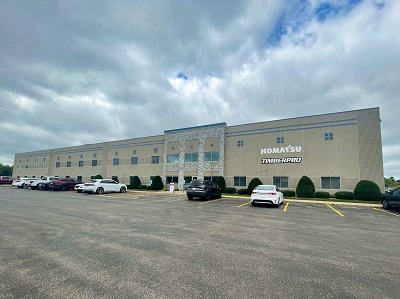
The expansion will allow the company to double production capacity.
TimberPro recently completed an $8 million expansion project that added nearly 49,000 ft2 (4,500 m2) to its facility in Shawano, Wisconsin, U.S. The expansion will allow the company to double production capacity, enabling it to meet growing market demand for its equipment and attachments.
To celebrate the project’s completion, TimberPro hosted a public open house on Friday, August 25, for employees, their families and members of the Shawano community. TimberPro was founded by Pat Crawford in 2002. The Crawfords have been involved in the forestry business in Wisconsin for more than 75 years, and in recognition of their contributions, the new expansion was dedicated to the family.
According to the Wisconsin Department of Natural Resources, the forest products industry provides more than 61,000 full- and part-time jobs in Wisconsin and has a total industry output of $24.4 billion. To help support regional jobs and the regional supply chain, TimberPro sources materials from many companies in northern Wisconsin. With its expanded operation, TimberPro currently has several new job openings for those seeking career opportunities in the rewarding equipment manufacturing industry. Access the TimberPro website to find out more information. Source
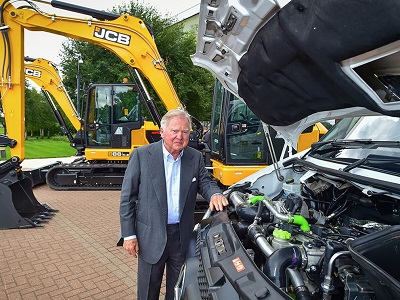
JCB has made a second major breakthrough in proving the wider appeal of hydrogen combustion technology.
This has been achieved by installing one of its super-efficient hydrogen engines into a Mercedes-Benz Sprinter van. The white van retrofit was completed in just two weeks and one of the vehicle’s first test drivers was JCB Chairman Anthony Bamford, who is leading the company’s £100 million hydrogen engine project.
The internal combustion engine used in the van is the same as those already powering prototype JCB construction and agricultural machines. It is the second Mercedes-Benz vehicle to be retrofitted with a JCB hydrogen engine; earlier this year a 7.5 tonne Mercedes-Benz truck was given the JCB hydrogen treatment.
JCB retrofitted this vehicle with a JCB hydrogen engine to demonstrate how simple it will be to convert existing vans and to show that it is not only construction and agricultural machines that can be powered by hydrogen. While converting vans will not be for JCB to do, it does prove there is something else other than batteries that can work very effectively.
JCB has already manufactured more than 70 hydrogen internal combustion engines in a project involving 150 British engineers and they now power prototype JCB backhoe loader and Loadall telescopic handler machines. The converted van was formerly diesel-powered and the switch to hydrogen is another breakthrough which underlines that this form of power could represent a much quicker way to reach global carbon dioxide emissions targets.
JCB is the developer of the world’s first working hydrogen-powered construction and agricultural machines. Last year JCB revealed another industry first – a mobile hydrogen refueller which provides a quick and straightforward way to refuel machines on site. JCB’s hydrogen internal combustion engines are manufactured at JCB Power Systems in Derbyshire. Source
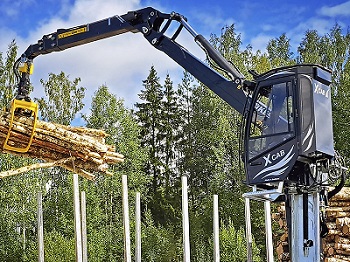
The package includes a crane with the Swedish X-Cab and Olsbergs control valve and full control system.
Finnish Kesla presents a new crane package for the Swedish market. Finnish Kesla is known worldwide for its timber cranes. Kesla offers cranes with various accessories, including the Kesla Vision cabin and Kesla proC control system. The company has now developed a crane package for the Swedish market to better serve its customers.
In Sweden, a large share of the cranes are sold as a complete package. Now, one can also get a Kesla crane as a complete package. The crane package includes the Olsbergs valve and control system, so Swedish customers can get their Kesla crane with the complete Olsbergs control feel they have wanted. Complementing the package, the Swedish X-Cab is highly customizable to each customer’s needs.
