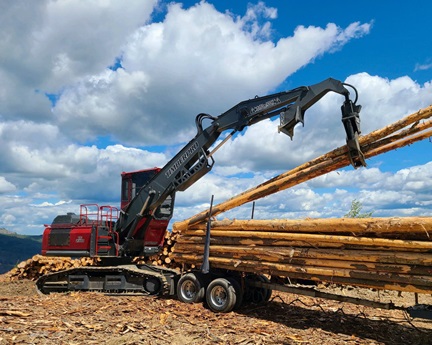
The new machine was built from the ground up based on customer and distributor feedback
Komatsu is pleased to introduce its newest log loader, the TimberPro TN230D. The 197 hp (145 kW) TN230D offers a 36 ft (11 m) reach. It also features Power Max, which temporarily increases engine horsepower and hydraulic flow to support tough forestry tasks. The machine is built with proven, high-quality Komatsu components and its hydraulic system, powertrain, control valve and interior components are designed and manufactured in-house to help ensure performance and quality control.
The TN230D is the first machine in its class segment to feature dual service platforms with electrically actuated platforms on the left and right sides, offering improved access for service and cleaning. New benefits include easy access via a large, rear entry cab with service walkways and safety railings, premium heated and cooled seats with adjustable armrests, an elevated cabin with large windows and a front view camera to improve visibility, LED lights and a large overhead skylight. Source
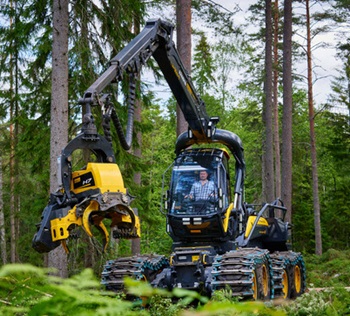
Ponsse reflects on their 2024 financial results.
Ponsse CEO, Juho Nummela provides feedback on Ponsse’s 2024 results and operating conditions. Modest financial development characterised 2024. Financial uncertainties also extended to Ponsse, and the market situation remained challenging throughout the year. Order intake was fairly weak during the first part of the year but improved in the latter half, driven by the busy exhibition season. In the last quarter of the year, the order flow was reasonable in relation to the situation,
Difficulties in the key drivers of Ponsse’s – the sawmill and chemical forest industries – were reflected in forest machine sales. Ponsse’s customers’ investment decisions slowed down. While inflation calmed down, the geopolitical situation caused significant uncertainties in the markets. Interest rates remained fairly high in some market areas. At the same time, the decreased purchasing power affected private consumption, and construction volumes were very modest in Europe in particular. Demand for wood was still reasonably high, and in general, Ponsse customers were kept busy throughout the year. Ponsse’s maintenance services performed well in the uncertain situation, providing customers with excellent services globally.
At Ponsse, 2024 was a year of major changes, as the company’s operating model underwent significant updates. A shift to a global organisational structure and reporting lines is a key part of the new operating model, which was adopted on 1 June 2024. This change supports even better customer service, strengthens competitiveness, increases cost effectiveness, and improves operational efficiency through shared practices. The new operating model enables a customer-driven organisation, focused on sales and maintenance services. This change is important for Ponsse’s long-term development. The aim was to plan the operating model respecting the company’s values and culture, and its implementation will continue.
Ponsse’s factory in Vieremä performed well in 2024. There were no problems with the availability of parts, and the factory stayed on schedule throughout the year. As the challenging market situation weakened the company’s order books and the order books were spread over a longer period, the factory’s operations had to be adjusted at the end of the year. However, considering the situation, the number of machines manufactured during the year was relatively good, driven by successful sales during the second half.
