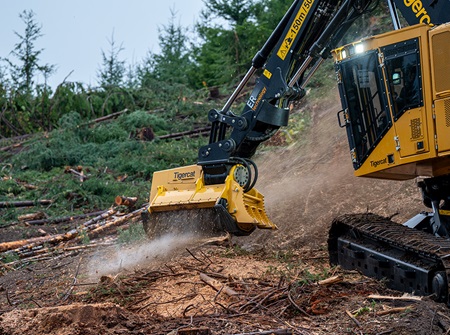
Tigercat has produced a mulching head for swing carriers.
Wildfire is proving to be one of the greatest challenges facing foresters, landowners, governments and environmental organizations in the 21st century. The summer fire season over the last several years in North America has devastated millions of hectares of forest land, destroying wildlife habitat and carbon sinks, while releasing massive amounts of carbon and particulate matter into the atmosphere. Excessive fuel build-up on the ground is having a devastating effect.
Tigercat recently released a mulching head designed to mount on a Tigercat LX830E carrier. This machine can tackle steep slopes and operate within dense stands to reduce build-up of woody debris as a mitigation measure to guard against future wildfires.
The new 4161-15 head has a 1,5 m (59 in) mulching swath, 130 degree wrist pivot, and a pin-on rake for added utility. Like all Tigercat mulching heads, it is strength-to-weight optimized and fitted with large bearings.
Many of the components including the bearings, sprockets, seals and timing belt are common to the Tigercat 4061 series mulching heads and thus field proven. Hydraulic hoses are routed through the open tip boom into the top of the wrist, providing excellent protection. The replaceable wear liner is field serviceable. Removable covers allow easy access to all service points. The LX830E carrier is powerful, compact and extremely capable on steep terrain. Source
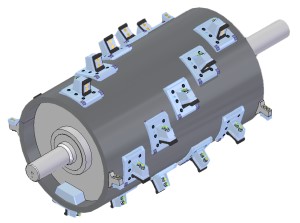
It is designed and manufactured to be an alternative solution for those grinding applications that may contain contaminants.
This highly productive 40 in (102 cm) capacity grinder is designed and manufactured to be an alternative solution for those grinding applications that may contain contaminants. A Caterpillar C32, 1,200 hp (883 kW) engine provides ample torque and horsepower for optimal machine performance and productivity.
The heart of the HM6420 is a 50 in (127 cm) diameter x 66 in (168 cm) wide hammermill. The heavy-duty mill features a 1.75 in (4.4 cm) drum skin custom formed from rolled plate. The mill is supported by a 7 in (18 cm) main shaft constructed of alloy steel that has been ultrasonic tested. Each pocket within the mill is manufactured from high strength A-514 steel. These combinations create a structural sound mill for added durability and integrity. The mill is equipped with 20 carbide infused hammer inserts built to withstand the toughest material fed into the machine. Each holder is securely attached to the mill via a patent-pending quick change pocket system. Each holder recesses into the mill pocket, increasing durability. A top plate covers the pocket and holds in place by six hex bolts. The hammer insert is attached to each holder utilizing two bolts. With this set-up, the mill hardware is easier and quicker to replace.
A heavy-duty slat-style infeed conveyor is directly driven generating over 18,000 lb (8,200 kg) of pulling power. The large diameter feed wheel is also directly driven and provides an additional 17,000 lb (7,700 kg) of pulling power and 8,650 lb (3,900 kg) to 17,300 lb (7,850 kg) of down force when hydraulic pressure is applied. These combinations allow the HM6420 to grind massive quantities of material efficiently and effectively at one time.
A proportional feed system is standard and regulates the feed system from 82 to 132 ft/min (25 to 40 m/min). The HM6420 has one of the fastest feed rates on the market allowing it to quickly process material. The proportional feed system allows operators to adjust the feed based on material being processed ensuring maximum output and grinder efficiency, all while achieving a higher quality end-product.
Three screens are located on the top side of the HM6420 mill. A variety of screen sizes are available up to 7 in (18 cm) to produce various end-product sizes. The top feed wheel moves upward, and a removable screen cradle allows for quick screen set-up changes. All work for screen changing is performed outside of the machine.
An impact detection system is standard and designed to limit damage if a contaminant is struck inside the grinding chamber. Once an impact event is detected, the grinder will idle down, open the gate, disengage the clutch, and reverse the feed.
The addition of the HM6420 expands the already diverse line of Bandit horizontal grinders available. Customers can choose from various mill configurations that will “CUT IT,” “CHIP IT,” OR “HAMMER IT.” Source
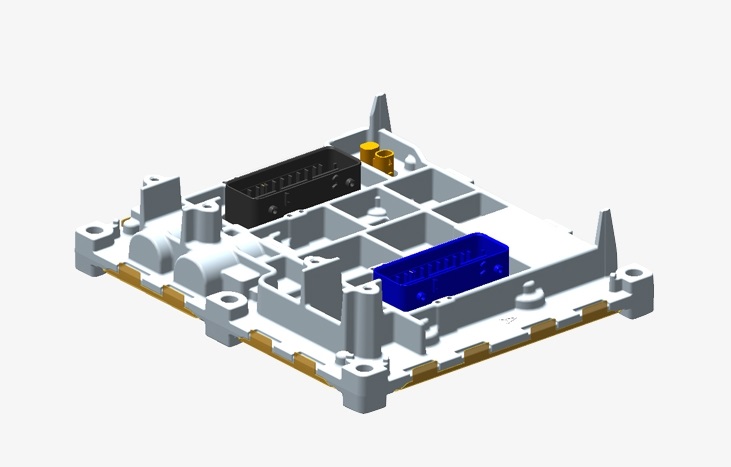
The ECM is the brain of the engine, optimizing performance and efficiency.