The new concept is available for the most popular 10- and 12-tonne straight-boom Kesla cranes. The cranes come ready-equipped, but most Kesla crane accessories and features are also available as an option for the concept models.
Since both X-Cab and Olsbergs are widely used in Sweden, the after-sales, spare parts, and technical support network are excellent. In addition to the new operating model, Kesla still has an active dealer network in Sweden, offering the entire range of cranes. Source
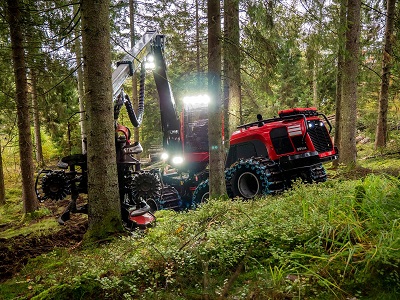
Logging-on recently introduced the Komatsu 951XC 8-wheeled harvester; we now provide more detail.
Demand for an eight-wheeled harvester for final logging has been high, resulting in the new Komatsu 951XC, a machine that combines tried and tested innovations with new solutions. The Komatsu 951XC is a final logging specialist and the third addition to Komatsu’s eight wheeled harvester range.
The challenge was to design a machine for harvesting large trees without making it too cumbersome. The 951XC combines the strength of a 951 with an extremely compact design. It has almost the same dimensions as a 931XC and so can even be used in denser stands.
The Komatsu 951XC is optimized for use with the Komatsu C164 – a harvester head specially designed for logging large trees. However, it also works just as well with the C144 head. This makes it a versatile machine with the capacity to harvest extremely large trees.
Thanks to the eight-wheel design, the 951XC delivers lower ground pressure, meaning less impact on the forest floor. It is mainly intended for final logging in hilly terrain and on soft ground. Another important factor when working in steep terrain is stability. The Komatsu 951XC has a number of features that make it one of the most stable harvesters on the market. The eight-wheeled XC series harvesters have a bogie on the rear frame with two suspension systems – comprised of the swinging rear axle and a bogie – giving the machines completely unique handling characteristics. As well as increasing stability by lowering the machine’s centre of gravity, the machine follows irregularities in the terrain in a forgiving manner while delivering good manoeuvrability in challenging terrain conditions.
The 951XC has a comfortable operator environment with a spacious cab, good visibility, and a pleasant cab climate. Thanks to the machine’s stability and levelling cab, the operator is always seated level without the need to stretch and strain to maintain a good seating position. A relaxed operator can keep their energy level up as well as maintain their focus and a high production rate for longer. If one chooses the Smart Crane option, one gets an even more easily maneuvered crane that delivers amazing precision. The parallel crane is fast in its outward movements, when the head is unloaded, and powerful in its return movements, when the head is heavily loaded. Source
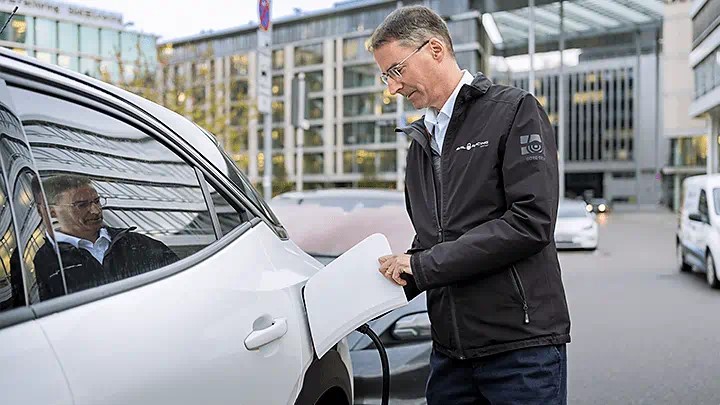
Trelleborg enters the discussion on which technologies will be appropriate to power the vehicles of the future.
Pick any data point and the growth of electric cars looks like a wildly successful phenomenon. The number of electric cars on the world’s roads hit 16.5 million at the end of 2021, according to the International Energy Agency (IEA). That is triple the number in 2018. Two million electric cars were sold in the first quarter of 2022 alone, three quarters more than the same period a year earlier.
Yet with such a rapid rate of growth come challenges. The price of critical minerals essential for battery manufacturing are soaring. Lithium prices, for example, the IEA said were seven times higher in May 2022 than they were at the beginning of 2022.
