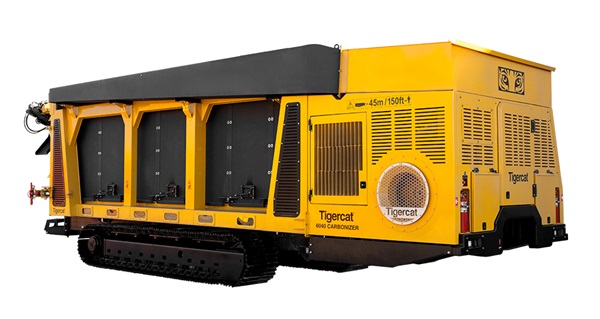
The long awaited 6040 carbonizer is ready for market and set to revolutionize the processing and handling of waste wood biomass.
Tigercat Industries is pleased to announce the official release of the 6040 carbonizer. This long awaited product replaces the 6050 carbonator that Tigercat marketed for a brief time after acquiring the product through the purchase of ROI in 2019. The mobile onsite wood conversion system is once again available in the marketplace after a comprehensive, ground-up redesign.
The 6040 is one of the most environmentally friendly wood debris reduction and conversion systems available on the market. The machine inputs woody debris and produces a high quality organic carbon with up to 90% material reduction. It is an ideal solution for converting unwanted logging and agriculture residue into a useful, high grade organic carbon that can be left onsite as a soil additive or marketed for many different commercial uses. The process captures 20 to 30 percent of the available carbon in the feedstock and sequesters it for thousands of years, furthering the goals of greenhouse gas (GHG) reduction. The innovative conversion process operates at high throughput levels and produces very low emissions because the gasses are combusted in the controlled combustion zone.
The 6040 redesign addresses performance related issues experienced in the original design and represents the knowledge of the applications that Tigercat engineers and field support personnel have gained over the past five years.
Great care has been taken to create a machine that allows modular replacement over time. For instance the grates in the carbonizing chamber are now made up of seven different sections that can be rotated 180 degrees to balance wear and extend life. Individual sections can be replaced as required. The undercarriage, auger trough, and conveyor system are all bolt-on sections to the main carbonizing chamber frame. Everything can be separated for service and replacement if required. The modular bolt-on design also allows for differing expansion rates of these major components.
The replaceable thermal-ceramic panel seal plate design has been improved, reducing panel wear. The composition of the panels has been altered to decrease back-face temperature while storing and utilizing more of the heat energy produced during the carbonizing process. This provides a more stable and sustained temperature within the carbonizing chamber. The result is increased efficiency, higher infeed rates, reduced emissions, and a greater yield of higher quality organic carbon.
The auger trough is designed for minimal air leakage, assisting with under-air efficiency, further defining the secondary combustion zone, while reducing hotspots that could form from an inefficient base pressure or vacuum. Unlike the 6050, the auger trough, where the quenching process takes place, is entirely sealed. Once the organic carbon drops through the grates, it is fully quenched by the water bath. An onboard hydraulic water supply pump and integrated automatic water level control system reduces water consumption by about 50% compared with the 6050. Automated water fill, level control, and water retention provides the operator a window of time to replenish the water supply if required.
The adjustable conveyor simplifies handling and management of the organic carbon product. It pivots 105 degrees from side to side and can be raised or lowered. The conveyor easily folds for transport and does not have to be detached from the machine frame.
Temperature control sensors are located throughout the machine. This, coupled with the Tigercat designed operating software and telematics system, improves data access and customer support. The 6040 development also emphasized parts commonality among other Tigercat products including pumps, motors, valves and filters, simplifying parts inventory management at the dealer and end user level.
The overall machine weight has been reduced from 43 550 kg (96,000 lb) to 37 650 kg (83,000 lb). Extended track frames improve load distribution on the trailer and reduce soil compaction on the ground. Source
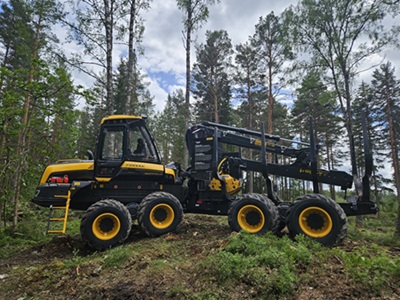
Ponsse is presenting new features to support forest machine operators’ daily work and to assist forestry entrepreneurs to follow up on the fleet’s profitability and productivity.
The new solutions include the Ponsse Scale crane system, which manages load data during all working stages, and the Ponsse High-Precision Positioning solution, which helps the machine operator know the exact location of the machine and the harvester head. Ponsse are also presenting a fossil-free material concept load space. Ponsse is the first forest machine manufacturer in the world to show a part of forest machine made of SSAB fossil-free steel.
