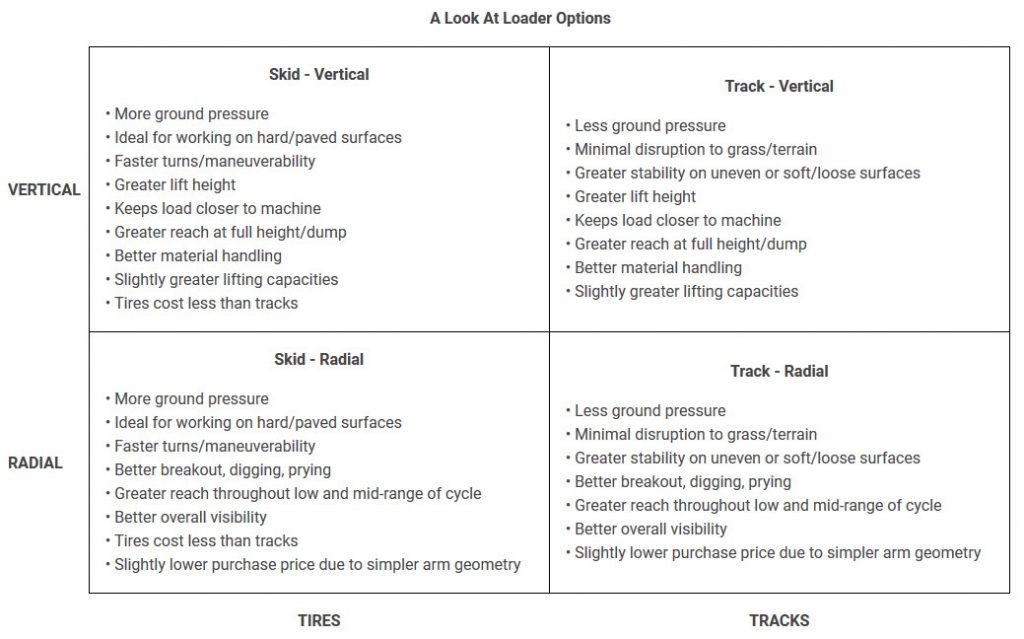
A compact track loader is one of the most versatile machines a contractor can own.
Whether as support equipment in a larger fleet or the main workhorse for an owner/operator, a skid steer and compact track loader are two of the most versatile machines a contractor can own. But what is the right loader arm and platform for each application? Contractors can follow this quick guide to set them on the right path.
- Loader arm – radial or vertical: Radial lift machines are best served for ground-engaging applications as they feature better breakout, digging and prying forces. As the travel path is most similar to an arc, this configuration provides greater reach at mid-ranges, which makes it ideal for loading and unloading off of smaller vehicles or platforms, such as pickup trucks. Visibility also tends to be a bit better with radial configurations. Vertical lift machines generally offer greater lifting heights, greater reach at full height and slightly higher lifting capacities. The arm design keeps the load closer to the cab for added stability and capacity. The arm design also allows for more stable material handling.
- Platform – tyres versus tracks: Tracked machines provide an incredibly stable platform that improves everything from grading to attachment use. The primary advantage is lower ground pressure and stable operation over uneven surfaces, as the tracks provide more contact with the ground than four independent tires. Tyred machines – the traditional skid steer loader – give the operator greater traction and maneuverability on paved surfaces. Tyred machines are quicker and have faster top travel speeds. Tyres are also more ideal in applications where tight turning is going to be taking place. While tyres will generally wear at a faster rate than tracks, tracks are more expensive to replace. Skid steers are typically less expensive than comparable compact track loaders.
- Lifting: Lifting is often the most taxing work that a skid steer or compact track loader will perform and its greatest measure of capacity. Case recommend selecting a machine with a rated operating capacity (50 percent of tipping load) that accounts for that heaviest common lifting task – and then some.
