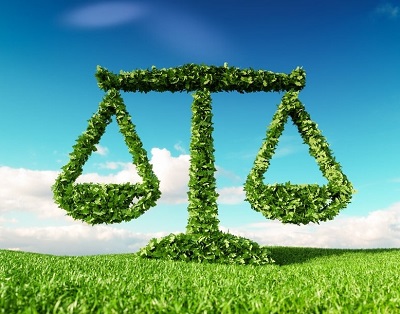
Many commercial fleet operators are thinking about transitioning their vehicles to hydrogen or natural gas engines.
These fuels can be great ways to reduce emissions. Both fuel options present similarities and differences across a variety of areas. For example, both hydrogen and natural gas are predominantly used in their gaseous form in vehicle applications. This leads to similarities in some components. On the other hand, there is a huge gap in their availability, resulting in different degrees of adoption.
Both natural gas and hydrogen engines are spark-ignited. Many of their components are thus similar, including the engine block, cylinder heads and ignition system. As is the case with all vehicles, safety is a paramount consideration. Both hydrogen and natural gas vehicles incorporate high-pressure fuel tanks to meet common safety requirements. However, Compressed Natural Gas (CNG) vehicles typically keep natural gas at pressures of around 3,600 psi. Hydrogen vehicles store their fuel at pressures of up to 10,000 psi—that’s higher than the pressure at the bottom of the ocean. Such high pressures are needed because hydrogen molecules contain less energy than natural gas molecules. So, to carry the same amount of energy onboard a vehicle, more hydrogen molecules must be pushed into the same tank, resulting in a higher pressure. This means that designing and manufacturing safe and lightweight storage tanks for hydrogen vehicles is more difficult.
Natural gas and green hydrogen are alternative fuels that help reduce emissions in the transportation sector. Replacing a hundred older diesel transit buses with natural gas buses with Cummins’ L9N natural gas engine, would have the same impact as taking 280 gasoline cars off the road. This is substantial, but natural gas vehicles still release CO2 when burning CNG. Hydrogen vehicles, in contrast, have near-zero tank-to-wheel greenhouse gas emissions, as long as they run on green hydrogen. They can reduce emissions by +99% compared to diesel. You can learn more about how green hydrogen emission reductions compare to different alternative fuels.
Switching to either type of vehicle can also result in lower emissions of air pollutants. Neither generates any soot and no-or very low-amounts of carbon monoxide and organic pollutants. Natural gas engines generate extremely low amounts of NOx. To account for the small traces of NOx tailpipe emissions from hydrogen engines, an aftertreatment system may be needed. Hydrogen Fuel Cell Vehicles, on the other hand, produce no NOx or other air pollutants whatsoever. Hydrogen internal combustion engines and fuel cells have complementary use-cases. Both invest in the hydrogen economy and infrastructure.
In 2021, there were approximately 1,500 private and public fueling stations offering Compressed Natural Gas, or CNG, in the United States. When comparing CNG to other fuels, it is not as universally available as gasoline and diesel. The CNG distribution network is still far denser than the green hydrogen distribution network though. There are only 67 public hydrogen fueling stations in the United States, and almost all of them are in California. The absence of a dense fueling network means that hydrogen is not yet an option for many use cases. In most places outside of California, Japan and some parts of Europe, drivers cannot consider purchasing a hydrogen vehicle as they would struggle finding places to refuel it.
For commercial vehicles, the absence of existing fueling options can be easier to overcome. Businesses interested in switching to hydrogen may have the option to build private hydrogen fueling stations in a central vehicle depot. These stations can be built similarly to CNG, a current practice, or they can place fueling stations along fixed routes between, for example, distribution centers.
If commercial users adopt hydrogen vehicles, it’s possible that hydrogen fueling stations will become more common. If this is case, then hydrogen vehicles could become a practical option for more users, including potentially private vehicles. This would drive the construction of additional hydrogen fueling stations and attract more users towards hydrogen vehicles. Cummins continues to invest in hydrogen production and electrolyzer technologies.
