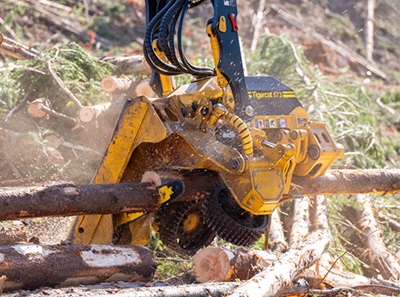
Tigercat adds a fifth model to their harvesting head line-up with the new three-wheel drive 573.
In late September 2023, visitors to the PLC live demo event held in Washington state got a sneak peak of the new Tigercat 573 harvesting head processing logs on the end of a Tigercat 875E logger. Since then, multiple units have been in testing in far flung regions from Alberta to Australia and the results are in. The 573 is shaping up to be a high performing, reliable head for roadside processing and harvesting.
Best suited to medium and large tree profiles, the 573 has a 800 mm (31 in) maximum cut capacity and offers optimal performance in 400-600 mm (16-24 in) diameter timber. The feed rollers close down to 60 mm (2.4 in), allowing the 573 to smoothly delimb and process smaller diameter trees and thus achieve higher value fibre recovery.
The compact frame design deftly handles poor stem form and contributes to tidy delimbing performance. The triangulated feed wheel arm configuration operates in locked three-wheel drive. This, combined with timed knife arms, provide the operator with fast picking and positive stem control for high productivity in roadside processing applications. Independently mounted, trailing-arm length measuring ensures reliable tracking and accuracy.
The top knife and lower/back knife pivot on the same side of the chassis frame, aligning the position and flow of each stem centrally through the head. This arrangement promotes positive contact with all three feed rollers and the measuring wheel at all times. The result is better quality and accuracy, reduced fuel consumption, and greater processing speed. The orientation also provides the operator with a clear sightline to the measuring wheel.
The 573 is standard equipped with continuous rotation for ease of use and superior hose routing and protection. Quick, stable WiFi connectivity between the cab and attachment modules reduces wire routing along the boom and provides excellent command response.
The Tigercat D7 control system is available with Priority or Optimization levels and is fully compatible and compliant with StanForD Classic and 2010.
The 573 is a great fit for the H250D, 850 and 875E for roadside processing applications and the H822E and H855E carriers for in-stand harvesting. Source
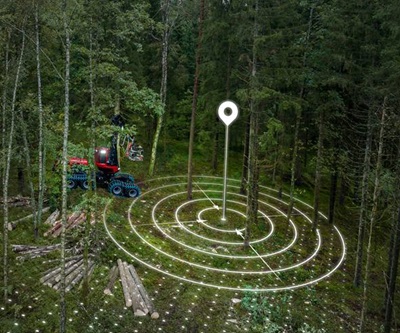
Komatsu’s digital solution Precision opens up new opportunities to work in a smarter and more efficient way.
Thanks to technological developments, it is now possible to show the machine's position to within just a few centimetres, providing the foundation for many functions that facilitates the forest machine operator’s working day. Precision is now expanding with more useful benefits, such as line following with guidance support. Precision includes many features that help increase productivity while providing the operator with important information and support to make wise decisions.
With geofencing, it is possible to draw in digital fences when planning the object, around the work area or to mark a protected area. Selectable alarms then alert the operator if the machine is too close to the border, providing extra peace of mind. The high precision also provides advantages such as being able to mark boundaries and areas digitally, based on map data from, for example, drones or LiDAR scanning. An accurate visualisation of the machine on the map as well as higher resolution map layers are other practical features.
Another area of use is stem code visualisation, which means that individual stems can be visualised with stem codes based on, for example, biodiversity considerations. Stem coding supports the operator in their work, enabling them to make better decisions more easily. It will also be easier to comply with directives, such as distances between future trees. Precision can also show the exact position of the felled logs, not just where the tree was cut. This feature allows the operator to know exactly where the timber is, even when it is dark or has snowed. This will also make it easier to see the assortment found in each log pile or at the roadside.