Economic uncertainty is expected to continue and affect demand for forest machinery. The current operating environment is reflected by trade policy, the geopolitical situation and economic uncertainty in the countries where we operate. Ponsse will focus on strong customer service and improve their efficiency by introducing consistent and cost-effective practices in line with their new operating model. Their investments will continue, with a deliberate focus on new products and digital services, the service network, the Vieremä factory and sustainability. Source
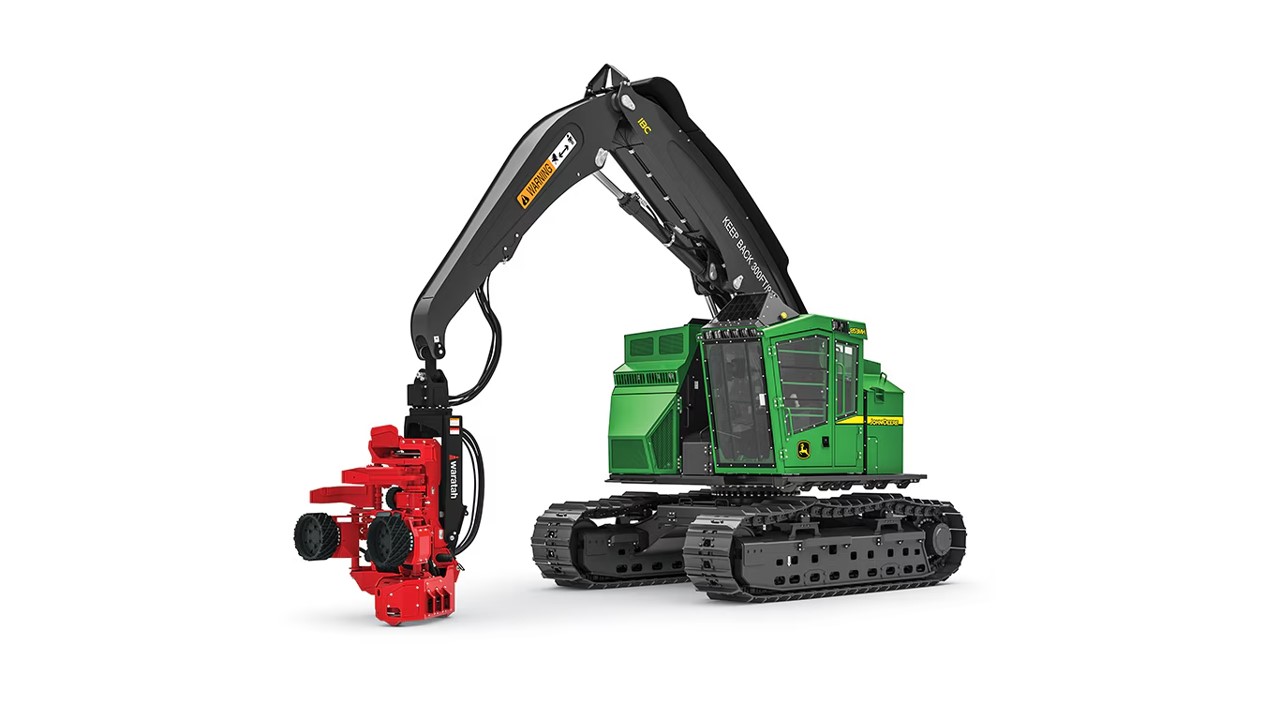
These updates allow users to access comprehensive jobsite data and machine health information
John Deere is enhancing the digital customer experience with new features in John Deere Operations Center. The empowers customers to make real-time decisions that drive profitability. John Deere is committed to investing in the digital customer experience, building out existing tools like Operations Center and Equipment Mobile with new features and enhancements.
Using feedback from John Deere customers, the added features and enhancements directly address challenges industry professionals face every day. The added information and enhancements include:
- Custom Alerts: Customers can be alerted when idle time, speed or fuel levels exceed limits. These alerts enable proactive planning, ensuring fuel usage and maximizing job site productivity.
- Jobsites with Summary Cards: Monitors jobsites in near real-time with Jobsite Manager and Summary Cards. Customers can easily create, track, and optimize jobsites to improve productivity and efficiency. Paired with Summary Cards, customers can monitor progress, fuel consumption, and machine locations, driving profitability and enhancing operational performance. Jobsites can also be automatically created when the automatic toggle is on.
- Machine Analyzer Updates: Provides default customer reports to track operator use of grade control and its impact on productivity as well as payload weighing.
- Remote Display Access: Facilitates remote monitoring and operator support, allowing control of the display and adjustment of settings to enhance productivity and maximize machine uptime.
Regarding maintenance, there are a variety of new solutions available to customers to help keep the jobsite running smoothly. The Maintenance Plan Auto Assignment within Equipment Mobile empowers dealers to proactively plan and provide maintenance solutions with seamless communication to ensure customers' equipment is readily available. With this feature, customers can add factory maintenance plans to their machines, see specific parts needed for service, streamline maintenance set up and empower customers to manage their machines efficiently.
The John Deere Equipment Mobile app helps customers manage their equipment with less effort. With this app, customers can look up information in the Operator's Manual, quickly find parts and maintenance schedules, track past or upcoming service, and more. Source
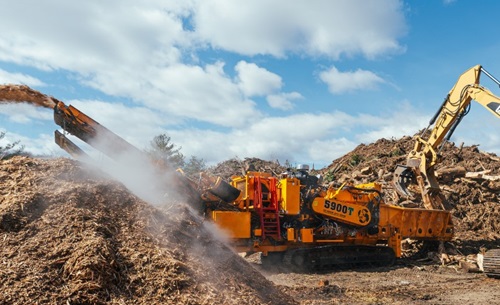
This is the first grinder in the 5900 series.