The expansion of charging infrastructure in many locations has failed to keep up with the growth in electric car sales, prompting hesitancy among potential buyers. Anxiety over the range of electric vehicles regularly crops up in consumer surveys, despite the industry’s best efforts to publicize how this has extended.
For many would-be buyers, questions over range and efficiency are only part of the picture. They focus on more mundane issues, such as where to charge an EV when living in an apartment block. That, according to Weimann, is becoming a redundant question. Employers across Europe are investing in charging infrastructure and gas stations are pivoting with installations of superchargers that can fuel 250 kilometers of range in just 25 minutes.
If you drive up to 250 kilometers (155 miles) per week, then you don’t need a charger at home. You can charge while you buy groceries or pop out for coffee with a friend. A change of mindset is required to see the opportunity of charging while parked and doing something meaningful rather than taking the extra ride to the filling station.”
The growth of EVs will place unprecedented demand on the national grid. To drive 100 miles (160 km), an EV uses the same amount of electricity as it does to power a typical US home for a day, according to the US Department of Energy. Yet, while EVs place significant demands on the grid, they can also be part of the solution. Smart charging technology known as “vehicle to grid” enables car batteries to give power back to the grid, taking some pressure off when demand is greatest. Plans to utilize the technology are already moving through the German parliament. This ‘breathing of energy’ is totally new and saves a huge amount of money on the grid because authorities don’t have to use their own storage capabilities. You can just use the fleet on the street.
Battery technology is now so advanced that it dominates the attention of governments and manufacturers. However, Weimann says that hydrogen power is developing quickly and holds advantages over electric vehicles in certain contexts, particularly heavy trucks.
Batteries weighing as much as two tonnes would be required to power standard-sized trucks, compared to a hydrogen fuel load weighing a quarter of that. That would ultimately cost the operator 1.5 tonnes of payload, and that is before you consider the slim prospect of finding super chargers outside of developed western economies. Hydrogen trucks have a window of opportunity for at least the next ten years.
That lack of infrastructure hints at the limitations facing e-mobility during the years ahead, and even points to a crisis for developing economies. Across China, the Americas and Western Europe, governments have set ambitious emissions reduction targets, which is fueling investment in infrastructure to support the growth of e-mobility.
Cars are built for huge markets. The countries who are lacking in charging infrastructure, or who don’t have the power to switch, are going to need help developing further. Otherwise, it won’t be long until there are no longer new cars available to these markets.
For now, manufacturers are focused on their domestic markets and it is working, but will everyone be willing to switch to electric vehicles? Car enthusiasts tend to be romantic about combustion engines. Whether they can be converted is perhaps the truest test of electric cars as products. Source
John Deere, Kreisel To Build Batteries and Chargers in Kernersville, North Carolina
Deere & Company announced it has selected a location in Kernersville, North Carolina, for the construction of a 115,000-square-foot manufacturing facility. The factory will expand production capacity of Kreisel Electric ("Kreisel") products. Kreisel, which John Deere acquired majority ownership of in 2022, produces innovative battery technology for e-mobility and stationary systems as well as comprehensive Level 3 charging solutions. The planned production facility can support a production capacity of up to 2 GWh. John Deere plans to break ground on the new facility in fall 2023, and production is estimated to begin in 2025. Source
John Deere reports solid 3rd quarter financial results
Worldwide net sales and revenues increased 12 percent, to $15.801 billion, for the third quarter of 2023 and rose 24 percent, to $45.839 billion, for nine months. Net sales were $14.284 billion for the quarter and $41.765 billion for nine months, compared with $13.000 billion and $33.565 billion last year. Deere continues to benefit from favourable market conditions and an operating environment showing further improvement. Source
Case introduces an All Makes Undercarriage Program
Case Construction Equipment has joined forces with Berco, a leading manufacturer of undercarriage components, on an expanded supplier agreement to bring you the All Makes Undercarriage Program. This collaboration takes the Case dealer network to new heights. With the All Makes Undercarriage Program, equipment owners can get quality, competitively priced undercarriage parts for all makes and models, including replacement options for non-Case machines. Berco allows you to order any size component in any quantity and customize track groups and track chains made to order. Source
Read MoreTo see the full list of international logging, roading and trucking conferences and expo’s, please click the “Events” tab at the top of the page.
Read More