Precision is constantly evolving, and new features are being added. New for this spring is the feature guidance support for line following, which helps the operator stick to a particular path. The person planning the route also sets limits for deviations and if the machine starts to deviate from the planned course, a guide will support the operator in how to navigate back to the line. This function is very useful when planning, for example, strip roads.
It is also important that the user experience is as smooth and intuitive as possible. A new feature is the ability to set zoom levels for different working modes. The zoom is automatically adjusted during work based on the operator’s presets, ensuring a more seamless experience throughout the working day. The functionality of the map layers has also been improved. For example, it is possible to import data layers, activate boundaries such as area boundaries, and add detailed information about a data layers. A new feature also allows the operator to select how felled stems should be visualized on the screen. Either as individual logs for full control of production or grouped together to give a good overview. Source
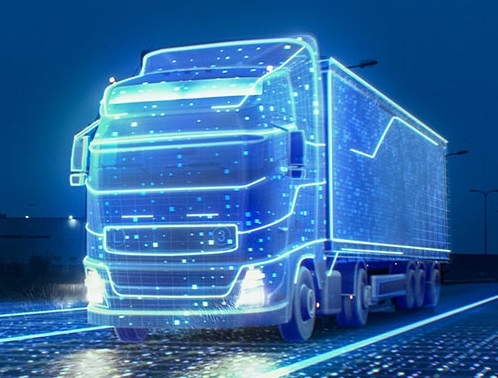
Virtual sensors are an emerging software-based technology that can make a big difference in how we monitor and manage engines and vehicle performance.
Unlike traditional sensors, which are physical pieces of hardware that need to be installed in specific places within the engine to work, virtual sensors work by using data from other sources within the vehicle's system. They help in calculating crucial aspects like temperature, pressure and speed of an engine, without the need for additional equipment. Building a virtual sensor requires a thorough understanding of the engine system. It relies on a statistical model to accurately predict critical parameters. The field of virtual sensors is a complex and very interesting engineering. Significant improvements in the computing power of microprocessors combined with the latest advancements in modeling technology over last decades, have made it possible to run these complex virtual sensors at runtime on Electronic Control Modules.
For OEMs of medium and heavy-duty vehicles, like trucks used in construction or delivery services, the broader adoption of virtual sensors will be a game changer. For example, instead of installing multiple physical sensors throughout the engine to monitor temperatures, a virtual sensor can use data from the existing sensors to create a complete and easy-to-understand picture of temperatures throughout the entire engine. This helps manufacturers save on costs, maintain the vehicle better and prevent issues before they arise. This also optimizes performance and makes vehicles run more efficiently with less environmental impact like lower greenhouse gas emissions.
The transition from physical to virtual sensors provides multiple benefits, the most important being substantial cost savings. OEMs can save on costs by decreasing the need for replacement parts in an engine’s sensor system while also freeing up space. Additionally, it reduces potential failure modes, by eliminating a component that may need to be serviced or replaced.
Virtual sensors make it easier to ensure an engine has the latest sensor and monitoring technology. Since virtual sensors are software-based, upgrades can be installed using a nearby computer or even Over The Air (OTA) using wireless networks. This removes the need to take apart the engine to install new parts or bring a vehicle into a maintenance facility. This in turn minimizes downtime and gets the vehicles back on the road quicker. Virtual sensors also play a key backup role in providing critical intelligence on vehicle performance even if some sensors fail. Thus, allowing continued limited use of the vehicle in safe conditions.
Another significant benefit of virtual sensors is the overall weight reduction of not only the physical sensor but also of the harness which connects the sensor to the ECM. In the long run, cumulative weight reduction efforts in a vehicle can have a positive impact on fuel economy, a critical factor especially in medium and heavy-duty vehicles. Reducing the vehicle weight directly increases fuel efficiency and cuts emissions.