Cummins explains the functions of the ECM and how it optimizes engine performance, reliability and efficiency.
The ECM is the heart of a modern engine. The ECM collects data from sensors distributed across the engine and uses this to analyse performance in real time. This data provides the ECM with key insights and enables adjustments for fuel consumption, ignition timing, achieving maximum engine efficiency, improving fuel economy and overall performance.
Beyond this, the ECM is crucial for maintenance and troubleshooting. When the engine encounters issues, the ECM quickly identifies and records the problem using specific diagnostic codes. These codes, accessible with professional tools, help to identify problems quickly and accurately, preventing further damage and expensive downtime.
- Manages engine performance: A crucial job of an Electronic Control Module is to monitor and adjust engine operations. It fine-tunes the fuel injection system, ignition timing, and many other engine functions. By constantly analysing data from different sensors, it improves performance and efficiency. For instance, while driving uphill, a truck's engine experiences a higher load and lower speed. The ECM detecting these changes through sensors, adjusts the fuel injection and ignition timing accordingly. This optimization ensures the engine provides the necessary power efficiently, helping the truck to climb smoothly without overworking the engine or wasting fuel.
- Monitors and helps control emissions: Electronic Control Modules play a vital role in emissions reduction and managing engine pollutants by constantly monitoring the engine's exhaust through sensors. If the ECM detects an increase in pollutant levels, it adjusts the engine's operations, such as the fuel-air mixture and combustion timing, to reduce emissions. ECM also constantly monitors temperatures, pressure and chemical compositions of the engine exhaust gas through sensors. It analyzes this information and takes action to operate the exhaust gas aftertreatment systems like Particulate Filter System (PFS) and Selective Catalytic Reductant (SCR) at optimal conditions.
- Helps with transmission control: The ECM is central to efficient transmission operations. It monitors factors like vehicle speed, engine load and driver input to optimally time the gear shifts. For example, when a truck is hauling a heavy load uphill, the ECM can detect the need for more torque to navigate the incline efficiently and can delay the shifting of gears in the transmission. This optimization ensures the engine delivers sufficient power while maintaining optimal fuel efficiency.
- Monitors the braking system: Road safety is critical, and the ECM helps by monitoring and managing the anti-lock braking system and other brake-related functions. If it detects a wheel is about to lock up, the ECM modulates the brake pressure to that wheel, preventing skidding and maintaining vehicle control. This ensures optimal brake control, enhancing safety for all driving conditions.
- Monitors the safety systems: The ECM also monitors various safety systems in the vehicle. It manages airbags, seatbelt pre-tensioners, and other safety features. In a collision, for example, it determines when to deploy airbags and tighten seatbelts to minimize possible injuries.
- Helps control vehicle accessories: The ECM controls vehicle accessories, from power windows and climate control to entertainment systems. It ensures these systems function well and seamlessly interact with other vehicle systems. For example, it might modify the climate control based on engine temperature and cabin conditions for increased driver comfort. Source
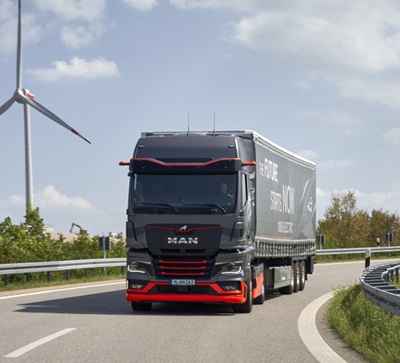
The first limited edition models of the new MAN eTruck for 2024 are already sold out.
A total of 700 orders and order requests have been received, the majority of which are for large-scale production, which will start at the MAN plant in Munich in 2025. Trucks with diesel and battery-electric drives will then be manufactured on the same assembly line, which will allow the greatest possible flexibility depending on the demand situation. The plan is for half of all new MAN trucks delivered in Europe to be electrically powered by 2030.
The new MAN eTGX and MAN eTGS are characterized by a high degree of variability in battery configuration with a choice of three to six battery packs. This means that the optimum vehicle configuration in terms of range, payload and charging time can be selected for every application characteristic - from supermarket deliveries in the city centre, to regional building materials supply, to long-distance transport in production logistics. With six battery packs, two of which are installed under the cab and up to four more on the side of the vehicle frame, the eTGX and eTGS offer up to 480 kWh (of usable battery capacity for daily ranges of up to 800 km (500 mi). In addition to the CCS standard with up to 375 kW (510 hp), MAN has been offering the even more powerful megawatt charging standard (MCS) for fast intermediate charging during breaks from driving, which will initially enable 750 kW (1,020 hp) and, in a later expansion stage, even more than one megawatt of charging power.
