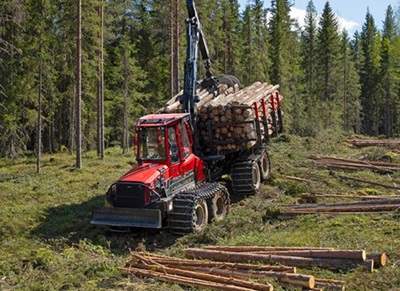
This makes the 895 an even more productive final felling forwarder.
The Komatsu 895 was introduced in 2013 and has undergone a number of productive upgrades during the years. There is an all-new, powerful crane option; the 205F. The Komatsu 895 has also been upgraded with a robust load space, including gate and bunks with telescopic function. In conjunction with this upgrade a new grapple model is presented, the G88H, as well as a new rotator that fits the larger crane.
With this upgrade, the focus is on a new, powerful crane and a load space with a telescopic full-width gate and telescopic bunks. The cooperation with customers has been a guide in this project and experiences from plantation forestry in South America as well as final felling in the Nordic countries, Australia and North America have contributed invaluable input in the development work.
The 205F is a brand new, powerful crane with a lifting torque of 205 kNm and a slewing torque of 51.9, kNm. It has been developed with a focus on increased productivity in final felling and plantation forestry. The crane has a robust, welded crane pillar which together with the inner boom and outer boom provides both good lifting capacity and lifting geometry. Choose between a reach of 7.5/8.5 m (24.6/27.9 ft) with single telescope or 10 m (32.8 ft) with double telescope. In connection with this, we also offer a brand new, larger grapple model, G88H, with tip-to-tip area 0.55 m2 (5.9 ft2). The new grapple also has a powerful new rotator, the GX.
The new load space consists of a robust, telescopic gate and new, hard-wearing bunks with telescopic widening function. The entyre gate is raised and lowered hydraulically and the foldable wideners can be locked in the retracted or extended position. There is also an option to make the gate movable along the rear frame direction.
The new bunks have a telescopic widening function and can also be equipped with hydraulic height-adjustable stakes. This increases the productivity of loading and unloading by reducing the height that the timber needs to be lifted over the stakes – which also contributes to reduced fuel consumption.
The machine’s frame system, including articulating frame and bearings, has been designed to handle the increased crane capacity and the new load space. The more robust frame also gives the machine better durability in challenging environments. A longer rear frame option is also offered to suit plantation forestry, mainly in South America. It is adapted for the log length of 7.2 meters (23.6 ft).
Another new feature is that the hydraulic system is equipped with a hydraulic pump with electric control. This provides benefits such as more even pressure levels and improved efficiency. The hydraulic tank has also been further developed and equipped with a practical new single filter that simplifies maintenance and service. Source
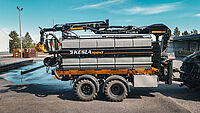
Kesla Oyj is launching a new multi-purpose forest trailer.
A tractor contractor's business rarely comes from a single source and the jobs depend on the season. Kesla’s new solution opens new opportunities in tractor contracting as the HydraX trailer adapts to the seasonal work needs. The main applications are wildland fire operations and wet works in built surroundings; the higher up and further the water needs are the better the HydraX is suited to the job.
Traditionally the forest fires have been extinguished using water but due to climate change fires are getting extreme and plain water is not always enough to stop the fire. Furthermore, in wildland fires the rural conditions complicate the firefighting as the fires are typically located off-road. Creating a firestop is a new method for fighting wildland fires; the burning hot fire is not fought with water, but instead a fire-extinguishing agent is used to create a so called firestop to a pre-designed location where fire is stopped from spreading.
Finnish companies PPO-Elektroniikka and Kiilto Oy have combined their expertise and developed a forest fire-extinguishing agent ForExt for which KESLA HydraX™ is especially designed for. Powerful jet stream can wet the ground in over 50m (160 ft) reach or trees even 30 to 40m (100 to 130 ft) high. In addition, a grapple can be used to open fire nests and simultaneously shoot fire-extinguishing agent to a minor fire. An environmentally friendly 1:100 water-ForExt admixture forms a kind of a film on top of the biomass which then prevents ignition and re-ignition. ForExt storage and dosing are integrated to the HydraX systems which automatically forms the correct mix-ratio.
Wildland fire fighting is always a game of logistics against time and everchanging conditions. The HydraX uses natural water sources, and no time is wasted in water logistics. The unit can operate in water supply logistics feeding the fire brigade’s tank trucks or in a small forest fire the unit can be driven to the middle of the forest and be used as effective front-line fire fighting unit carrying over 10 000l of water to a difficult off-road location. In large scale logging sites or plantations, the HydraX can operate as a first-hand fire extinguishing unit, and it allows also the daily machinery washing works on-site to minimize fire risks.