Although battery electric vehicles tend to be more popular than hydrogen vehicles in the personal transportation segment, there has been an undeniable progress in green hydrogen technology, production capacity and distribution infrastructure. If green hydrogen continues on that course, availability constraints will be less and less of a factor for fleet operators who are looking to switch their vehicles to an alternative fuel. Source
Long-time Logset man, Pascal Rety, returns to Logset as sales director
A total of 13 years of history in Logset sales will continue when Pascal starts developing Logset sales. He spent time with Sampo-Rosenlew’s agricultural sales. Pascal is educated in forestry and business as a Forest product marketing engineer. He was also involved with the establishment of a Logset’ subsidiary in Canada for 2 years. Source
The MAN eTruck picks up speed
Presented for the first time to a large audience at the IAA Transportation 2022, the future large-series eTruck from MAN is taking significant steps towards the future: it is prepared for the coming megawatt charging standard and is therefore suitable for heavy long-distance transport, but also covers all regional and distribution transport services provided by diesel trucks today. MAN has now made the first public test drives of the new eTruck possible as part of the MAN eMobility Experience. Source
Read More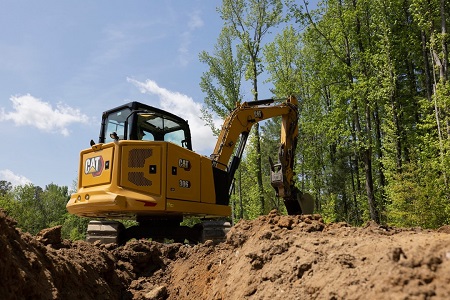
These simplify operation, improve accuracy, reduce costs and help operators work more safely.
New to Cat mini excavators, Ease of Use Indicate helps operators to reach grade faster, while Ease of Use E-Fence constrains machine motion to within operator preset boundaries. These technologies are ideal for digging footings, drainage and septic systems, irrigation, electric utilities, and applications near structures or obstacles operators need to avoid. They allow operators of all experience levels to work more efficiently and consistently.
An entry-level grade system, MHE Ease of Use Indicate provides visual and audible indications to bucket position compared to target grade to assist operators in cutting to exact specifications the first time. Regardless of skill level, operators reach target grade faster with improved precision and reduced need for on-the-ground grade checking to create a safer work environment.
With Indicate, the operator selects target depth and slope from the in-cab guidance system, and the monitor provides real-time work-in-progress and distance-to-grade feedback. The technology enables operators to reach grade faster without overcutting, saving time, manpower and saving cost overall.
MHE Ease of Use E-Fence automatically constrains machine motion to within operator preset boundaries for ceiling, floor, wall and swing. Operators work confidently and efficiently by avoiding structures overhead, underground, in front, or to the left or right of the machine.
Both MHE Ease of Use E-Fence and Indicate are packaged with Swing Assist and Bucket Assist features at no added cost. Swing Assist, also referred to as return to trench, automatically stops machine swing at one or two set points, ideal for truck loading and trenching applications. It helps operators hit more repetitive swing targets with less effort, reducing fuel use and improving cycle times. Bucket Assist maintains last known bucket angle and keeps the cut accurate in sloping, leveling, fine grading and trenching applications.
Current production Cat 306 CR, 308 CR and 309 CR Next Gen Mini Hydraulic Excavators are shipped from the factory Ease-of-Use-ready to reduce installation time in the field. Ease of Use Indicate and E-Fence can be ordered bundled together or as separate feature packages, installed at the factory or through Cat dealers as an upgrade kit. These technologies are not currently available for Cat 308 CR Variable Angle Boom, 309 CR Variable Angle Boom, 308 CR Fixed Boom, or canopy models. Source
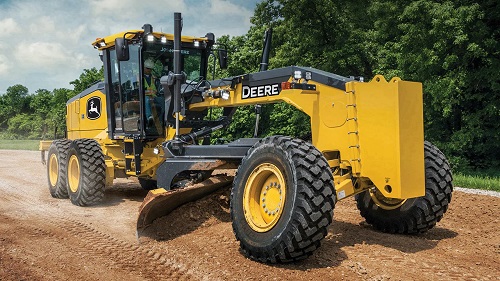
John Deere introduces its full suite of technological advancements on its GP-Series motor grader lineup.
Now available in the European market are industry-leading automation features including industry-exclusive Machine Presets, Auto-Gain, and Auto-Shift PLUS. European customers can also benefit from John Deere Premium Circle technology and Grade Management solutions, available for purchase through the Wirtgen dealer network.
John Deere has introduced features that help ease the learning curve and reduce rework, and operators can get to the next job faster, increasing their bottom line. Now available in certain European markets is Premium Circle. The fully sealed bearing and pinion help reduce maintenance costs and downtime by eliminating wear inserts and ensuring the circle remains tight during operation, maximizing accuracy while also significantly boosting circle torque and speed. The addition of the Premium Circle will boost machine productivity and uptime, positively impacting contractors’ bottom lines.
Customers can also benefit from two additional industry-exclusive offerings: Machine Presets and Auto-Gain for John Deere’s cross slope system. Machine Presets enable multiple functions to be programmed into one button. Functions such as automatically stowing the blade or ripper, turning on lights or beacons, engaging Auto Shift, and many more can be completed simultaneously with the touch of a button. Auto-Gain automatically adjusts the blades responsiveness on the fly when using Cross Slope based on the operating conditions, eliminating the need for operators to make manual adjustments. In addition, Auto-Gain technology helps improve productivity for operators by ensuring accurate blade movement in ever-changing conditions.