- The interaction between horsepower and rated operating capacity: Greater horsepower will typically allow for faster cycle times and make it possible for the machine to get to required pressures and flows faster – and maintain them more easily.
- Greater torque gives the operator more ability to power through resistance. It also aids in multifunctional performance and keeps the ground drive moving forward when it encounters resistance – all leading to greater, more powerful performance.
- A skid steer’s auxiliary hydraulic system provides the hydraulic flow that drives the machine’s attachments. The thing to remember is that not all attachments have the same hydraulic flow requirement. The most common system is the standard-flow auxiliary hydraulics package. Standard-flow auxiliary hydraulics are included on all skid steers from the factory and operate on the same pressure that the machine’s main hydraulics operate on. A standard-flow system powers many of the most common hydraulic attachments on the market, such as 4-in-1 buckets, hydraulic hammers, augers, trenchers and grapples. A high-flow auxiliary hydraulics system is a second option that further increases a skid steer’s versatility and productivity. A high-flow system can be factory-installed as an option or installed later in the field. It powers production-type attachments that require a high flow rate to perform as specified. Examples include cold planers, many snow blowers, rock saws, small mulchers, and chipper/shredders. When even more hydraulic power is required, an enhanced high-flow auxiliary hydraulics package is available. Examples of attachments that require an enhanced high-flow system include larger cold planers, larger mulchers used to clear brush and small trees, and a large rock saw you might find in an aggregates operation. Source
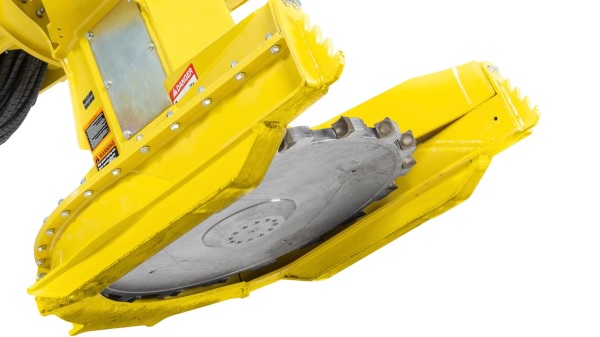
John Deere introduces the one-piece hardened beaver saw tooth to its line-up of aftermarket options.
Expanding the portfolio of aftermarket forestry saw teeth options for its customers, John Deere introduces the one-piece hardened beaver saw tooth for John Deere Wheeled and Tracked Feller Bunchers. The new beaver saw tooth design boasts a beveled feature at each tooth tip, which helps improve tooth durability while striking materials other than wood. Not only does this extend the life of the tooth but, also helps increase productivity in rocky conditions where a carbide tooth would not be advisable.
As the latest addition to the John Deere saw tooth lineup, the beaver saw tooth is one of four options available to customers and can be purchased in boxes of 18 or 20 teeth. Designed for maximum durability while lowering operating costs, the full line of John Deere saw teeth for Wheeled and Tracked Feller Bunchers are made to help support daily logging operations and applications. Source
https://www.cat.com/en_US.htmlThe new loaders have improved lift and tilt breakout forces, significantly increasing torque
Building on D3 series compact track loader success, the all-new, next generation Cat® 255 and 265 Compact Track Loaders are a ground-up redesign of the previous series, improving on the features that made the previous models so popular. All Cat next generation compact track loaders are identified by the ending model number 5. The simplified nomenclature uses the middle number to represent machine size with larger numbers designating larger machines.
The new 255 and 265 loaders are powered by Cat C2.8T and Cat C2.8TA engines respectively, which offer 74.3 hp (55.4 kW). The new engines maintain horsepower across a wider RPM range and boast significant torque increases – gains of 13% for the 255 and 43% for the 265 – for improved working performance. A redesigned engine compartment mounts the engine and cooling package lower into the frame for improved stability, giving the operator confidence in handling heavy loads and throughout all aspects of the work cycles.