Lastly, in their development virtual sensors have already made engine testing processes significantly more straightforward and environmentally friendly. Traditional engine testing methods, namely using test cells, are not only cumbersome but also a contributor to emissions. With virtual sensors, tests are done through computer simulations, reducing the need for physical test cell environments. This not only simplifies the testing process but also aligns well with the global push towards reducing
Long-haul trucking operations stand to gain from using virtual sensors as they allow for the close monitoring of engine temperatures, which can prevent overheating and optimize the vehicle's performance over long distances. Similarly, delivery vehicles used for transporting temperature-sensitive goods can use virtual sensors to maintain precise temperature conditions, which is crucial for the safe transit of perishables, while simultaneously monitoring parameters like fuel pressure and coolant temperature.
Construction and mining operations are renowned for their demanding environments. In these sectors virtual sensors play a pivotal role in safeguarding engines from potential damage due to fluctuating oil levels or high pressure and help to lengthen the lifespan of vehicles. Of course, emissions monitoring in these applications also assists fleet owners in adhering to increasingly strict environmental and emissions regulations.
In conclusion, virtual sensors are emerging to offer exciting possibilities for industries everywhere. Imagine better ways to predict when machines need fixing or how to save fuel in vehicles. As technology keeps improving, virtual sensors will likely become a normal part of how we do things, making processes more efficient and reliable. Source
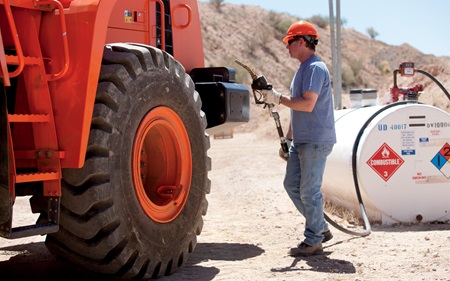
Learn more about fuel management systems, auto idle & various power modes.
The cost of diesel fuel remains a primary concern for contractors in the construction industry. Fuel costs can constitute a significant portion of operational expenses, particularly on large projects or when equipment operates in less populated areas, requiring longer-distance fuel transportation.
The evolution of nonroad diesel engines has helped with fuel consumption, and manufacturers are also designing dozers, excavators, wheel loaders and articulated dump trucks (ADTs) with cutting-edge heavy construction equipment technologies. These include real-time fuel management systems, automatic engine start-and-stop features, and selectable power modes. These innovations can go beyond fuel saving and reduced emissions — they can also increase equipment longevity and improve efficiency.
Newer technologies on construction equipment can help optimize fuel consumption and improve overall efficiency. Here are several technologies of importance.
- Fuel Management Systems: Fuel management systems offer real-time monitoring capabilities, allowing you to track fuel consumption for each machine. You can use the live data to make informed decisions about equipment usage, maintenance schedules and operational practices. These monitoring systems generate detailed reports that break down fuel efficiency metrics, including information on fuel consumption patterns, high-consumption periods and locations of specific machines. They can also be configured to send alerts or notifications based on predefined thresholds. For example, if a machine’s fuel consumption exceeds normal parameters, the system can automatically notify you and your dealer, prompting an investigation into such potential issues as fuel leaks or inefficient operation. One major benefit is that fleet management systems often integrate with maintenance scheduling tools. This integration allows you to align fuel efficiency with preventive maintenance, ensuring the equipment operates at peak efficiency. Regular equipment maintenance helps prevent issues that can lead to increased fuel consumption.
- Automatic Engine Start-&-Stop Systems: Also called idle management systems, automatic engine start-and-stop systems are designed to optimize fuel consumption in heavy equipment by automatically managing engine idling. Engine idling is a significant contributor to fuel waste in the construction industry. These systems shut off the engine during periods when equipment is not actively working, such as during breaks, waiting times or temporary halts in operation. When the equipment is ready to resume work, the system starts the engine, so there is minimal disruption to workflow. The systems can be equipped with an option to override the automatic function in situations where continuous engine operation is needed. In addition to saving fuel, auto idle can contribute to the overall health and longevity of heavy equipment. Reducing unnecessary idling minimizes the stress on the engine, contributing to extended service life and reducing maintenance costs.
