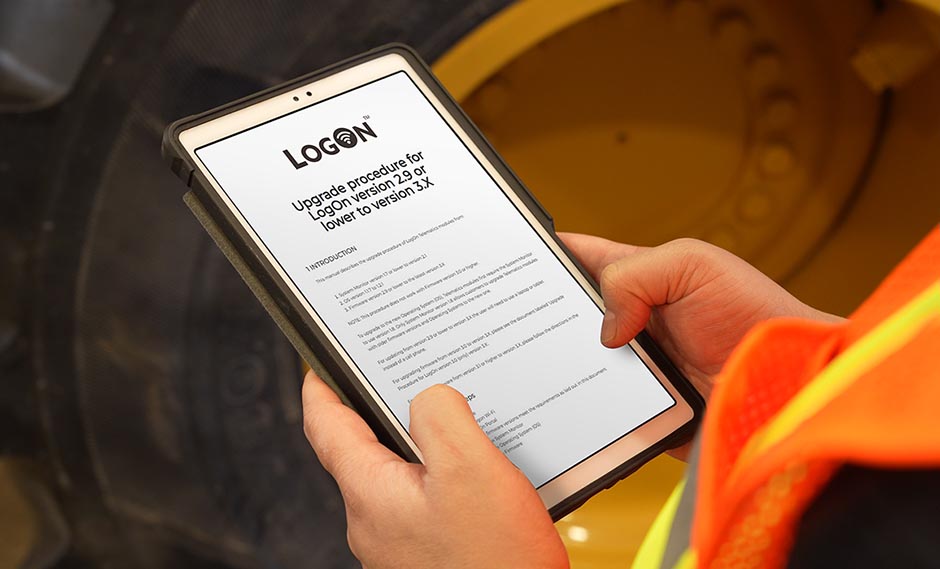
The upgrade provides added functionality, improved user interface, and to take advantage of the latest advanced engine diagnostics capabilities.
The update offers enhanced features for a more comprehensive telematics experience. For instance, a new display has been added to the information tab that displays information reported from TPMS, the Tire Pressure Monitoring System. This update is available for all wheeled machines.
Tigercat has also developed more advanced and comprehensive tools for troubleshooting. The LogOn interface provides easy-to-understand steps to diagnose issues, directly referencing the appropriate section of the service manual. Several diagnostic tests can be initiated directly from LogOn to further diagnose the underlying reason for the fault code. Compression, runup, and high-pressure rail engine diagnostic tests have been added to this important new update.
The update provides a more intuitive and user-friendly interface for easier navigation. For example, colour coding has been added to the Engine Diagnostics reporting screen to make it easier to comprehend the status of the test. This applies to all the tests available in Engine Diagnostics. The update also improves system stability and performance with resolved issues. Source
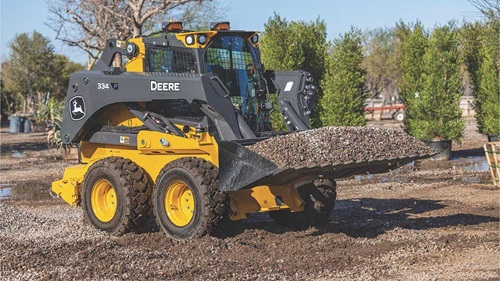
John Deere debuted five new P-Tier Skid Steer Loader (SSL) and Compact Track Loader (CTL) models.
Entering the market, the 330 and 334 P-Tier SSLs and the 331, 333 and 335 P-Tier CTLs boast a brand-new one-piece cab design with premium options, enhanced technology features, and an overall increase in operating power. With the introduction of new CTLs and SSLs also comes the debut of three brand new attachments, including the MK76 and MH72D mulching heads and the CP40G cold planer. Expanding offerings in grade management solutions on compact models, the 333 and 335 P-Tier machines can be equipped with John Deere SmartGrade™ technology, helping to boost productivity on the job.
Prioritizing operator comfort and capability, the new P-Tier models boast larger, fully redesigned operator stations. Built from the ground up with direct feedback provided by customers, the new models feature multiple styling upgrades. The new operator station is sealed, pressurized, and isolated from the frame to help improve operator comfort and productivity. This means that outside noise will be lowered, and the cab interior is better protected from the elements.