Together with payload and body-friendly positioning of the drive unit, the modular battery concept of the MAN eTGX and MAN eTGS also offers a high degree of variability for a wide range of bodies, as well as very short wheelbases from 3.75 m (12.3 ft), which allows the tractor unit to be combined with all common semi-trailer variants within the permissible overall length specifications. This also makes volume variants for three-meter internal loading heights possible, which are often in demand in production logistics.
Even before purchasing a new eTruck, MAN supports customers with its 360-degree eMobility Consulting. In addition to advice on the most suitable vehicle, this also includes consideration of customer-specific operating conditions, including cost optimization, route analysis, fleet optimization and, building on this, the necessary advice on charging infrastructure. Additional support is provided by digital tools such as the new MAN eReadyCheck, which customers can use to check how their delivery routes can be driven purely electrically, or the MAN eManager, which fleet managers can use to keep an eye on the important information on the charging status of all trucks in the fleet at all times. MAN also has its own charging infrastructure offering for customers in its portfolio through partnerships with charging infrastructure manufacturers such as ABB, Heliox and SBRS. The service page offers service contracts and financing solutions for the new MAN eTrucks that are specially tailored to electromobility. Source
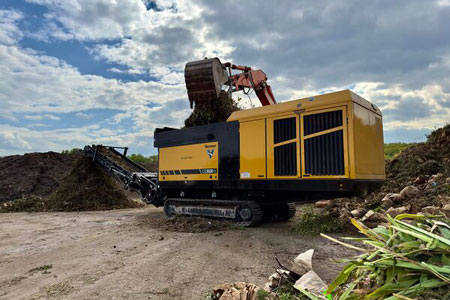
It can process a broader range of materials with this latest recycling innovation by Vermeer.
Vermeer unveils the LS3600TX low speed shredder, its latest innovation for the recycling industry. This single-shaft shredder incorporates exclusive innovations that efficiently process contaminated waste streams and help safeguard critical machine components. The Vermeer LS3600TX is specifically designed to excel at processing various materials, including light construction and demolition waste, wood waste with contaminants, and municipal solid waste. It is well-suited for waste facilities and land clearing operations, as well as compost, mulch and biofuel producers.
Vermeer has designed the LS3600TX shredder with a strong focus on maintenance and accessibility. The engine bay of the LS3600TX prioritizes ease of maintenance and serviceability, featuring large access doors, multiple ladder points and a spacious service platform. This thoughtful design allows for quick and efficient maintenance. Additionally, the LS3600TX is equipped with a hydraulically operated access system that provides full exposure to the rotor, comb, and belly conveyor, further streamlining maintenance procedures. Also, the belly conveyor can be easily removed without detaching the discharge conveyor, minimizing the invasiveness of service operations.
The LS3600TX shredder has a powerful 456-hp (340 kW) CAT Tier 4 Final/Stage V engine. It operates at a sound level of only 111.9 db. The shredder features a tracked undercarriage, which enables operators to reposition and manoeuvre it around a jobsite. It also comes with a full-function remote control, allowing operators to adjust the feed, access machine data, and diagnose fault codes from the comfort of the feed loader's cab or a safe distance from the shredder.
The LS3600TX is equipped with a 10 ft (3 m) long rotor featuring wear-resistant plates for enhanced durability and dual-bolt tips to help maintain clamp load. It utilizes individual bolt-in comb teeth, each with two usable edges, which extends their lifespan. The shredder is built with a fully mechanical driveline designed to optimize horsepower transfer to the rotor. To safeguard the driveline system against unshreddable objects, the LS3600TX includes a reversible mechanical transmission with an external torque limiter that will automatically disengage the drive when maximum torque is reached.
Vermeer offers an optional cross band magnet for the LS3600TX to further enhance its capabilities. This magnet effectively reduces steel contaminants from the end material, minimizing contamination in the final product. Source
Tigercat Provides Increased Spare Parts Responsiveness
Tigercat has opened a west coast parts warehouse facility to improve responsiveness, decrease lead times and extend spare parts operational hours into Pacific time zone. Tigercat Industries is pleased to announce that it has opened a new 3 250 square metre (35,000 square foot) parts warehousing and distribution facility in Kelso, Washington with a current stock of inventory valued at $3.5 million. Source
Janne Loponen has been appointed Managing Director of Ponsse Latin America Ltda.
Managing Director of Ponsse Latin America Ltda, Ponsse’s subsidiary in Brazil, is changing. Janne Loponen has been appointed as new Managing Director of Ponsse Latin America Ltda. starting from February 1, 2024. Janne Loponen's location will be in Brazil, and he will report to Marko Mattila, Chief Sales, Service & Marketing Officer of the Ponsse Group. Former Managing Director of Ponsse Latin America Ltda, Fernando Campos Passos, has served as the Managing Director since 2018. Source
Read MoreTo see the full list of international logging, roading and trucking conferences and expo’s, please click the “Events” tab at the top of the page.
Read More