Ponsse have manufactured a Buffalo forwarder´s load space of SSAB fossil free steel. This is a material concept to invest in the workability, behaviour and characteristics of the new material used in forest machine manufacturing. The load space is designed only for material testing and does not correspond to production models. The material concept is part of the FORWARD27 ecosystem project.
Ponsse Scale is a crane scale system that weighs, sorts, saves and manages load data during all working stages. The collected weighing data makes load handling routines easier. Precise weight measurements ensure an optimal load at all times. It features full weighing automation during both loading and unloading, with detailed load registration. Whether loads are grabbed in the middle or off-centre does not affect the weight result. Load details, load logbooks and measuring accuracy data are available in easy-to-read reports. PONSSE Scale has excellent weather resistance, with accurate results in both hot summer temperatures and winter’s sub-zero temperatures. Ponsse Scale can be installed in all Ponsse forwarder loader models.
Ponsse High-Precision Positioning is a solution that helps the machine operator know the exact location of the machine and the harvester head. This enables the effectiveness of logging operations to be maintained, even in changing conditions. Utilising industry-leading navigation and location tools, as well as Ponsse’s own advanced technologies such as Active Crane, High-Precision Positioning can raise the reliability bar to a level conventional positioning systems often don’t reach. By defining the exact location of the harvester head and presenting it on a map view, High-Precision Positioning can significantly improve harvesting productivity. The solution clearly shows where the operator should harvest and the areas that should be avoided. Every stump location is saved in the production file, and the driving path the harvester creates is clearly visible to the forwarder.
High-Precision Positioning is available in Finland, Sweden and Germany for all Ponsse harvesters equipped with Active Crane, and it can also be retrofitted. Availability for other markets will be specified later. Source
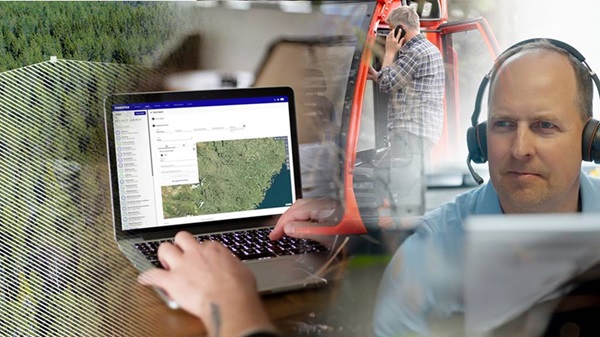
Smart Forestry is best described as a collection of digital solutions that help make the workplace safe, smart, productive and sustainable.
Digital development in the forest machine industry is seeing constant progress. MaxiFleet has offered a comprehensive tool for simplifying the working days – whether that means keeping track of machines, collaborating with colleagues or making smart decisions. Komatsu are now entering the next era of smart digital solutions where the features in MaxiFleet have become part of a new concept - Smart Forestry.
The concept encompasses Komatsu’s digital solutions – including all the features currently offered by MaxiFleet. However, Smart Forestry is a broader concept compared to the previous offering, and the goal is to develop it into a platform where Konatsu, together with customers, partners and other stakeholders, can create new types of value-creating solutions.
At this point, Smart Forestry consists of three different applications, making it easy to find the best solution for you.
- Fleet Monitoring provides you with full control over your machines, with the ability to plan remotely and all the necessary remote control functions – including support.
- Vision includes all functions for practical map layers, collaboration between operators and the ability to monitor all production in real time.
- Precision provides the ability to use the latest positioning technology to simplify the working day and reach new levels of precision for the work. Source
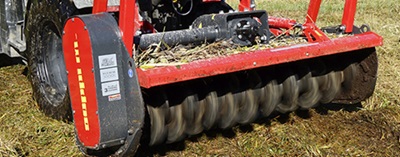
Seppi M introduce the upgrade of their proven, powerful, and versatile Miniforst forestry mulcher.
The Miniforst is designed to mulch brush and wood up to a diameter of 20 cm (8 in), making it ideal for smaller and medium-sized tractors with an engine power range of 60 to 100 hp (44 to 74 kW) and despite its compact size, this forestry mulcher offers impressive performance and precision.
The Miniforst is a multifunctional device with applications from forest and woodland management to the maintenance of orchards, vineyards, and berry plantations, as well as post-harvest cleaning. Additionally, the Miniforst is also ideal for maintaining power and gas lines and creating firebreaks for governmental and commercial use.
With a reinforced housing, robust gearbox with freewheel and through-drive shaft, and hydraulically adjustable rear hood, it is ready to withstand the most demanding challenges in forestry and landscaping. No matter which tool you choose, all Miniforst rotors are equipped with the dynamic Helix rotor and its wear-resistant tool holders. Thanks to the spiral arrangement of the tools, this system works particularly quietly and with low vibration, and enables excellent results with low energy consumption. These rotors are fitted as standard with the tried and tested Mini Duo tools, which are particularly popular with contractors in landscape maintenance.