Utilizing the eight-inch touch-screen display interface, available on the full line-up of P-Tier models and standard on the 334 and 335 P-Tier. Customers can experience better insight and customization of machine settings and viewing information. When the premium display is selected, a range of standard features and benefits are included within the software.
Also enhancing comfort, a new premium heated and ventilated seat allows those working in all types of climates to be comfortable during hot summers or frigid winters.
Onboard Grade Indicate is standard on the new touchscreen display. This feature displays the cross-slope and main-fall of the machine in either degrees or percent and allows operators to use a relative benchmark to assist in maintaining a desired grade.
Helping take control to the next level, the optimized joystick controllers enable more tasks to be completed with easy to reach and adjustable controls that offer personalized setup. The new 25 Button SSM puts all functions in one spot, eliminates rocker switches, and makes it easier to quickly make machine adjustments while operating.
With a focus on serviceability, the new cab tilts up in one piece, giving ground-level, all around access to the engine, drivetrain, and undercarriage of the machine. A single operator or technician can raise the boom and enable the mechanical lock out from within the cab. In addition, visibility has increased 20% over G-Series, improving visibility out the front, sides, and back to the machine.
Two brand new technology capabilities make their debut with the rollout of these models, including Attachment Manager and Surround View. Attachment Manager, available as an upgrade on the 330, 331 and 333 P-Tier Machines and standard on the 334 and 335 P-Tier models, takes the guesswork out of determining optimal attachment performance parameters by enabling preprogrammed flow and pressure for John Deere attachments, resulting in optimal productivity. From displaying the key attachment parameters on the screen while running to being able to save or select performance parameters depending on the tool, this new feature helps increase operator confidence and productivity, and helps prevent damage to the attachment correlated to incorrect machine settings during usage.
Surround View technology, available on all P-Tier models, stitches together views from around the machine to provide a birds-eye-view image to the operator to assist with increasing situational awareness and giving more confidence to operators to navigate jobsites with ease. When reversing, the display will automatically switch to the rearview camera which gives the operator a closer view of what's behind the machine. Surround View dynamically integrates two boom mounted cameras in addition to a rear camera onto a dedicated monitor that provides a 270-degress view of the sides and rear of the machine. Adding enhanced visibility and situational awareness for operators can help prevent damage and keep operators safer on the job.
Lastly, the John Deere Operations Center™ will continue to be included on all large-frame CTL and SSL, enabling fleet managers to monitor machine location, codes, fuel usage and other key features more efficiently. Enabling data sharing with a dealer streamlines maintenance and repairs and can help prevent downtime when issues are identified early.
Looking at the latest in mulching attachments, the MK76 and MH72D Mulching Heads are designed to work with the 333, 334 and 335 P-Tier models to take on land clearing needs in stringy, fibrous, dense, and fast-growing cycles. Designed to tackle clearing applications, the optimized knife style head on the MK76 is ideal for fibrous vegetation. In addition, these mulching head attachments produce the finest chip of all John Deere mulchers, broadcasting discharge to mitigate piles. Source
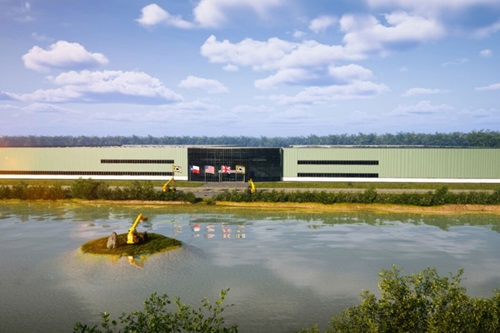
This is the biggest-ever investment in the company’s history.
The start of construction was signalled at an official ground breaking ceremony at the site in San Antonio, Texas, where The Hon. Alice Bamford, daughter of company Chairman Anthony Bamford, cut the first sod of earth.
