This will expand rural connectivity through satellite communications.
Utilizing the industry-leading Starlink network, this solution will allow machine owners facing rural connectivity challenges to fully leverage precision technologies. This partnership, an industry first, will enable John Deere customers to be more productive, profitable, and sustainable in their operations as they continue to provide food, fuel, and fibre for their communities and a growing global population. This requires executing incredibly precise production steps while coordinating between machines and managing machine performance. Each of these areas are enhanced through connectivity, making the entyre operation more efficient, effective, and profitable.
The SATCOM solution will connect both new and existing machines through satellite internet service and ruggedized satellite terminals. This will fully enable technologies such as autonomy, real-time data sharing, remote diagnostics, enhanced self-repair solutions, and machine-to-machine communication, all of which help machine owners work more efficiently while minimizing downtime.
John Deere is bringing satellite communications service to rural areas at scale so those with cellular coverage challenges can maximize the value of connectivity to their operations. The SATCOM solution unlocks the John Deere tech stack so every machine owner can fully utilize their current precision agriculture technology in addition to the new innovative solutions Deere will deploy in the future.
John Deere’s SATCOM solution will leverage SpaceX’s Starlink satellite internet constellation. To activate this solution, John Deere dealers will install a ruggedized Starlink terminal on compatible machines, along with a 4G LTE JDLink modem to connect the machine to the John Deere Operations Center. The SATCOM solution will initially be available through a limited release in the United States and Brazil starting in the second half of 2024. Source
Read More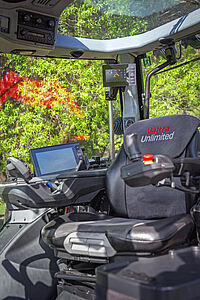
The control system has undergone extensive testing and is now ready for sale.
The control system is Kesla’s own work. It features intelligent loader control and end damping. It is available for the KESLA 320 series loaders, i.e. the 325T and 326T models. Kesla has also combined remote contact with proC i intelligent loader control. Remote contact provides security for the user, as it enables direct technical support from the factory. With remote access, the factory technical support can see the same view as the operator. Remote access can be used to support the customer in, for example, problem-solving or adjustments.
The development of the KESLA proC i intelligent loader control was started six years ago. Having gained popularity among customers, KESLA proC control provided a good basis for the construction of the new control system. The new intelligent loader control has been tested by customers for three years. It has been used in a variety of conditions, from heat to sleet and extreme cold. The applications have included forestry work, contracting work and heavy agricultural use.
KESLA proC i intelligent loader control further improves the usability and ergonomics of the loader The intelligent loader control specifically controls the tip of the crane, not the main boom, outer boom or extender separately. This makes it easier to learn the control method and is also reflected in productivity. In a study commissioned by Metsäteho, the productivity of intelligent loader control compared to electric two-lever control was over 24% higher.
The end damping provided with the intelligent loader control makes the operation smooth and soft, since there are no jolts caused by extreme movements. It is possible to turn off both the intelligent loader control and the end damping if this makes more sense for the work. The control system is operated using a large touch screen with clear menus. It is possible to store 10 different sets of settings in the KESLA proC i system. Examples of typical settings include separate settings for handling brushwood, wood or bales, or for driving with cold oil and warm oil.
Ergonomics have been taken into account in the equipment – for example, in the new armrest. The armrest is easily adjustable to suit different-sized operators. The joystick base is shaped to keep the grip relaxed. The stand-by and on/off buttons frequently used in the control system have been moved to the armrest, minimising the need for hand movements.
Kesla has also published material that makes it easier to explore the new features independently at any time, using a smartphone, for example. For more information about the material, please contact your nearest dealer. Official sales of the KESLA proC i intelligent loader control will start at the beginning of January 2024, and it will be available for the KESLA 325T and 326T loaders at first. Source
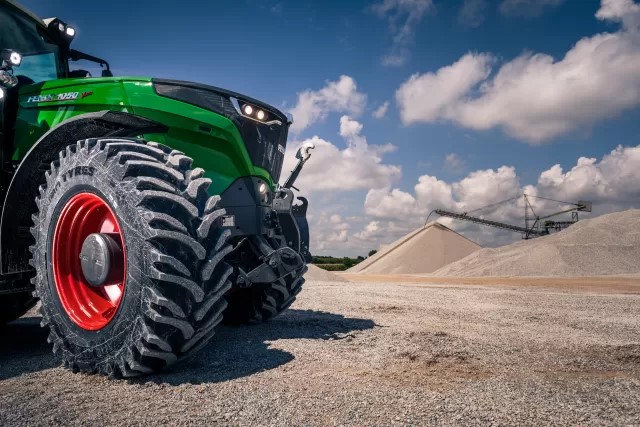
This provides more choices for forestry applications and more load-carrying capacity.