To meet special working requirements, the Miniforst rotors can also be equipped with the optional Cut Control system. The wear-resistant brackets are supplemented with innovative cutting depth limiters. This innovative rotor system is available with two different tools: the tried and tested Mini Duo tools or with the fixed Mini Blade cutting edges, which ensure a smooth material flow, even with stationary logs. The new series of Miniforst features 3 rows of replaceable hardened Counter Cutter and 2 fixed Counter Cutter under the hood for maximum efficiency and longevity.
Depending on your needs, the Miniforst is available in working widths of 125 cm (49 in), 150 cm (59 in), 175 cm (69 in), and 200 cm (79 in) to ensure optimal coverage and efficiency. Source
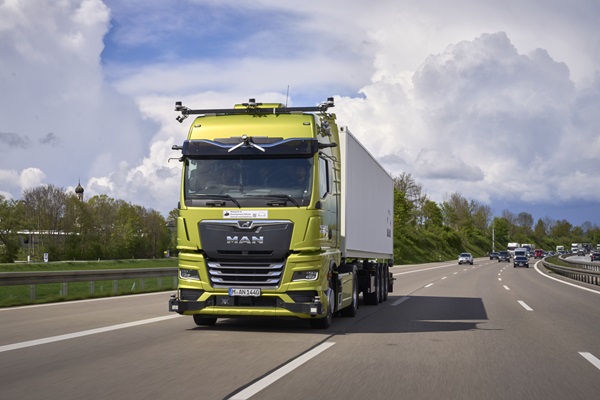
MAN Truck & Bus is the first commercial vehicle manufacturer to receive a Level 4 motorway test permit.
MAN has become the first commercial vehicle manufacturer to send an autonomous truck onto the German motorway. MAN has been intensively driving forward the development of autonomous trucks for use in logistics hubs and for hub-to-hub traffic on motorways for some time and recently became the first commercial vehicle manufacturer to receive a Level 4 test permit based on the law on autonomous driving on German motorways.
Freight volumes and, in particular, transport between logistics hubs – such as the warehouses of large online department stores – are growing steadily. The use of autonomous trucks in this so-called hub-to-hub transport is particularly suitable for this. The trucks are always on the road, extremely efficient in terms of consumption and safe to drive. There are no driving time breaks, so the vehicles can be perfectly integrated into tightly synchronised logistics processes. In the long term, the efficient use of autonomous trucks can reduce overall operating costs by ten to 15 per cent. The new technology can also alleviate the driver shortage. There is already a shortage of up to 100,000 truck drivers in Germany alone.
MAN has been driving autonomous driving forward for many years with various research and development projects. From 2017 to 2019, MAN developed and tested electronically coupled trucks in a joint research and development project with DB Schenker. These particularly safe and fuel-efficient platoons were used for more than six months in regular general cargo transport on the A9 motorway between Neufahrn and Nuremberg. From 2019 to 2023, the ANITA project with partners Deutsche Bahn, Fresenius University of Applied Sciences and Götting KG focused on the complete digital integration of an autonomous truck into the logistics process of container handling from road to rail. And since 2022, MAN has been working together with Autobahn GmbH and other partners from industry, science and technical testing in the ATLAS-L4 project to develop an autonomous truck for use in motorway transport between logistics hubs. The project is thus specifically implementing the law on autonomous driving passed in Germany in 2021, which already allows driverless driving on clearly defined routes and with technical supervision. Practical test drives of the prototype with a safety driver on the motorway are planned at the end of the project. To date, MAN has filed 133 patent applications in the field of autonomous driving, 33 of which have already been granted. By participating in the @CITY, BeIntelli and MINGA projects, MAN is also involved in the development of automated driving for city buses. Source
Volvo to launch hydrogen-powered trucks
Volvo Trucks is developing trucks with combustion engines that run on hydrogen. On-road tests with trucks using hydrogen in combustion engines will begin in 2026, and the commercial launch is planned towards the end of this decade. Trucks that run on green hydrogen provide a significant step for Volvo to achieve its net zero goal and support customers to reach their decarbonization targets. Source
Freightliner produces milestone 1 millionth Cascadia
Freightliner, a brand of Daimler Truck North America LLC (DTNA), celebrated a significant milestone with the production of the 1 millionth Freightliner Cascadia – the first Class 8 truck in North America to reach the seven-figure mark. Source
Read MoreTo see the full list of international logging, roading and trucking conferences and expo’s, please click the “Events” tab at the top of the page.
Read More