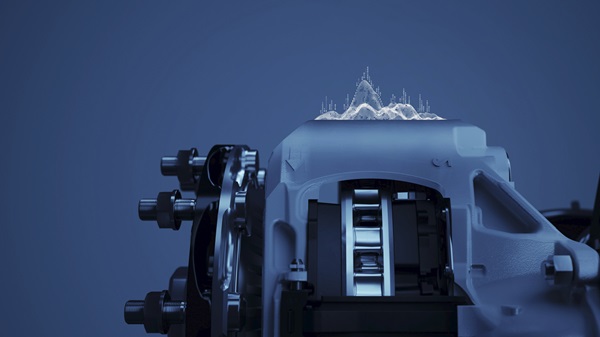
The AI revolution in transport is unstoppable!
The trailer now recognises its optimum load based on the axle loading, checks critical components - and issues a warning before things get expensive and dangerous. The new iC Plus running gear generation from BPW uses intelligent algorithms to analyse braking performance. Something that has been saving testing and downtime in the UK for years is now rolling out across Europe for the first time.
With the new iC Plus running gear generation, which comes with telematics hardware as standard, BPW is now creating the basis for the introduction of artificial intelligence into the trailer: intelligent algorithms detect data patterns in the running gear that e.g. indicate the need for maintenance of critical components. Above all, this includes the brakes: iC Plus informs the driver, fleet manager and dispatcher when the brakes need to be checked in the workshop. Causes can include a defective air hose, a sluggish brake calliper or a weakening spring on the cylinder – typical maintenance and repair tasks are recognised by artificial intelligence before expensive breakdowns or even accidents can occur. The highlight: BPW does not need separate sensors to analyse the braking performance, but instead accesses the data collected in the EBS. In addition to the brake lining wear sensors, the AI interprets the need for maintenance and repair in a differentiated manner in context. Temporary reaction patterns – triggered by a severe pothole, for example – are filtered out.
Brake performance measurement has already proven its worth in the UK, where close-meshed brake checks for trailers are required by law. For years, here, AI has been saving fleet operators expensive downtimes on the brake test stand. With the iC Plus running gear generation, BPW is also adapting its innovation for the rest of Europe.
Brake lining wear measurement is also tried and tested with iC Plus. It works with a sensor whose signals give the fleet manager sufficient flexibility to plan a workshop visit to change the brake lining. The BPW Group's digital services are also proving their worth here: the digital maintenance management system from BPW and idem telematics integrates statutory inspection regulations, maintenance instructions for BPW axles and vehicle status and fault messages. It also documents maintenance work down to the last detail – creating a digital vehicle file without any paper, hole punches or folders. Source
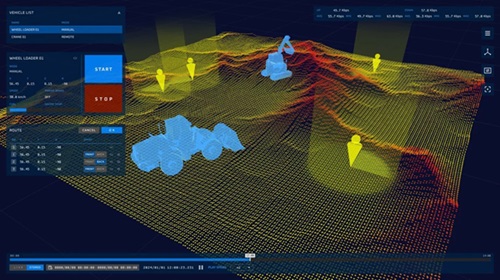
This enables the management of construction progress and the operation of autonomous construction machinery from a remote location on the Internet.
Hitachi developed a real-time digital twin platform that reproduces the construction site in a virtual world from data collected in real time, in cooperation with aptpod, Inc.. Utilizing this platform will enable Hitachi to collect various types of construction-related data and achieve progress management and the operation of autonomous construction machinery from a remote location on the Internet with the goal of realizing construction sites where people and machinery work in a coordinated manner.
In recent years, labour shortages have become an issue in the construction industry due to the decreasing birthrate and aging population. Customers have high expectations that autonomous construction machinery will become one solution to that problem. To meet these expectations, Hitachi Construction Machinery aims to realize construction sites in which people and machinery work in a coordinated manner to balance safety and productivity through "collaborative safety" by mutually sharing information about the "people, machinery, and site environment." Specifically, people would be alerted to pay attention and construction machinery would be controlled based on information collected by the machinery and sensing systems to carry out highly productive construction while guiding the overall site in a safe direction. To realize this type of construction, Hitachi Construction Machinery developed the "ZCORE" system platform for autonomous construction machinery in August 2020. In addition, the company invested in and singed a business alliance agreement with aptpod in May 2023 to promote the development of a digital twin system that visualizes an entire construction site and autonomously operates construction machinery.