The HydraX is also an efficient solution for any mobile wet works e.g. infrastructure washing, dust control, wetting works and fire security. Applications can range from washing road signs, bridge railings, tunnels, industrial yards to washing large storage halls inside out. In the forest industry the unit can be used to wet the round wood piles or woodchip stockpiles during hot summer season, or it can act as mobile fire security unit securing industrial hot works. In built surroundings the water filling can be done for example at a port, from a rain water reservoir or from a pressurized fire post.
The HydraX is available in two specifications. The basic version requires manual moving of suction head and suction hoses and is equipped with a 50m (160 ft) hose reel with an ergonomic manual nozzle. Fully equipped HydraX comes with a drawbar mounted Kesla 325T loader with a nozzle on the boom, suction head and hoses are moved using the loader and most importantly rear part of the unit is equipped with a powerful cabin controlled water monitor and hydraulically adjustable nozzle for shooting the water or water and ForExt admixture to maximum reach. Source
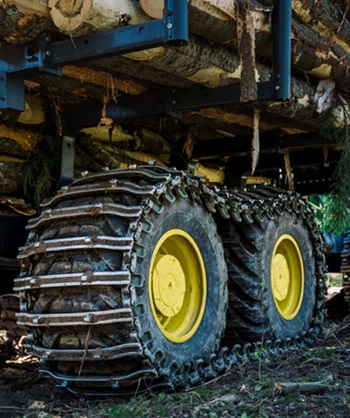
Nokian Tyres is setting new standards in the CTL segment with a new size for the Forest King F2.
The new tyre size for the Forest King F2 tyre family meets the increasing demands of Cut to Length (CTL) forestry machines, particularly the larger, more powerful forwarders and harvesters now being deployed in the industry. Featuring a protective tread design with strong shoulders, it provides excellent functionality on tracks and chains, with a strong diagonal structure and steel fortification ensuring excellent puncture protection.
The introduction of the new 30.5” tyre size is an important advancement for the forestry industry. As the demand for more productive equipment grows, Nokian Tyres is at the forefront of innovation, providing solutions that meet the evolving needs of the market. The larger air volume of the new Forest King F2 tyre size enables a step forward in load capacity, while the increased wheel diameter improves tyre-wheel contact area, resulting in increased tolerance against rim slip. The design of the tyre, with its strong shoulders and protective tread, ensures excellent performance with tracks in terms of grip and support to track paws.
To fully utilize the performance upgrade available with the new tyre, Nokian Tyres makes it available as a complete wheel with a matching heavy-duty wheel (size AG26.00x30.5”) and inner tube (size 780/55-30.5”). Working as a perfect match, the complete wheel complements the tyre properties for the best possible forestry performance.
The new 30.5” size for the Nokian Tyres Forest King F2 tyre is available now, allowing forestry professionals to immediately benefit from its enhanced performance and capabilities. Nokian Tyres Forest King F2 in size 30.5” makes its first appearance at FinnMetko trade fair held in Jämsä, Finland. Source
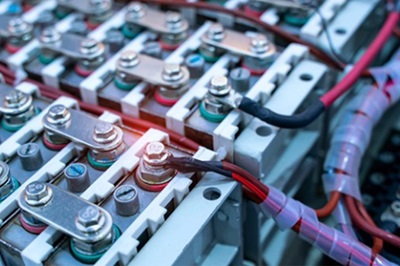
In this article we focus on Lithium batteries and their application
BESS systems can use a variety of battery types with relative advantages and disadvantages that are worth considering. For example, Lithium Iron Phosphate (LFP) batteries offer longer term deep cycle durability than Lithium polymer (LiPo) and they are resistant to dendrite growth so they pose no fire risk. Their day-one capacity is a little lower than LiPo, but after a few hundred cycles they'll hold up better in capacity.
Nickel-Manganese-Cobalt (NMC) batteries, on the other hand, have a shorter deep cycle life expectancy than LFPs but they offer increased power density and considerably better cold weather performance, particularly in charging, which can reduce operating overheads. It's for these reasons that NMC and LFP batteries are increasingly prevalent in BESS applications.
Lithium batteries function through electrochemical reactions involving lithium ions moving between the battery's positive (anode) and negative (cathode) electrodes, with material motion blocked by a separator that allows ion transport in the electrolyte. Lithium batteries typically contain a cathode (the +ve) formed from a lithium compound such as LiCoO2, NCA, NMC, LiFePO4 and LTO. These remain typical in the newer, solid-state embodiments.
An anode (the -ve) is usually made of carbon (graphite or graphene). Coatings applied to the electrodes aid as barriers to the formation of dendrites, metallic threads that form on the surface of the electrodes and can pierce the separator and cause short circuits. These coatings include polymers or ceramics, depending on the manufacturer. Between the electrodes there is typically:
- Electrolytes: There are three classes of electrolytes used in lithium battery technology including:
- Liquid electrolyte: A lithium salt dissolved in an organic solvent, often containing flame-retardant additives. The lithium salt is the ionic conductor that transfers charge; the organic solvent delivers high ionic motility and the additives optimize the stability, conductivity, and safety of the electrolyte.