Work on the 720,000 sq. ft (67,000m²) factory is under way on a 400-acre site and will create 1,500 new jobs over five years. It will be the company’s second largest plant, rivalled only by the manufacturer’s World HQ in Rocester, Staffordshire, UK. The factory will make Loadall telescopic handlers and aerial access equipment, with production scheduled to start in 2026. The factory will also have the capacity to expand into the manufacture of other products in the future.
Chairman Lord Bamford said: "Construction equipment manufacturers sell more than 300,000 machines every year in North America, making it the single largest market in the world. JCB has been growing its share of this important market steadily over the past few years and the time is now right to invest in our manufacturing capacity in North America, where we already have one factory."
Texas is an obvious choice for JCB’s new North American manufacturing facility, not least because the State is the largest consumer of construction equipment in the USA. San Antonio is also the logical choice as a location for the new factory because of its central location, proximity to the supply chain and great local labour force.
JCB sold its first machine in North America in 1964 and opened its first manufacturing plant there in 2001 in Savannah, Georgia, which employs 1,000 people. The new facility will manufacture machines for customers specifically in North America.
JCB employs 19,000 people and has 22 factories around the world, including 11 in the UK, seven in India, and others in Brazil and China. The company will mark its 80th anniversary in 2025. Source
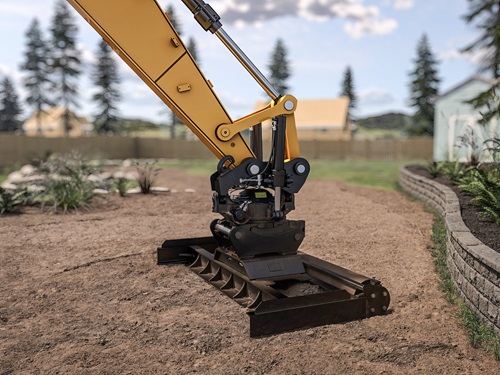
This allows contractors to take on dynamic and efficient grading and compaction work using excavators.
New Cat® Grading Beams for Cat Tiltrotators. Pairing with Cat Tiltrotators enables 360˚ bidirectional and 40˚ left-and-right rotation of the grading beam to increase attachment versatility. The grading beams’ mechanically adjustable roller – from 10 mm (0.40 in) below frame to 20 mm (0.79 in) above – flexibly tailors the desired level of compaction based on material type. Preventing material from sticking to the roller, the adjustable roller scraper allows the attachment to be used with clay, silt and other sticky materials.
Available in five widths from 1250 to 3000 mm (49 to 118 in), Cat Grading Beams quickly tackle a range of applications from grading sidewalks to larger site prep applications. The design’s large top opening with solid extended sides and side plates allow the beam to spread, compact, and grade materials quickly and effectively. Highly abrasion resistant, Hardox 500 wear protection at the bottom of the beam protects the frame for long-life operation. The beam’s welded frame increases structural rigidity, while additional support plates on the heavy-duty frame extend beam strength and overall service life.
Compatible with Cat Grade technology via the Cat Tiltrotator attachment, contractors can grade to plan using Cat Grading Beams, improving accuracy and saving time. Available tool recognition automatically confirms the identity of the attachment to ensure all settings – pressure, flow and dimensions – are correct, allowing operators to quickly get to work.
Standard Cat PL161 attachment technology provides simple attachment tracking across all worksites, reducing the chance of a lost grading beam and assisting with maintenance and replacement. The PL161 integrates into VisionLink® for fleet management from a single mobile device. Source
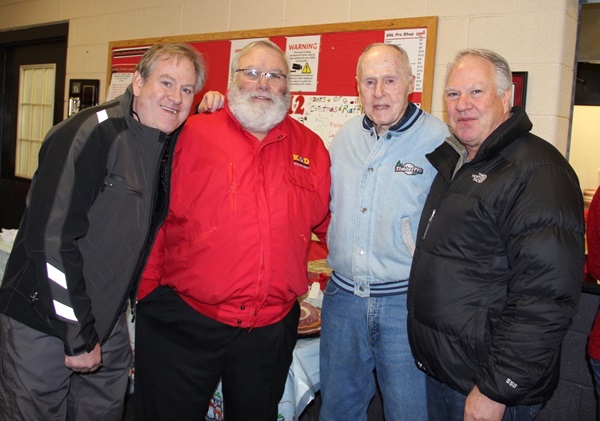
The timber industry leader leaves a decades-long legacy of innovation and generosity.