This platform can reproduce real-time real-world construction site in the virtual world, including various information such as the location and operational information of construction machinery, the location and biometric information of workers, terrain changes due to the progress of work, and other construction site conditions. This will enable adjustments to be made to the work details of individuals and the control of multiple pieces of construction machinery working on site with low latency on the Internet from a remote location to realize construction sites where people and machinery coexist with a high degree of safety.
In the development of this platform, Hitachi Construction Machinery was in charge of providing the autonomous construction machinery (hydraulic excavators and wheel loaders) and defining the requirements for reproducing a construction site as a digital twin. aptpod developed the cloud system for data collection based on its "intdash" high-speed IoT platform and the mobile and PC user interface used by the workers, and Unicast developed the software for converting the terrain of a construction site into 3D data based on data obtained from LiDAR. The ability of the technologies from aptpod and Unicast to transmit and process large volumes of constantly changing data enables the construction of a highly real-time digital twin. Going forward, the companies aim to realize collaborative safety which includes advanced autonomous construction machinery and improved site safety and productivity through repeated verification tests for the purpose of practical application. Source
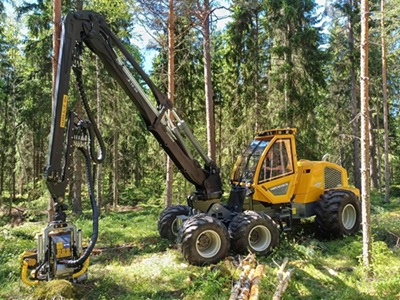
The HR56 is based on the bestselling HR46x four-wheel harvester with new features that improve both efficiency and productivity.
One of the hallmarks of the Sampo rosenlew machines has always been their suitability for thinning young forests, so the new model is a natural step in the development of the range. The familiar components used in the construction of the machine combined with their tried and tested technical solutions ensure low operating and maintenance costs.
The HR56 is equipped with a Logmer crane with 10-meters reach. This ensures less harvesting damage and more stability. The HR56 is equipped with a front bogie, so the surface pressure exerted on the ground by the six-wheeled machine is low. The front bogie combined with a low centre of gravity make the machine stable to work with. The HR56 harvester is an energy-efficient and environmentally friendly choice for thinning and harvesting energy wood. It is a comprehensively sensible package with low operating and maintenance costs. Source
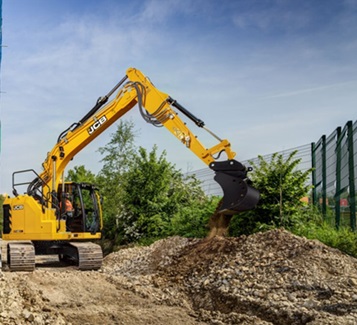
It is a reduced tailswing model that delivers good performance and productivity with compact dimensions and a full-size operator cab.
The 145XR reduced tailswing model builds upon the success of JCB’s larger 245XR, delivering impressive performance in a compact design with a minimal counterweight swing. The 145XR has a 27% shorter counterweight overhang than a conventional 140X. The machine weighs in at 15-18 tonnes, depending on specification, and can be supplied with a monoboom or a two-piece triple articulating (TAB) configuration. Powered by JCB’s proven Stage V Dieselmax engine, the 145XR boasts an output of 81kW (108hp). This features Auto-Stop and Auto-Idle engine functions, to reduce fuel consumption and emissions when idling. Engine working speed has been reduced to 1,700rpm, increasing fuel economy by 10% and cutting overall noise levels.
The machine is built with heavy-duty track components, plates, bearings, and features graphite bushings on key pivot points, allowing up to a 250-hour greasing interval. Hydraulic filter changes are extended to 2,000 hours, meaning this new machine requires 24% fewer filter changes over 10,000 hours of service, reducing operating and maintenance costs.
As with all X-Series models, the 145XR benefits from the full-sized JCB Command Plus ROPS cab. As well as being one of the largest on the market, with 2.86m³ of volume, the Command Plus cab benefits from a heated air suspension seat and a reduced in-cab noise level. The cab is further improved with a new 10” touchscreen monitor, with the JCB UX interface. The switch panel incorporates customisable hot keys, allowing personalisation for the operator. Climate control, keyless start, and twin cameras for added visibility are all standard.