- Power Modes: Heavy machinery can be equipped with power modes, which are designed to balance power output and fuel efficiency to adapt to different working conditions. The eco, or economy, mode is geared toward optimizing fuel efficiency without compromising overall productivity. In this mode, the engine operates at lower revolutions per minute (rpm) to reduce fuel consumption during less demanding tasks or when maximum power is not needed. This is especially beneficial during periods of idling or with lighter workloads. Proper training on how to use different modes helps maximize efficiency, extend equipment life and minimize fuel consumption. Your local equipment dealership can help make sure your construction equipment is outfitted with the right fuel-saving technologies.
- Evolution of Engine Technologies: Today’s diesel engines in construction equipment are very different from what was on the market even 10 years ago. The advancement from mechanical to electronically controlled engines has made diesel engines significantly more efficient. These systems continuously monitor and adjust various engine parameters in real time, optimizing performance based on the specific operating conditions while minimizing fuel emissions. Autonomous technology is another notable trend that may lead to reduced fuel consumption because owners will have more control of the machine operation. And this technology can enhance safety by reducing the need for operators on high-risk jobsites. The remote monitoring and control can offer real-time insights into equipment performance and enable quick responses to any issues that may come up.
- Telematics Technologies: Telematics systems are revolutionizing the construction industry by providing real-time insights for contractors, including the location, performance and usage patterns of heavy machinery. Telematics systems utilize GPS, sensors and data analytics. By leveraging this data, contractors can make informed decisions to streamline routes, reduce idle time and ultimately curtail fuel consumption. Source
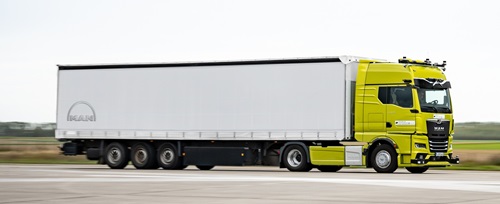
New development partnership with Plus aims for real-life use of autonomous trucks in hub-to-hub transport.
MAN Truck & Bus continues to drive forward the development of driverless transport between logistics hubs. The technology has the potential to reduce fatigue accidents, alleviate the increasing shortage of drivers and make transport processes even more efficient and environmentally friendly. In order to further intensify the development towards real-life logistics applications, MAN agreed to a collaboration with the US specialist for automated driving systems Plus. This is part of an overarching development partnership for autonomous driving between MAN parent company TRATON and Plus, which includes as well other brands of the TRATON GROUP.
MAN has been advancing autonomous driving for many years with various research and development projects. From 2018 to 2020, MAN developed and tested a driverless truck in container handling on the premises of the Port of Hamburg in a joint research and development project with Hamburger Hafen und Logistik AG. From 2019 to 2023, the ANITA project with partners Deutsche Bahn, Hochschule Fresenius, University of Applied Sciences, and Götting KG focused on the complete digital integration of an autonomous truck into the logistics process of container handling from road to rail. And since 2022, MAN has been working with twelve partners from industry, science, technical testing and road operations in the ATLAS-L4 project to develop an autonomous truck for use in motorway transport between logistics hubs.
The project thus specifically addresses the law on autonomous driving passed in Germany in 2021, which already allows driverless driving on defined routes with technical supervision. Practical test drives of the prototype with a safety driver on the motorway are planned for the end of the project. From 2025 onwards, further projects in specific customer transport applications will drive development towards series application. Source
Mack Introduces Mobile Off-Grid Charging System to Help Customers Test Electric Vehicles
In an effort to help customers investigating e-mobility for Class 6-8 vehicles and the feasibility for their fleets, Mack Trucks has built a mobile off-grid charging system that will be integrated into the body of a Mack® MD Electric truck. Source
Bandit announces the formation of an expanded and diverse management board
The formation of this group will give better representation for all areas throughout the company. With these additions, the management board expands significantly. This board will lead a dedicated group of employees that strive to engineer, manufacture, and support the multiple tree care and recycling products manufactured and distributed worldwide. Source
Read MoreTo see the full list of international logging, roading and trucking conferences and expo’s, please click the “Events” tab at the top of the page.
Read More