- Polymer-based gel electrolytes: They deliver high ionic conductivity but a much-reduced chance of leakage. The polymer matrix acts as a gelling agent and, by design, they don’t pose a barrier to ionic motility within the solvent. The lithium salt acts in the same way, but gel-type cells offer improved battery safety and cycle life.
- Solid-state electrolytes: New alternatives to liquid electrolytes that improve safety and stability, acting as a barrier against dendrite formation and improving the thermal and chemical stability of the battery. This facilitates higher charge and discharge rates without increased risk.
- Separators: Porous membrane structures that force a physical gap between the anode and cathode, while allowing lithium ions to pass through during charge and discharge. Separators are generally constructed from high-porosity polyethylene (PE), often containing a polypropylene (PP) element to improve robustness.
During charging, lithium ions are electrically “pushed” from the positive electrode to the negative electrode through the electrolyte and become adsorbed onto/into the anode carbon. Electrons flow from anode to cathode in the outer circuit during charging. The charge current pushes electrons from anode to cathode. During discharge, these ions move back to the positive electrode, releasing electrical energy, and current flows in the outside circuit from cathode to anode. This ionic movement is greatly assisted by the crystalline structures within the electrode materials and energized by the flow of electrons through the external circuit in both charge and discharge.
The voltage and capacity of lithium batteries vary with the electrode/electrolyte chemistry and internal design, with voltages ranging from 3.6 V to 3.7 V per cell. Capacity relates to the amount of electrolyte and the size and construction of the electrodes. The discharge rate depends on many details and the internal safety systems in the cell and the battery. These prevent overcharging, over- discharging, and thermal runaway. Source

Caterpillar is announcing multiple technology and performance updates on the next generation Wheel Loaders to increase productivity and operating ease
The new auto front differential lock engages the differential lock to recover or maintain traction. Additionally, upgrades to both auto front and rear differential locks are options for the wheel loaders.
The auto lock is available on:
- All 950 to 972 models with joystick steering
- All 966 to 972 models with HMU (steering wheel) steering,
These medium wheel loaders feature improvements to the integrated brake system (IBS) and new engine RPM deceleration. The new transmission neutralizing features smooth engagement and disengagement with the IBS pedal.
A new standard job-aid widget helps the operator in load-and-carry operations by automatically placing the bucket at the optimal height for stability and maximum material retention. Now linked to the work tool centre, improvements to the zero-angle work tool widget enable the setting of different zero angles for different work tools and attachments.
Three programmable buttons on the implement control pod afford quicker access to regularly used functions to improve operating efficiency. Each operator can pull from over 25 different functions to customize and save their personal settings.
Key operating features – including Cat Payload, manual tip-off, neutralizer settings and tips, and application profiles – are now available in the on-board display system. A new option for Cat Advanced Payload, e-Ticketing, can send the generated on-board weighing ticket as an electronic ticket to any preprogrammed email address within seconds of finishing the loading cycle, reducing paper ticket handling in the cab.
A new optional tyre pressure measuring system shows the tyre pressure on the main machine display. Sensors transmit pressure information wirelessly to the system, and the desired target pressure can be adjusted based on tire type, manufacturer and model.
Cat Remote Flash and Remote Troubleshooting are standard features. Downloaded software update installations can now be initiated from the on-board display. Dealer remote troubleshooting functionalities have been expanded to include machine usage histograms and system calibrations. Preventative maintenance interval tracking can now be synchronized with VisionLink®, due-time reminders and overdue events are now shown to the operator on the display. Source
Tigercat product support grows in Western USA
Brady Lizotte joins product support team. Brady Lizotte is a heavy equipment professional based in Powell Butte, Oregon. Over the past nine years, he has worked in various industry sectors across the United States, including forestry, construction, oil and gas, agriculture and mining. His roles have included shop mechanic, field service technician and service manager. He recently moved to Central Oregon and will work with Regional Service Manager Damien Donoher to support the western US dealer network. Source
Ponsse is the most reputable listed company in Finland
According to a survey conducted by the Finnish Shareholders’ Association, the Finnish Foundation for Share Promotion and T-Media, the most reputable listed company in 2024 is Ponsse. The survey evaluated the reputation of 80 listed companies in the eyes of Finnish private investors. Ponsse is the only company in the survey to achieve an excellent reputation. The top three most reputable listed companies were Ponsse, KONE, and Gofore and Vaisala, sharing third place. Source
Read MoreTo see the full list of international logging, roading and trucking conferences and expo’s, please click the “Events” tab at the top of the page.
Read More