This machine blends the best of both worlds- incorporating proven features from the CBI 6800 and 5800 grinders while introducing innovative upgrades for superior material processing. With a 60 in (152 cm) wide infeed rotor, the 5900T optimizes material flow, handling wider material and reducing the need for pre-processing. Its robust 755 hp (555 kW) engine, paired with a hydraulic clutch, delivers smooth, powerful performance with precise control, making it a good choice for high-production environments.
Designed with mobility and transport efficiency in mind, the 5900T has legal transport width and a redesigned dolly system, ensuring seamless movement between job sites. Built for durability and ease of maintenance, this next-generation grinder features quick air filter removal and convenient engine access, minimizing downtime and maximizing productivity.
A key enhancement to the 5900T is its updated discharge system, engineered with multiple wear plates and a material-ejecting pulley to enhance durability and overall performance. The grinder as a Metal Detection System (MDS) which provides essential protection from tramp metal, preventing damage to vital components. The 60 in (152 cm) wide infeed and rotor improves material handling and reduces the need for pre-processing. It has belt hold down rollers which extends skirt rubber life for increased efficiency and longevity. Source
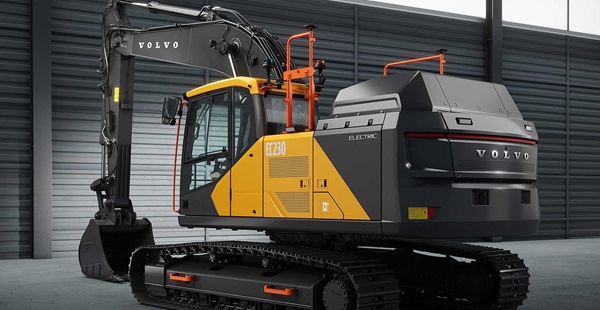
The advanced technology gives customers double the typical operating hours of its predecessor
Now capable of a full day of operation on a single charge, the upgraded EC230 Electric signals a groundbreaking and sustainable evolution in heavy construction. Furthermore, the battery-electric excavator combines state-of-the-art features and an updated design with enhanced efficiency, greater safety and superior operator experience.
The launch of the updated EC230 Electric marks a significant milestone in the transition towards sustainable construction solutions, offering the same robust – and now long lasting – performance as its diesel counterpart but with the added benefits of zero exhaust emissions, near silent operation, reduced vibration and instant torque.
The mid-size machine, which has already been proving its worth on jobsites around the world, re-enters the market as the ideal partner for medium to heavy-duty applications, such as building, demolition and industrial material handling.
Offering an extended runtime of 7 to 8 hours per charge – powered by its 600V lithium-ion battery with a capacity of 450 kWh – operators can now work a full day without interruption, making it ideal for noise-sensitive and environmentally restricted areas.
Moreover, a peak motor power of 160 kW (218 hp) ensures a performance equivalent to diesel excavators, while fast charging capabilities allow the battery to reach from 20% to 80% in just 1 hour with a 250-kW charger.
Hydraulic efficiency is also improved by 10% and – when matched with additional features such as Volvo Active Control, On-Board Weighing and Dig Assist 2D and 3D – the electric excavator offers good machine guidance and control. This not only provides more precise digging, shorter cycle times and reduced operator fatigue, but it sets a new standard for electric performance by maximising productivity while minimizing environmental impact.
Building on the success of its predecessor, the enhanced EC230 Electric inherits a suite of improvements found in Volvo’s new generation excavators. These include:
- An enhanced operator experience, thanks to a revamped cab environment with greater space, comfort and functionality,
- An intelligent electro-hydraulic system enabling smoother, more precise movements of the boom, bucket and other attachments, and
- Innovative safety features such as HD Volvo Smart View with People and Obstacle Classification providing operators with 360° visibility and deep-learning technology to detect potential hazards. Source
Tigercat announces changes to its district manager team and territories in the southern United States
Following the recent passing of Johnny Boyd, who served as a Tigercat district manager since 1996, Tigercat is pleased to announce the promotion of Nicholas Edwards to District Manager. Nick will continue to provide technical support to Tigercat dealers and customers until a new product support representative is brought onboard for the regions of Arkansas, Louisiana, Oklahoma, and Texas. Source
Nokian Tyres used on vehicles crossing Antarctica with the Transglobal Car Expedition team
The world’s first crossing of East to West Antarctica involved driving across the coldest area in the world, reaching altitudes up to 3650 meters. The team experienced both extreme clarity and zero visibility conditions, with snow varying from very soft to hard-packed. Source
Read MoreTo see the full list of international logging, roading and trucking conferences and expo’s, please click the “Events” tab at the top of the page.
Read More