The new 255 loader delivers good lift height, and compared to the 259D3, delivers 36% more tilt breakout, 26% higher lift breakout force and a 24% increase in rated operating capacity (ROC). Height to the B-pin for the 265, compared to the 289D3, increases by 7.6 in (193 mm), resulting in a maximum lift height of 11 ft (3.35 m) for easier truck loading. The 265 also delivers 19% higher tilt breakout force and 22% higher lift breakout force.
Standard hydraulic system pressure is increased to 3,500 psi (24130 kPa). New for these next generation machines, the closed-center auxiliary hydraulic system allows the 255 and 265 to operate all Cat Smart Attachments, including the Cat Smart Dozer Blade, with the standard auxiliary hydraulics provided.
Reengineering of lower machine components results in a stronger and stiffer undercarriage for improved machine stability and less pitching when filling the bucket with material. Its torsion suspension undercarriage delivers better operator comfort, track wear and material retention, plus the stiffer design results in smoother graded surfaces. The 255 loader offers a new 12.6-in (320-mm) bar-tread narrow track option.
Both the Cat 255 and 265 Compact Track Loaders feature a larger cab design with 22% more overall volume and 26% additional foot space. With a 2.75-in (70-mm) increased interior width, the new cab expands footwell-to-ceiling height by 1.8 in (46 mm) and allows for an additional 1.5 in (40 mm) of hip room and 1.1 in (28 mm) more width between the joysticks for improved operator comfort. A range of new mechanical and air-ride suspension seat options are available for the 255 and 265 loaders, including a high-comfort seat that is both ventilated and heated. New auto temperature control plus vent outlet positioning above the operator helps the new HVAC system to quickly cool the cab’s interior.
Next generation loaders are equipped with either a 5-in (127-mm) standard LCD monitor or an 8-in (203-mm) advanced touchscreen monitor, depending on the technology package selected. Like the D3 series’ advanced display, the standard monitor features Bluetooth connectivity and supports functionality for rearview camera feed, creep, job clock, maintenance reminders and 32 languages. The advanced touchscreen monitor provides a higher level of control over standard monitor functionality, delivers advanced radio control, and supports the multicamera 270˚ option and 32 language choices. The new advanced joysticks provide integrated control of the advanced touchscreen monitor so all machine function control and adjustments can be made without the operator removing their hands from the controls. Source
Read More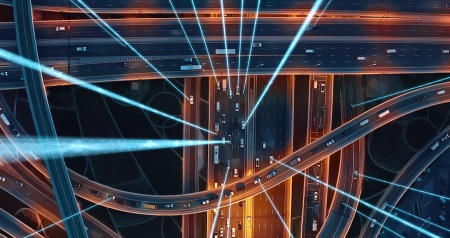
Connectivity and telematic technologies used in the trucking industry have advanced significantly in recent years.
Vehicles and components are smarter than ever thanks to smaller, more advanced electronics and widespread communications infrastructure. Digital applications such as remote monitoring, diagnostics and prognostics are changing vehicle management. Today, customers have a wealth of real-time data from their engines to leverage, ultimately increasing vehicle uptime, reducing costs and enhancing efficiency.
Telematics is the combination of telecommunications – technology like phones and cables – and informatics – computer systems. Telematics systems can provide customers with comprehensive, real-time insights into various aspects of their vehicles, such as engine health, fuel consumption and maintenance needs.
Connectivity technologies can accumulate insights and send information regarding a vehicle remotely, including the engine’s health, driving patterns and fuel usage. Telematics and connectivity are critical technologies for modern customers to consider integrating into their vehicles. Here, Cummins provides some of the key benefits of telematics and connectivity.
- When an equipment failure occurs, remote diagnostics can help technicians identify the problem and ensure the right parts are available for repair.
- Predictive service insights or prognostics systems can significantly increase uptime. By identifying problems before they cause a failure, preventive maintenance can extend equipment life and reduce downtime. This technology monitors a customer’s entire fleet, notifying them of only the engines that require attention.