The JCB UX interface has up to 25 user profiles, which can be customised for the operator to set preferred joystick configuration to meet their individual requirements. Mobile phone connectivity has been improved, with phone book integration via the monitor. The machine is easy to use and help guides are available within the monitor, along with ‘how to’ videos covering all of the features of the JCB UX system.
The 145XR is available with a range of options, to tailor the machine to an individual customer’s requirements. These include auxiliary hydraulic circuits with up to 15 attachment settings and a premium heated and cooled operator’s seat. LED lights are now standard, with options available to increase to up to 14 LED work lights. A birds’ eye 360 camera system, integrated within the 10” display, can also be offered, along with high visibility, all-round handrails. Source

Caterpillar’s online web platform has been enhanced with the introduction of three new features – Cat Grade and Compact, Operator Coaching, and E-Ticketing.
This unified platform is designed to give managers insights into jobsite productivity and equipment utilization. The scalable cloud-based application collects and summarizes data from any subscribed machine equipped with a Cat Product Link™ device, ensuring that fleets with mixed OEM equipment can be seamlessly incorporated into one unified platform.
VisionLink Productivity simplifies data management with its user-friendly dashboards. These include a comprehensive jobsite summary and detailed insights with key performance indicators (KPIs). The platform analyzes standard telematics data, such as machine location, fuel burn, and idle time, providing a clear overview of machine performance. For more in-depth analysis, advanced data from machines equipped with Cat Payload, Grade, and Compact systems provides more job-specific details.
VisionLink Productivity now incorporates Cat Grade 3D and Cat Compact data into its reporting platform. Leveraging Cat Grade Connectivity, the platform enables 3D design files and updates to be seamlessly distributed to all machines at the jobsite, eliminating the need for USB uploads. VisionLink Productivity further improves accuracy through GNSS corrections for position validation rather than installing a base station with high set-up costs for short projects. Grade Connectivity also minimizes machine downtime by reducing the need to send a technician onsite to diagnose Grade related issues, improving overall jobsite productivity.
Operator Coaching is a powerful tool that empowers operators of all experience levels to enhance their skills, efficiency, and productivity. Two categories of operator coaching tips – Operating Efficiency and Machine Health – are tracked. During machine operation, the operator receives an onboard notification when an action with a corresponding tip is detected, putting them in the driver's seat of their improvement journey. This helps to improve operational efficiency and increase machine longevity.
When paired with the offboard VisionLink Productivity, managers can remotely view what coaching tips their operators have activated. This enables site managers to track improvements over time and focus training on areas specific to the operator's needs and overall operations. Dashboards, lists, and maps allow quick views of each coaching tip's count, time, and location.
The new E-Ticketing feature brings convenience, eliminating the need for manual or printed tickets generated by onboard Cat Payload systems. Key personnel can now receive an electronic copy of the tickets via email, including detailed information on individual buckets, total payload, truck, and material type. Tickets can be quickly recalled using ID or number or filtering based on material type or truck name. Key performance indicators tracked by E-Ticketing include ticket count, average truck rate, pass count per ticket, and total ticket payload. Source
More Canadian product support from Tigercat
Tigercat adds product support representative for Quebec and northeastern Ontario with the the arrival of Éric Boulanger. Based in Rimouski, Québec and with over 30 years of experience in the forestry industry, Éric brings excellent product knowledge, unmatched tenacity, and a constant thirst for learning. Éric’s mandate will involve supporting and developing Tigercat products and their dealer network alongside Bruno Villeneuve, Keith Gauvreau, and Yannick Lapointe. Source
New Holland FieldOps™ is a new platform for real-time tractor data management
It is an easy-to-use and free platform available for mobile and web for customers worldwide to manage their machines and operation data from anywhere at any time. It enables customers to view and monitor all their machines in one place instead of using multiple apps to manage their mixed fleet, with an all-new interface designed to simplify farm management. Thanks to collaboration with Intelsat, a leader in satellite communications, New Holland and CNH will be the first in the market to make connectivity accessible to areas that do not have consistent internet access. Source
Read MoreTo see the full list of international logging, roading and trucking conferences and expo’s, please click the “Events” tab at the top of the page.
Read More