Powerful tractors and challenging terrains need tyres to match. The Nokian Tyres Tractor King tyre family is designed for forestry, earthmoving and road construction jobs. A wide range of available sizes ensures the best match with the machine and the job at hand. This is why the Nokian Tyres Tractor King family is expanded with three new sizes, 600/65R28 for front axle as well as 710/70R38 and 800/70R38 for rear axle.
When the Nokian Tyres Tractor King tyre family was released in 2018, it was especially welcomed by the people doing heavy tractor work in harsh terrains. Its all-new tread pattern with more tractive edges provides excellent grip while the fortified carcass and special forestry compound add reliability. With the three new sizes, even more tractors can benefit from these winning properties.
Big machinery, heavy loads and powerful work attachments call for high load-bearing capacity from a tyre. The biggest of the new rear tyre options, 800/70R38, raises the load-bearing capacity to a new level. The new tyre boasts the highest load carrying capacity in the Nokian Tyres Tractor King product family with a Load Index (LI) of 183. The wider rear tyres offer increased traction and durability, particularly beneficial for high horsepower pulling tasks. Source
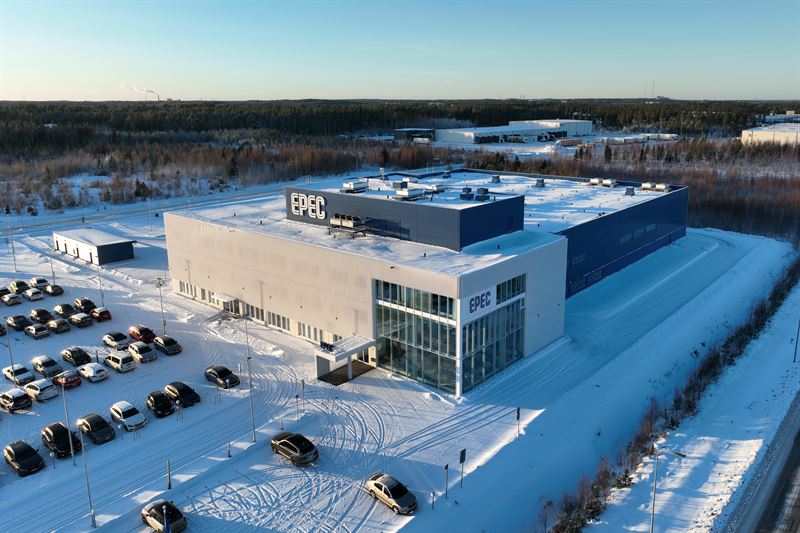
The factory produces, for example, control units, displays, sensors, power distribution units and telematics units.
Epec Oy’s new smart electronics factory aims for carbon neutrality and uses responsible manufacturing processes. It will provide these products for the needs of various mobile work machines and commercial vehicles. In addition, Epec designs and develops systems and software for machine manufacturer needs.
The state-of-the-art factory is a significant investment for Epec and is in line with the company’s growth goals and responsibility commitments. The technology transformation is accelerating digitisation and electrification in mobile machinery and vehicles. Epec’s products play a key role in enabling the development of more responsible mobile machinery and commercial vehicles. They offer solutions for integrating electronic systems and control systems, optimise the efficiency of machines and promote productivity, while reducing emissions. The products enable the path towards zero-emission work machines. The factory offers Epec a significant opportunity for their growth and for their customers’ continued success.
The rapid development of technology and increasing sustainability demands provide Epec with an excellent opportunity to contribute to technology aimed at zero emissions. Ponsse’s vision is to be the preferred partner in responsible forestry, obliging Epec to conduct bold development work from an environmental perspective as well. Ponsse aims for more climate- and environmentally friendly solutions in product and service development. The factory in Seinäjoki is one concrete step towards this goal, both in terms of product offering and daily operations. Epec supports Ponsse’s technological development and plays a part in enabling future growth.
ESF1 aims for carbon neutrality during operation and uses sustainable manufacturing processes. The factory, covering an area of 8,500 m2, incorporates energy-efficient solutions, including electricity generation from more than 600 solar panels (210 MWh/year) and a geothermal system. Heat recovery is achieved through efficient needle heat exchangers, and the need for cooling energy is significantly reduced by an aluminium grille in the office wall. All electricity and heating energy is sourced from renewable sources.