- Connectivity allows customers to remotely push over-the-air updates to any trucks under their control. This means that trucks require no additional downtime to apply updates and always have the latest software to deliver the highest performance and reliability.
- Timely maintenance and repairs can prevent more extensive and costly breakdowns, ensuring that trucks remain in optimal condition with minimal downtime.
- Advanced telematics-based insights also allow customers to study their driver’s behaviour and determine areas of efficiency. With cloud-based management, drivers are routed to the nearest service station, eliminating unnecessary mileage when looking for a shop.
- Telematics data can monitor driver behaviour to help identify and address unsafe driving practices such as harsh braking. With data on driver behaviour, businesses can offer further training to help keep incidents to a minimum.
- Data collected through remote monitoring can improve optimization for current vehicle models and future engines. Performance and maintenance data on current generations of engines will enable more robust and efficient engines in the future. Source
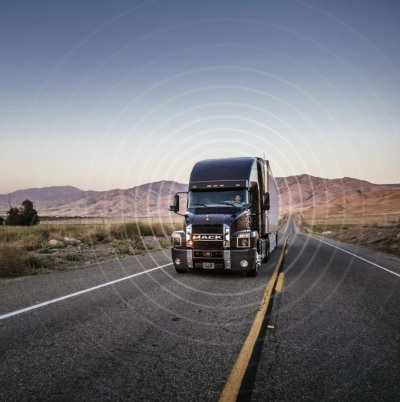
This enables customers to digitally access information about the Mack-powered trucks in their fleet.
Mack Connect improves customer visibility into the health and performance of their vehicles and simplifies the process to access the data. Mack Connect gathers critical aspects about a customer’s trucks, services and their specific application, translating this into improved fuel efficiency, safety and productivity. The Mack Connect toolbox includes data about asset location, idle time, traffic information, fuel efficiency, safety performance and vehicle speed. Customers can access the status of their Mack vehicles through a 4G Telematics Gateway, factory-installed at Lehigh Valley Operations, Macungie, Pennsylvania, where all Class 8 Mack vehicles for North America and export are assembled.
Mack Connect is a portal that offers customers access to critical data that goes beyond what they are used to seeing. Mack Connect offers visibility to the Mack GuardDog® Connect integrated telematics solution so customers can easily manage fault events should they occur, while also providing visibility to over-the-air updates when available. Reporting and analytics are available so customers may analyse the data to determine whether adjustments need to be made to improve efficiencies. Source
Bandit celebrates 40th anniversary at corporate headquarters
Bandit Industries celebrated its 40th anniversary with a corporate event on September 27th and 28th. Visitors from the USA and 15 different countries attended, including from Australia, Argentina, Brazil Canada, Chile, Czech Republic, Denmark, France, Guatemala, Indonesia, New Zealand, Poland, Puerto Rico, South Africa, and the United Kingdom. Source
Logset Oy and HIDROCOM SRL collaborate in distributing Logset products in Italy
The agreement was formally signed at the Austrofoma exhibition in Stühleck, Austria. Logset Oy identifies the Italian market as a potential hub for the growing use of CTL machines. The broad product range offered by Logset aligns well with the requirements of the Italian market. Source
Changes to Tigercat Social Media
Due to an ongoing legal dispute related to the use of the Tigercat brand name in the countries of Belgium, Netherlands, and Luxembourg (collectively known as the Benelux region), Tigercat Industries Inc. is compelled to take certain actions related to its online social media presence. While current Tigercat followers will be unaffected, anyone who is not, and wishes to view the page feed must submit a request to follow. Individuals residing in Benelux should not submit a request to follow as these individuals are not permitted to view Tigercat branded content. Source
Read MoreTo see the full list of international logging, roading and trucking conferences and expo’s, please click the “Events” tab at the top of the page.
Read More