After seven years as president of TimberPro, Lee Crawford has announced his retirement. This draws to a close Crawford’s nearly 40 years in the forestry machinery business, during which he consistently exemplified entrepreneurial spirit and a caring attitude.
Pat Crawford, Lee’s father, was a third-generation logger whose company — Shawano, Wisconsin-based Timbco — had become known for its popular line of levelling machines. But Lee never planned on entering the forestry industry, becoming an engineer at the Oshkosh Truck Company in 1982.
In 1985, however, Lee’s father asked him to join the family business at Timbco, where he started on the assembly line. “It gives you credibility with your people,” Lee said. “And you learn the products. You learn what needs to be changed.” After his assembly line shifts ended, Lee kept working, ordering parts and writing warranties.
Lee eventually become Vice President in 1992. In 2000, Timbco was sold to Partek, a Komatsu-owned company. The Crawfords bought back the wheeled division from Partek in 2002 to form TimberPro, which became recognized for its innovative track machine products. TimberPro was acquired by Komatsu in 2019.
Lee considers everyone he works with his “TimberPro family.” Patrick Anderson, Product Supervisor, joined TimberPro at its founding, and called Lee one of the most compassionate people he knows. “As Vice President of the company, he went to fix a valve all the way out in South Dakota on Christmas Eve,” Anderson says. “He’s family-first, but he still goes out of his way to make sure you can spend time with your family.”
Joe Hardwick, Vice President of New Hampshire-based logging company D.H. Hardwick and Sons, has a similar story to tell. Two days prior to a logging expo in 2010, the engine of his machine died prematurely. The manufacturer wouldn’t help since the warranty had expired just a few hours prior. Hardwick met Lee at the expo and told him what happened to his machine. Lee, shocked that the company had done nothing, told Joe, “I will get you a new motor at no cost to you. The only thing I ask is the next time you buy a machine, you give ours a try.” Hardwick has remained a TimberPro customer since, and calls Lee a “great mentor.”
In retirement, Lee plans to stay involved in charitable giving with the Ruth and Pat Crawford Foundation, which has donated millions over the years to community organizations and food pantries. While the TimberPro family is sad to see Lee go, the legacy of the Crawford’s ingenuity and generosity will continue with Komatsu at the helm. “By taking Komatsu’s strengths and combining it with TimberPro’s, we can be a leading supplier. We’re really excited about the future,” said Doug Morris, Vice President, Forest Machine Business Division at Komatsu.
Lee feels safe leaving his companies in Komatsu’s hands. “Komatsu wants TimberPro to grow. Komatsu has the means and ambition to plan and grow our offerings over time,” he says. “My family was comfortable. Komatsu has the drive to get bigger and bigger and bigger. It’s going to be exciting.”. Source
Cranab AB becomes importer for Metsatek timber truck superstructures
With a new cooperation, Cranab is expanding the product range for their truck crane customers. Their new partner Metsatek offers solutions of high quality in the manufacture and installation of timber truck superstructures. Metsatek is a leader in the Baltic automotive industry. The company has produced and installed machinery for timber transport since 1993. Source
Cummins announces their new X15 diesel engine for heavy duty on-highway trucks that is aligned with 2027 regulations
The new X15 advanced diesel engine is Cummins’ most efficient yet, designed for the Cummins’ fully integrated powertrain featuring Eaton Cummins Automated Transmission Technologies and Cummins-Meritor. Maintaining the traditional reliability and lower operating costs that have met the needs of a diverse customer base since the inaugural X15 launch in 1998, the next generation, advanced diesel X15 will feature improved greenhouse gas and fuel efficiency benefits while retaining the same ratings of the current X15 (up to 605 horsepower) and optimizing powertrain integration with Eaton Cummins and Cummins-Meritor. Source
Read MoreTo see the full list of international logging, roading and trucking conferences and expo’s, please click the “Events” tab at the top of the page.
Read More