The ESF1 project progressed according to the planned schedule. Epec moved its headquarters and production to new premises at the end of 2023. The expanded and modern production facilities enable the optimisation of manufacturing processes and improvement in material flow management. The opening of the factory is 18 January 2024. Source
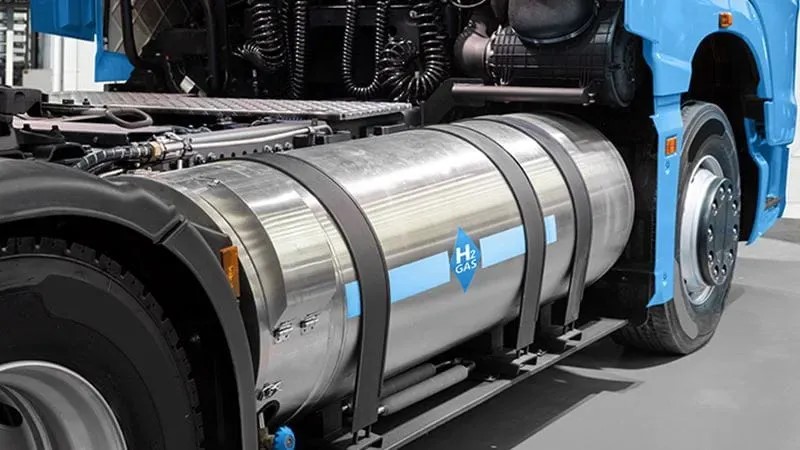
Trelleborg explains why is it only now being considered as a fundamental part of a more sustainable world.
Currently, around 51% of the hydrogen that is used in the global economy goes to refineries, and 43% as an input for ammonia synthesis, primarily in the production of fertilizers. The most common process for producing hydrogen is steam methane reforming (SMR). This is fossil fuel-based and consumes around 6% of the world’s natural gas and 2% of its coal.
Hydrogen is rarely available in its pure form on Earth, so it requires extraction from compounds in which it is present. Any compound with ‘H’ in its chemical formula has hydrogen as one of its constituents, such as hydrocarbons, methane (CH4) and water (H2O). In fact, hydrogen makes up about 75% of the universe.
Although hydrogen is colourless, its different types are defined through a palette of colours that range from black (which comes from coal), pink (from nuclear), and turquoise (produced by pyrolysis of methane) to blue hydrogen (produced from natural gas with carbon capture technology), and what is currently the most common form, grey (extracted from coal gas). It is the source material and the production method that determine the extent to which the type of hydrogen is environmentally friendly.
So, if hydrogen derives from fossil fuels, why is it being seen as such an important part of a sustainable future? The holy grail is completely carbon-neutral or ‘green’ hydrogen.
Green hydrogen is made by passing water through an electrolysis cell powered by electricity generated from a renewable source, such as wind, solar or hydropower. The electricity divides hydrogen from oxygen, creating hydrogen gas at one electrode and oxygen at the other. The potential of green hydrogen in the sustainable energy mix lies in the fact that it can be burned in much the same way as natural gas is burned; and it can be run through a fuel cell, where it behaves in a similar way to a battery.
Though it has many uses, what has limited hydrogen’s applications so far is its energy-intensive extraction process, which sometimes uses more energy than the energy that is produced. Fossil fuel-based grey hydrogen is relatively cheap; up until now, the greener the hydrogen, the more costly it is to produce. However, this is changing as the production of green hydrogen becomes a more viable option and to some extent, an essential one.
Fossil fuels are becoming more and more expensive and increasingly unacceptable due to their impact on climate change. They are also being used as a bargaining tool in geopolitical conflicts, so the push for a reduction in dependence on these fuels is becoming more urgent by the day. There is also pressure on governments, global bodies, and industry to slash greenhouse gases to meet the zero emissions targets they have set. Realistically, these are only achievable through substantial new solutions, such as green hydrogen.
In addition, initiatives like the United Nations Green Catapult, the U.S. Department of Energy Hydrogen Program, China’s longterm hydrogen plan and legislative proposals from the European Commission are all leading to hydrogen extraction becoming prioritized, more efficient, and thus more cost-effective. Meanwhile, the falling costs of the production of solar and wind energy are significantly lowering the total costs of green hydrogen manufacturing.
Manufacturers will definitely be ‘greening’ the critical chemical processing applications that currently dominate hydrogen use. There will be a shift from grey to green hydrogen for fertilizer production, for instance. What about hydrogen cars? In fact, the first four-wheel vehicle powered by hydrogen and oxygen was conceived as long ago as 1807. Even back in the 1970s and 1980s, many saw hydrogen as the answer to the quest for green automobiles. Jack Nicholson, the Hollywood actor, wowed onlookers in 1978 with a car fueled by what today we would call ‘green hydrogen’.