Entering the market as the latest industry-exclusive technology is Auto-Shift PLUS, which allows for the machine to come to a complete stop without stalling, helping reduce fatigue while cutting smoothly around obstacles or structures. Operators can control ground speed, come to a complete stop, and start moving the machine by only using the throttle and brake. Whether transporting the machine or completing any grading task, Auto-Shift PLUS simplifies operation. Source
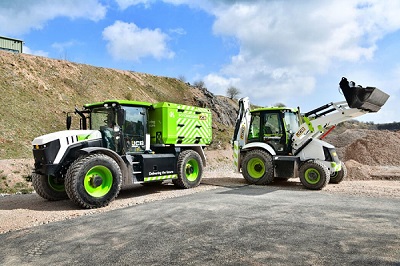
JCB also developed the world’s first working construction machines powered by hydrogen.
JCB is investing £100 million in a project to produce super-efficient hydrogen engines and has already showcased working prototypes of a backhoe loader and Loadall telescopic handler powered by hydrogen. Now JCB has announced another industry first – a mobile hydrogen refueller, providing a quick and easy way for customers to refuel their machines on site. Around 97 per cent of construction machines have fuel delivered to them while working on site. This means customers are already used to a transportable fuel, allowing refuelling to take place in a matter of minutes.
The new mobile hydrogen refuelling system allows hydrogen to be taken from on-site tube trailers and distributed to machines by a refueller as they work on the job site. This is no different to today when diesel is taken in bowsers to refuel machines.
Fossil fuels are not the future and hydrogen is the practical solution to powering JCB machines in the decades to come. A team of 100 engineers is working on the project. The first hydrogen powered machine to be unveiled was a JCB backhoe loader followed, a year ago, by a Loadall telescopic handler. The technology went on to be shown in the Green Zone at COP26 in Glasgow as world leaders debated measures to drastically reduce greenhouse emissions. Source
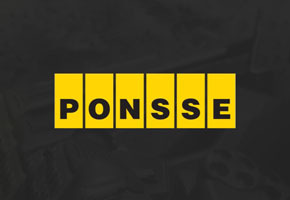
Ponsse also update us on how the war in Ukraine affects machine manufactures.
Demand for Ponsse forest machines and services remained healthy. Global market conditions were generally good, supported by a good market situation in the pulp industry and the absence of Russian timber and sawn timber in the European market. The corporate acquisition of their Russian subsidiary OOO Ponsse is awaiting approval by Russian authorities, and they are aiming to conclude the sale as soon as possible.
The discontinuation of business in Russia, heavy inflation, and the notable decline in the availability of parts and components continue to have a material effect on Ponsse. The problems with the availability of parts and components continued during the period under review, impacting both the company’s profitability and cash flow. The company’s production and aftersales services continue to suffer due to limited availability. Regardless, their production has continued without interruption.
During the period under review, Ponsse launched major product and service solutions, which were presented at forest machinery fairs around the world. In addition to conventional harvesting technology, they launched completely new technology with their subsidiary Epec: the electrically driven Ponsse EV1 forest machine concept. The interest of developing forestry towards Ponsse’s and Epec’s new products has been highly encouraging. They continue to target pioneering product technology with their investments.
Net sales were regionally distributed as follows: Northern Europe 37.7 (40.3) per cent, Central and Southern Europe 22.0 (23.1) per cent, North and South America 36.1 (31.8) per cent and other countries 4.2 (4.8) per cent
Ponsse’s operating environment has changed drastically and it is affecting Ponsse’s operations. Russia’s invasion of Ukraine has forced the European Union and United States to respond and impose rigid sanctions against Russia. In compliance with export sanctions and the company’s policy, Ponsse suspended all sales and export operations to Russia and Belarus effective 2 March 2022. At the same time, the operations of the local Russian subsidiary OOO Ponsse were discontinued.
The war in Ukraine is hampering to a great extent the operation of the manufacturing networks. Russia, Belarus and Ukraine have played a significant role in the supply chains of the European steel industry, while Russia has played a critical role as an energy supplier to Europe. As a result of the war, the availability of raw materials used in steel production has declined significantly and rising energy prices have pushed up the costs of steel processing to the extreme. In addition, Ukraine has supplied, inter alia, gases used in the semiconductor manufacturing process, which has already been reflected in the shortage of semiconductors. The delivery capacity of the manufacturing networks has decreased and inflation has significantly risen as a result of the crisis.
In the challenging situation, Ponsse’s strong financial position is important. The company’s financial position has remained strong due to good liquidity and binding credit limit facilities agreed with financial institutions. In terms of financing, Ponsse has carried out all measures necessary to ensure business continuity and financial situation is regularly evaluated. Source