In the intervening period, battery technology has improved dramatically so that battery electric vehicles (BEVs) now rival traditional powertrains in terms of range — the distance travelled on one charge at an electric point or after filling up at a gas station. Most experts agree that batteries rather than hydrogen fuel cells have won the race for sustainable car technology, although Honda became one of the first original equipment manufacturers (OEMs) to offer a hydrogen fuel-cell electric vehicle (FCEV) to retail customers, in 2008.
For other types of vehicles though, batteries have their limitations and hydrogen could be a better option. According to SAE International, OEMs and global suppliers are looking to hydrogen propulsion as a solution for decarbonizing heavy transport. However, hydrogen has been long the poor relation of the BEV, and it was only in 2020 that Hyundai began producing its Xcient hydrogen-fueled truck.
It’s therefore unsurprising that, until now there has been limited uptake and acceptance of hydrogen vehicles. According to Information Trends, only 56,000 hydrogenpowered vehicles are on the world’s roads in 2023, and very few of those are commercial or heavy-duty trucks. However, current breakthroughs in hydrogen technology could reduce fleet emissions while still providing reliable service with similar uptime to modern diesel trucks.
OEMs are focusing on developing the technology for difficult-to-electrify applications: for trucks that travel 400 kilometers or more daily and are being used in areas where the ambient air quality is low, or which have high duty-cycle applications (continuously in use for much of the day).
As a first step, most OEMs are concentrating on hydrogen-powered engines that utilize current technology and chassis. However, FCEVs could eventually provide a longterm solution to decarbonizing long haulage trucking. Hydrogen fuel cells offer great promise for heavyduty trucks in applications requiring a higher density of energy, fast refueling and additional range.
Beyond this there are also pressures on the shipping industry to lower its carbon footprint. Ships currently emit 3% of the world’s greenhouse gases. Several projects are underway, testing how hydrogen and other fuels made from it, such as ammonia and methanol, could power a low-carbon maritime industry.
Another area of interest is long-distance rail, and here technology is already a reality. Alstom’s Coradia iLint™ is the world’s first passenger train powered by a hydrogen fuel cell; in September 2022 it reached a new world record distance of 1,175 kilometers on a single filling.
The most significant sustainable application for hydrogen is its potential role in the stabilization of the electricity grid. This is because hydrogen is produced from electricity, is storable and has the capability to be converted back to electricity.
Renewable energy is inherently intermittent as it is dependent on when the sun shines or the wind blows. Although the efficiency of solar panels and turbines keeps increasing, there is a need for an alternative source when there is no energy generated. Currently, coal gas is the back-up and that is unsustainable due to its climate impact.
The panacea is filling that gap with green hydrogen. When there is peak production for wind and solar, turbines and panels produce more energy than is needed for the electricity grids they supply, so they shut down. That results in a loss of up to 20% of renewable energy’s capacity.
Major investment now focuses on integrating hydrogen with renewables. Instead of switching off panels and turbines at peak production times, the excess electricity would divert to produce green hydrogen, which goes into storage facilities. When the grid needs energy, the hydrogen would be converted back to electricity. Source
Bandit Industries announces the appointment of new CEO and President
Former CEO, Jerry Morey, announced the appointment of Craig Davis as the CEO and President of Bandit Industries on Thursday. Craig joined the Bandit team in 2018 as the sales director. Craig was also a part of the Bandit management board and oversaw the marketing and parts managers. Prior to joining Bandit, Craig was employed at Power Solutions International and held various roles ranging from parts and sales to executive VP of sales. While working at PSI, Craig supplied Bandit engines for over twenty years, and was able to form a variety of relationships with Bandit employees, customers, and dealers. Source
Ponsse Studio presents: Manager 2.0
Interested people are welcome to attend the Ponsse Studio event on 31 January. At the event, Ponsse will present PONSSE Manager 2.0, a modern new digitalisation platform for forestry. Ponsse Manager 2.0 is a solution that gathers Ponsse’s entire digital offering into a single package. The user only needs to sign up once, and all the digital services that are required to improve operational efficiency and productivity are at the user’s disposal. The English language event will take place on 31 January 2024 at 10:00 / 10 a.m. and 19:00 / 7 p.m. (EET). Source
Read MoreTo see the full list of international logging, roading and trucking conferences and expo’s, please click the “Events” tab at the top of the page.
Read More